Physical vapor deposition (PVD) is a vacuum-based process used to deposit thin films and coatings onto substrates. It involves vaporizing a target material, transporting it in a vacuum environment, and condensing it onto a substrate to form a thin film. PVD is characterized by its ability to produce high-purity, durable coatings with excellent adhesion and surface quality. It is widely used in industries such as electronics, optics, and aerospace due to its precision, environmental friendliness, and versatility in coating various materials. The process is typically conducted at moderate temperatures and is known for its "line of sight" coating method, which ensures uniform and controlled deposition.
Key Points Explained:
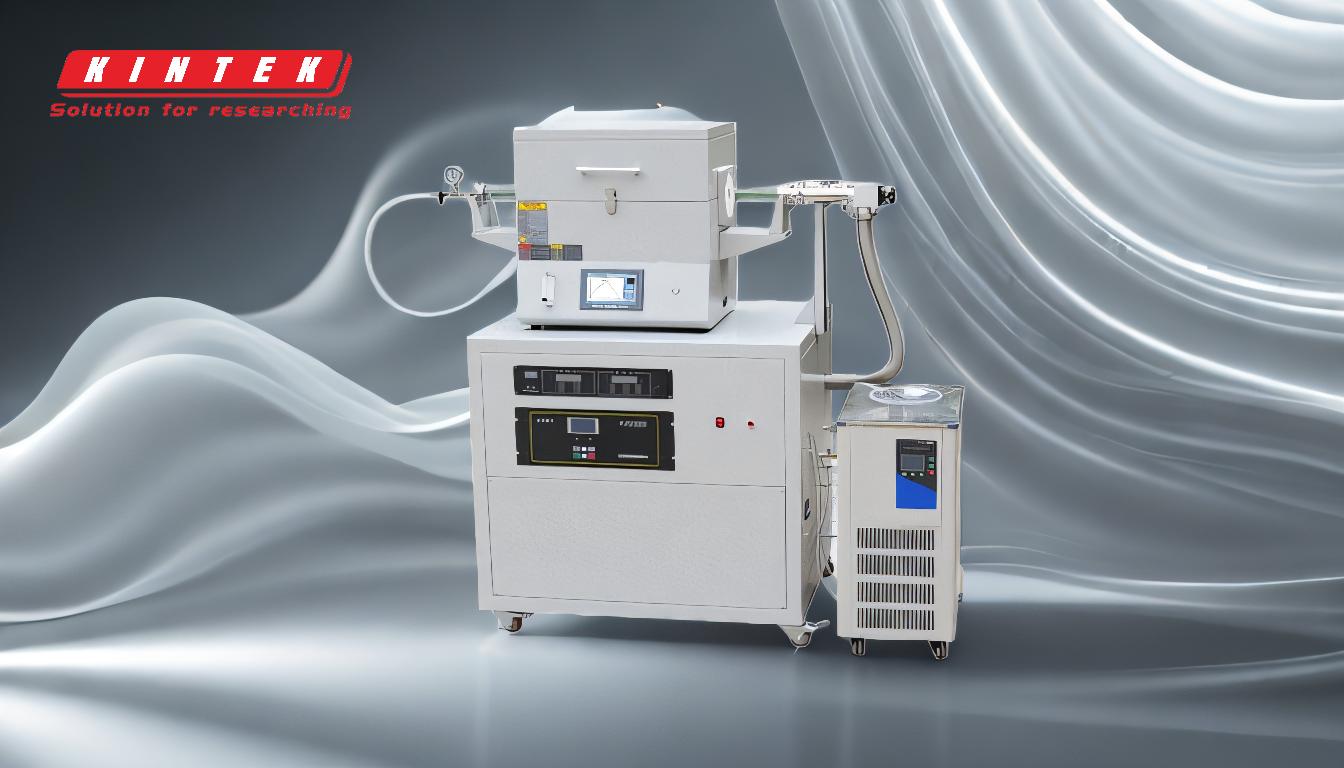
-
Vacuum-Based Process:
- PVD is conducted in a vacuum chamber to minimize contamination and ensure a clean deposition environment.
- The vacuum allows for precise control over the deposition process, resulting in high-quality, pure coatings.
-
Material Transition Phases:
- PVD involves three key phases: vaporization of the target material, transportation of the vaporized material, and condensation onto the substrate.
- The material transitions from a solid or liquid phase to a vapor phase and then back to a solid thin film on the substrate.
-
Common PVD Methods:
- Sputtering: Atoms are ejected from a solid target material due to bombardment by high-energy ions, forming a vapor that deposits onto the substrate.
- Thermal Evaporation: The target material is heated until it vaporizes, and the vapor condenses onto the substrate.
- Electron Beam Evaporation: An electron beam heats the target material, causing it to vaporize and deposit onto the substrate.
- Pulsed Laser Deposition (PLD): A high-power laser ablates the target material, creating a vapor that deposits onto the substrate.
-
Environmental Friendliness:
- PVD is considered environmentally friendly because it does not involve harmful chemicals or produce hazardous byproducts.
- The process is energy-efficient and produces minimal waste.
-
Coating Characteristics:
- Thickness: PVD coatings are typically very thin, ranging from 0.00004 to 0.0002 inches, making them suitable for applications requiring tight tolerances.
- Adhesion: The coatings have excellent adhesion to the substrate due to the physical bonding process.
- Surface Quality: PVD improves surface quality by providing smooth, uniform coatings that replicate the finish of the substrate.
-
Temperature Range:
- PVD processes are conducted at moderate temperatures, typically between 320 to 900 degrees Fahrenheit.
- This temperature range allows for the coating of heat-sensitive materials without causing damage.
-
Line of Sight Coating:
- PVD is a "line of sight" process, meaning the coating material travels in a straight line from the target to the substrate.
- This characteristic requires careful positioning of the substrate to ensure uniform coating coverage.
-
Versatility in Material Usage:
- PVD can deposit a wide range of materials, including metals, ceramics, and polymers.
- This versatility makes PVD suitable for various applications, from decorative coatings to functional layers in electronics.
-
No Heat Treatment Required:
- Unlike some other coating processes, PVD does not require post-deposition heat treatment.
- This simplifies the process and reduces production time.
-
Replication of Substrate Finish:
- PVD coatings replicate the finish of the substrate, making them ideal for applications where surface appearance is critical.
- This characteristic is particularly useful in decorative coatings and precision engineering.
In summary, PVD is a versatile, precise, and environmentally friendly process for depositing thin films and coatings. Its ability to produce high-quality, durable coatings with excellent adhesion and surface finish makes it a preferred choice in many industries. The process's vacuum-based nature, moderate temperature range, and "line of sight" coating method contribute to its effectiveness and widespread use.
Summary Table:
Key Aspect | Details |
---|---|
Process | Vacuum-based, involves vaporization, transportation, and condensation. |
Common Methods | Sputtering, Thermal Evaporation, Electron Beam Evaporation, Pulsed Laser Deposition (PLD). |
Coating Characteristics | Thin (0.00004–0.0002 inches), excellent adhesion, smooth surface quality. |
Temperature Range | 320–900°F, suitable for heat-sensitive materials. |
Environmental Impact | Energy-efficient, no harmful chemicals or hazardous byproducts. |
Applications | Electronics, optics, aerospace, decorative coatings, precision engineering. |
Discover how PVD can enhance your projects—contact our experts today for tailored solutions!