Fast pyrolysis is a thermochemical process that rapidly decomposes biomass into valuable products such as bio-oil, syngas, and biochar. The efficiency and product distribution of fast pyrolysis are heavily influenced by catalysts, which play a crucial role in enhancing reaction rates, improving product yields, and controlling the composition of the output. Catalysts for fast pyrolysis are typically heterogeneous and are selected based on their ability to promote specific reactions, such as cracking, dehydration, and deoxygenation. Key catalysts include titanium compounds (e.g., TiN) and metal nitrides (e.g., GaN), which are particularly effective in producing furfural and other high-value compounds. The choice of catalyst depends on the desired product slate, feedstock properties, and process conditions such as temperature, heating rate, and residence time.
Key Points Explained:
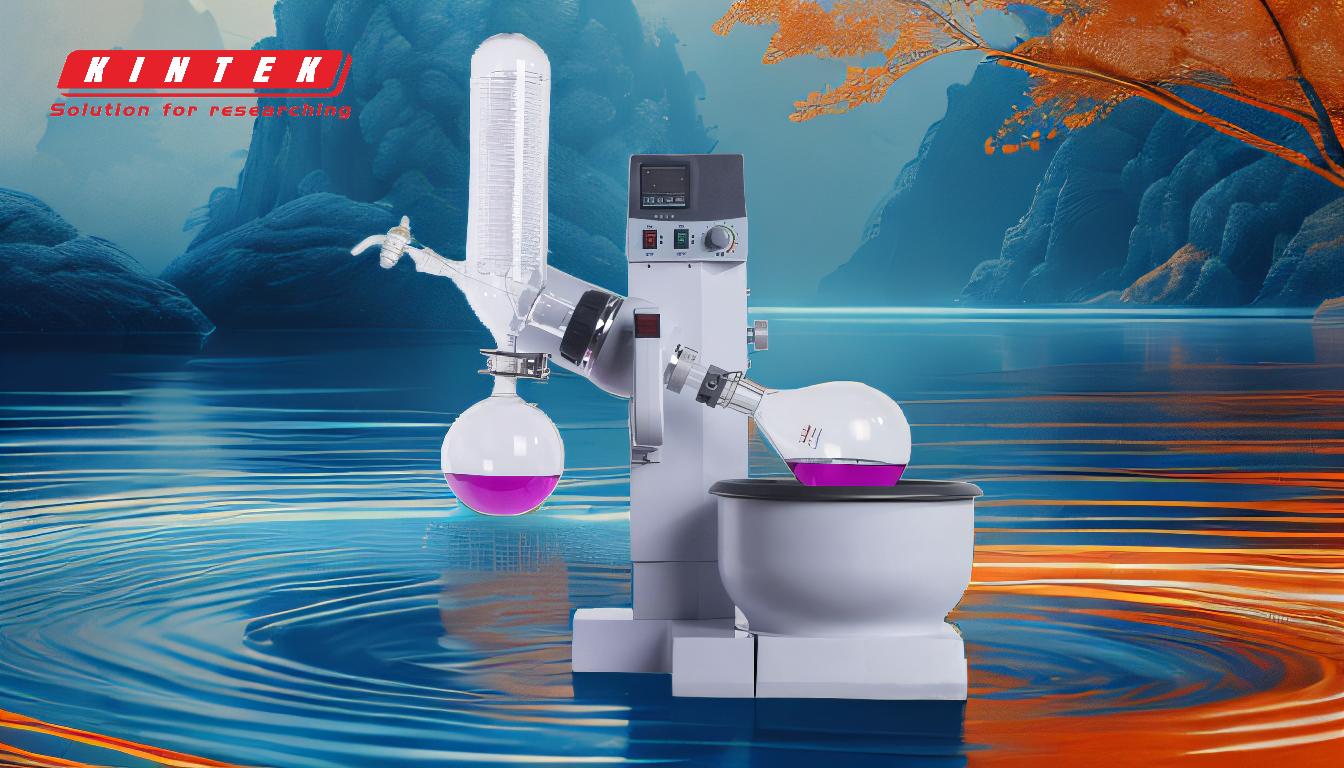
-
Role of Catalysts in Fast Pyrolysis:
- Catalysts in fast pyrolysis accelerate the decomposition of biomass by lowering activation energy and facilitating specific chemical reactions.
