Plasma-enhanced chemical vapor deposition (PECVD) offers a range of benefits that make it a preferred technique for thin film deposition in various industries. These advantages include the ability to deposit a wide variety of materials, control microstructure, achieve high deposition rates, and uniformly coat complex surfaces. Additionally, PECVD provides better quality and stability compared to other CVD techniques, along with faster growth rates. Its compatibility with vacuum processes and ability to operate at lower temperatures further enhance its appeal. Below, the key benefits of PECVD are explained in detail.
Key Points Explained:
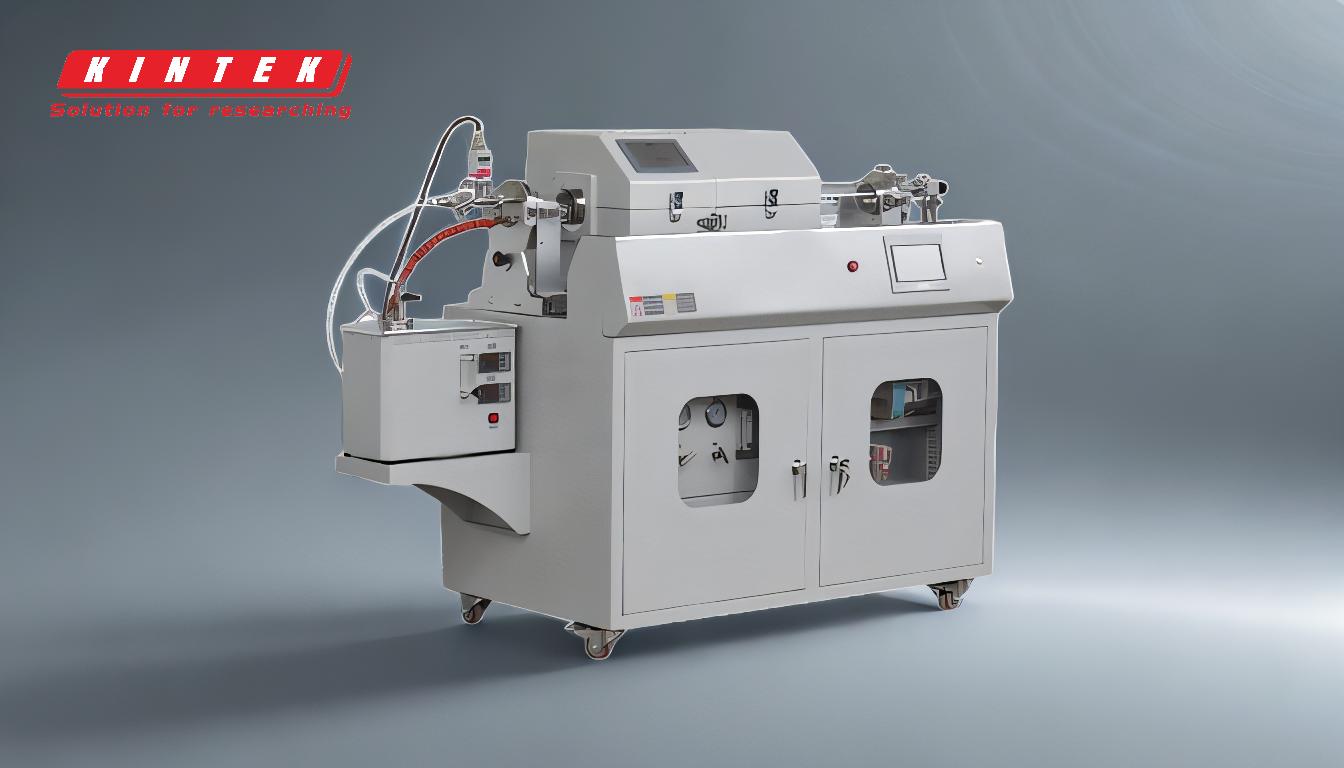
-
Versatility in Material Deposition
- PECVD can deposit a wide range of materials, including elemental, alloy, glassy, and compound materials. This versatility makes it suitable for diverse applications, from semiconductors to optoelectronics and protective coatings.
