Biomass pyrolysis is a thermochemical process that converts biomass into valuable products such as biochar, bio-oil, and syngas. Catalysts play a crucial role in enhancing the efficiency and selectivity of this process. They promote desirable chemical reactions, improve product yields, and optimize the quality of the end products. Key catalysts for biomass pyrolysis include biochar-based catalysts, which are known for their ability to enhance the production of biofuels and chemicals. The effectiveness of these catalysts is influenced by factors such as temperature, residence time, and the physical and chemical properties of the biomass feedstock. Understanding these factors is essential for optimizing the pyrolysis process and achieving the desired outcomes.
Key Points Explained:
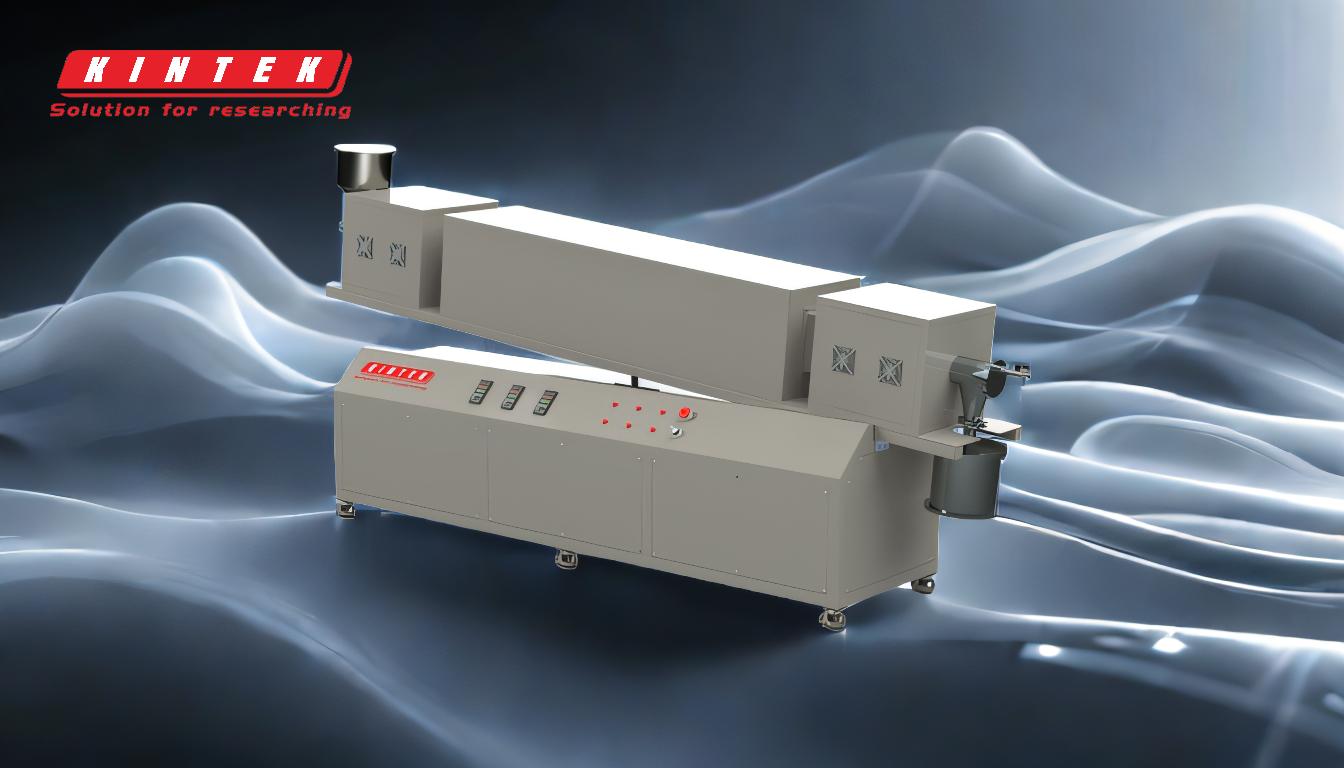
-
Role of Catalysts in Biomass Pyrolysis
- Catalysts are substances that accelerate chemical reactions without being consumed in the process. In biomass pyrolysis, catalysts promote the breakdown of complex organic molecules into simpler compounds, enhancing the yield and quality of the end products.