- They help optimize the yield and quality of pyrolysis products, such as bio-oil, syngas, and biochar, by controlling the reaction pathways.
- Catalysts can also reduce the formation of undesirable by-products, such as tar and char, by promoting selective reactions.
-
Types of Catalysts Used in Fast Pyrolysis:
- Heterogeneous Catalysts: These are solid catalysts that interact with the biomass feedstock during pyrolysis. Examples include titanium compounds (e.g., TiN) and metal nitrides (e.g., GaN).
- Metal Oxides: Certain metal oxides, such as alumina (Al₂O₃) and silica (SiO₂), are used to enhance cracking and deoxygenation reactions.
- Zeolites: These microporous materials are effective in cracking large hydrocarbon molecules into smaller, more valuable compounds.
-
Specific Catalysts for Furfural Production:
- Titanium Nitride (TiN): TiN is a highly effective catalyst for promoting the formation of furfural, a valuable chemical used in the production of resins, solvents, and biofuels.
- Gallium Nitride (GaN): GaN is another catalyst that enhances furfural yield by facilitating dehydration reactions of biomass-derived sugars.
-
Influence of Process Conditions on Catalyst Performance:
- Temperature: Optimal catalyst performance is achieved within specific temperature ranges. For example, TiN and GaN are most effective at moderate to high temperatures (400–600°C).
- Heating Rate: Faster heating rates can improve the interaction between the catalyst and biomass, leading to higher yields of desired products.
- Residence Time: Longer residence times allow for more complete reactions, but excessive times can lead to over-cracking and reduced product quality.
-
Feedstock Properties and Catalyst Selection:
- The composition of the biomass feedstock, including moisture content, fixed carbon, and volatile matter, influences the choice of catalyst.
- For example, feedstocks with high cellulose content may benefit from catalysts that promote dehydration reactions, while lignin-rich feedstocks may require catalysts that enhance cracking.
-
Advantages of Using Catalysts in Fast Pyrolysis:
- Increased yield of valuable products, such as bio-oil and furfural.
- Improved selectivity and reduced formation of unwanted by-products.
- Enhanced energy efficiency and reduced process costs due to faster reaction rates.
-
Challenges and Considerations:
- Catalyst deactivation due to coking or poisoning by impurities in the feedstock.
- High costs associated with some advanced catalysts, such as TiN and GaN.
- Need for catalyst regeneration or replacement, which can add operational complexity.
-
Future Directions in Catalyst Development:
- Research is focused on developing cost-effective, durable, and highly selective catalysts for fast pyrolysis.
- Advances in nanotechnology and materials science are enabling the design of catalysts with tailored properties for specific feedstocks and products.
- Integration of catalytic fast pyrolysis with other biorefinery processes, such as gasification and hydrotreating, is being explored to maximize resource utilization.
By understanding the role and selection of catalysts in fast pyrolysis, stakeholders can optimize the process to achieve higher yields of valuable products, reduce waste, and improve overall economic viability. The choice of catalyst should align with the specific goals of the pyrolysis process, such as maximizing bio-oil production or targeting specific chemicals like furfural.
Summary Table:
Aspect | Key Information |
---|---|
Role of Catalysts | Accelerate biomass decomposition, optimize product yields, reduce by-products. |
Types of Catalysts | Heterogeneous (e.g., TiN, GaN), metal oxides (e.g., Al₂O₃, SiO₂), zeolites. |
Furfural Production | TiN and GaN are highly effective for furfural yield enhancement. |
Process Conditions | Temperature (400–600°C), heating rate, and residence time influence catalyst performance. |
Feedstock Properties | Catalyst selection depends on moisture, fixed carbon, and volatile matter in biomass. |
Advantages | Increased product yield, improved selectivity, enhanced energy efficiency. |
Challenges | Catalyst deactivation, high costs, need for regeneration or replacement. |
Future Directions | Development of cost-effective, durable, and selective catalysts for tailored applications. |
Optimize your fast pyrolysis process with the right catalysts—contact our experts today for tailored solutions!