- The technique allows for the synthesis of both pure and complex materials at desired purity levels, making it ideal for industries requiring high-purity films.
-
Control Over Microstructure
- PECVD enables precise control over the microstructure of deposited films, ranging from amorphous to polycrystalline and even single-crystal structures. This control is crucial for tailoring the mechanical, electrical, and optical properties of the films to meet specific application requirements.
- The ability to adjust the chemical and physical properties of the films by controlling parameters such as temperature, pressure, and gas flow rate further enhances its utility.
-
High Deposition Rates
- PECVD offers significantly faster growth rates compared to other CVD techniques. For example, DC plasma jet systems can achieve rates of up to 930 µm/h, microwave plasma systems range from 3-30 µm/h, and RF plasma systems can reach 180 µm/h.
- These high deposition rates make PECVD a time-efficient process, which is particularly beneficial for large-scale production.
-
Uniform Coating of Complex Surfaces
- One of the standout advantages of PECVD is its ability to uniformly coat complex three-dimensional structures. This is essential for applications such as microelectronics, where step coverage and sidewall coverage are critical.
- The technique’s strong step coverage ability ensures consistent film thickness and quality, even on intricate geometries.
-
Improved Quality and Stability
- PECVD produces films with superior quality and stability compared to other CVD methods. The low-pressure environment used in PECVD improves film uniformity and reduces defects, resulting in higher performance and reliability.
- The smoother surfaces and better electrical and thermal conductivity of PECVD films make them ideal for advanced applications like electrical circuits and optoelectronic devices.
-
Lower Temperature Operation
- PECVD can be carried out at lower temperatures compared to traditional CVD methods. This is particularly advantageous for temperature-sensitive substrates and materials, as it minimizes thermal stress and degradation.
- Lower temperatures also allow for better control over the chemical composition and microstructure of the films, further enhancing their quality.
-
Compatibility with Vacuum Processes
- PECVD equipment is compatible with other vacuum-based processes, making it easy to integrate into existing production lines. This compatibility reduces the need for additional equipment and simplifies the manufacturing workflow.
- The vacuum environment also helps maintain high purity levels, which is critical for applications in the semiconductor and optoelectronics industries.
-
Cost-Effectiveness and Scalability
- PECVD is a cost-effective solution for producing high-purity films, especially in industries like semiconductors and optoelectronics. Its ability to scale up production without compromising quality makes it suitable for both research and industrial applications.
- The reduced CO2 footprint of PECVD compared to other deposition technologies also aligns with sustainability goals, making it an environmentally friendly choice.
In summary, plasma-enhanced CVD stands out as a highly versatile, efficient, and reliable technique for thin film deposition. Its ability to deposit a wide range of materials, control microstructure, achieve high deposition rates, and uniformly coat complex surfaces makes it indispensable in modern manufacturing and research. Additionally, its lower temperature operation, compatibility with vacuum processes, and cost-effectiveness further solidify its position as a leading deposition technology.
Summary Table:
Benefit | Description |
---|---|
Versatility | Deposits a wide range of materials, from elemental to complex compounds. |
Microstructure Control | Precise control over film structure (amorphous, polycrystalline, single-crystal). |
High Deposition Rates | Faster growth rates (up to 930 µm/h), ideal for large-scale production. |
Uniform Coating | Ensures consistent film thickness on complex 3D structures. |
Improved Quality & Stability | Produces high-quality, defect-free films with smooth surfaces. |
Lower Temperature Operation | Minimizes thermal stress, suitable for temperature-sensitive materials. |
Vacuum Compatibility | Easily integrates with other vacuum-based processes, ensuring high purity. |
Cost-Effectiveness | Scalable, eco-friendly, and cost-efficient for industrial applications. |
Unlock the potential of PECVD for your thin film needs—contact our experts today!