- Biochar-based catalysts are particularly effective in biomass pyrolysis. They improve the production of biofuels and chemicals by facilitating desirable reactions, such as cracking, reforming, and dehydrogenation.
-
Types of Catalysts Used in Biomass Pyrolysis
- Biochar-Based Catalysts: Derived from biomass itself, these catalysts are cost-effective and sustainable. They enhance the yield of bio-oil and syngas while improving the quality of biochar.
- Zeolites: These are microporous, aluminosilicate minerals that act as catalysts by providing a large surface area for chemical reactions. They are effective in cracking heavy hydrocarbons into lighter fractions.
- Metal Oxides: Catalysts such as alumina (Al₂O₃) and silica (SiO₂) are used to improve the selectivity of pyrolysis reactions, particularly in the production of syngas and bio-oil.
- Alkali and Alkaline Earth Metals: Potassium (K) and calcium (Ca) are commonly used as catalysts to enhance the decomposition of biomass and increase the yield of gaseous products.
-
Factors Influencing Catalyst Performance
- Temperature: The temperature of the pyrolysis process significantly affects the activity of catalysts. Higher temperatures generally increase the rate of catalytic reactions but may also lead to the degradation of certain products.
- Residence Time: The duration that biomass and catalysts remain in the pyrolysis reactor influences the extent of thermal decomposition and the composition of the end products.
- Biomass Properties: The type, moisture content, and particle size of the biomass feedstock affect the interaction between the biomass and the catalyst. Smaller particle sizes and lower moisture content generally improve catalytic efficiency.
- Heating Rate: Faster heating rates can enhance the effectiveness of catalysts by promoting rapid decomposition of biomass and reducing secondary reactions.
-
Impact of Catalysts on Pyrolysis Products
- Biochar: Catalysts can improve the quality of biochar by increasing its carbon content and stability. Biochar-based catalysts, in particular, enhance the porosity and surface area of the biochar, making it more suitable for applications such as soil amendment and carbon sequestration.
- Bio-Oil: Catalysts play a critical role in improving the yield and quality of bio-oil. They help reduce the viscosity and oxygen content of bio-oil, making it more suitable for use as a fuel.
- Syngas: Catalysts enhance the production of syngas (a mixture of hydrogen and carbon monoxide) by promoting gasification reactions. This is particularly important for applications in energy production and chemical synthesis.
-
Challenges and Future Directions
- Catalyst Deactivation: Over time, catalysts can become deactivated due to the deposition of carbon (coking) or the accumulation of impurities. Developing catalysts with higher resistance to deactivation is a key area of research.
- Sustainability: The use of sustainable and renewable catalysts, such as biochar-based catalysts, is gaining attention. These catalysts not only improve the efficiency of pyrolysis but also align with the principles of circular economy and environmental sustainability.
- Scalability: Scaling up the use of catalysts in industrial pyrolysis processes remains a challenge. Research is ongoing to develop cost-effective and scalable catalytic systems that can be integrated into large-scale biomass conversion facilities.
In summary, catalysts are essential for optimizing biomass pyrolysis, enhancing the yield and quality of biochar, bio-oil, and syngas. The choice of catalyst, along with process conditions such as temperature, residence time, and biomass properties, plays a critical role in determining the success of the pyrolysis process. Ongoing research aims to address challenges related to catalyst deactivation, sustainability, and scalability, paving the way for more efficient and environmentally friendly biomass conversion technologies.
Summary Table:
Key Catalysts | Role in Pyrolysis | Benefits |
---|---|---|
Biochar-Based Catalysts | Enhance bio-oil and syngas yield, improve biochar quality | Cost-effective, sustainable, improves porosity and surface area |
Zeolites | Crack heavy hydrocarbons into lighter fractions | Large surface area, effective for gas and oil production |
Metal Oxides | Improve selectivity in syngas and bio-oil production | Enhances reaction efficiency, optimizes product quality |
Alkali/Alkaline Metals | Increase gaseous product yield by enhancing biomass decomposition | Boosts syngas production, improves overall pyrolysis efficiency |
Ready to optimize your biomass pyrolysis process? Contact our experts today to learn more about the best catalysts for your needs!