Chemical vapor deposition (CVD) is a versatile and widely used process for depositing thin films and coatings on substrates. It involves the transport of gaseous reactants to a substrate surface, where chemical reactions occur to form a solid material. The process is highly controllable and can be tailored to produce coatings with specific properties, such as corrosion resistance, abrasion resistance, or high purity. Key parameters in CVD include the choice of target materials, deposition technology, chamber pressure, and substrate temperature. These parameters influence the type and rate of material deposition, making CVD suitable for a wide range of applications, including the production of electrical circuits and coatings for precision and complex surfaces.
Key Points Explained:
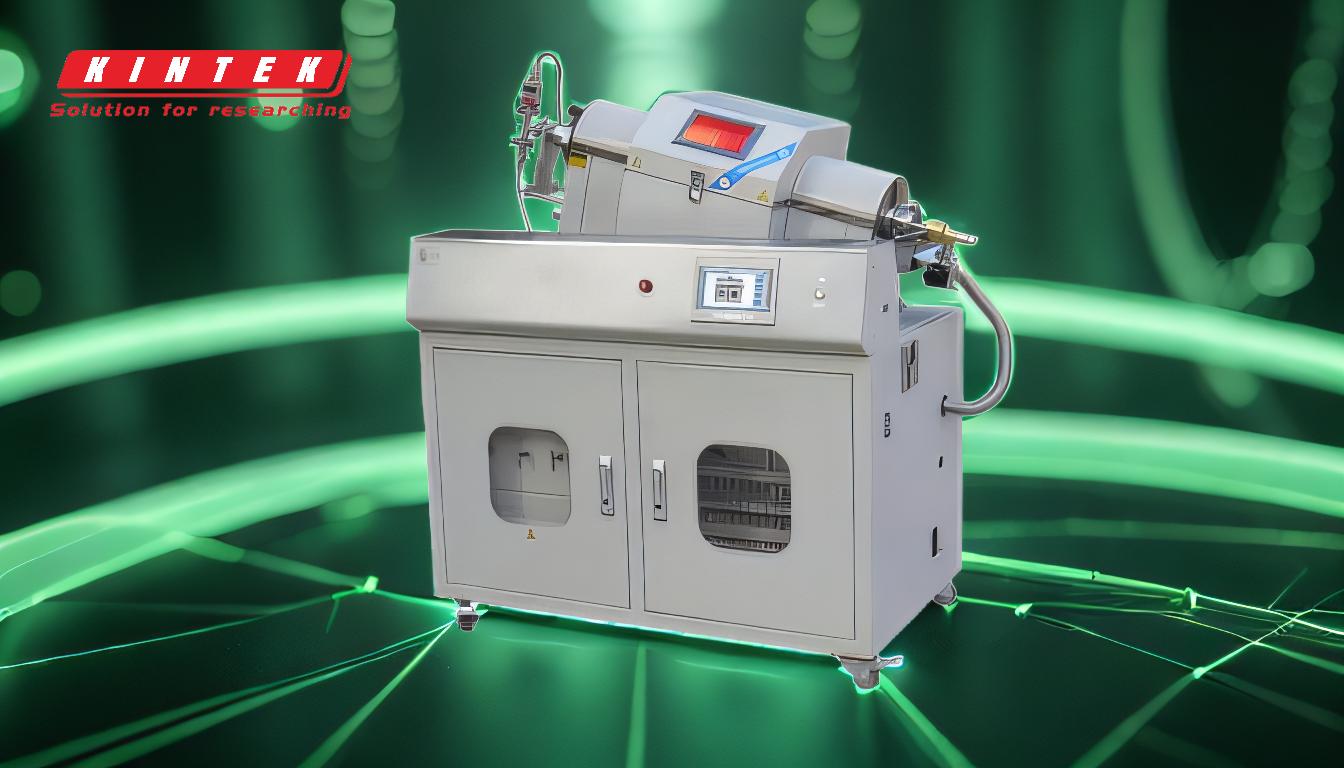
-
Steps in the Chemical Vapor Deposition Process:
- Transport of Reacting Gaseous Species: The process begins with the transport of gaseous reactants to the substrate surface. This step ensures that the necessary chemical species are available for the deposition process.
- Adsorption on the Surface: Once the gaseous species reach the substrate, they adsorb onto the surface. This step is crucial for the subsequent chemical reactions to occur.
- Heterogeneous Surface-Catalyzed Reactions: The adsorbed species undergo chemical reactions on the substrate surface, often catalyzed by the surface itself. These reactions lead to the formation of the desired material.
- Surface Diffusion and Growth: The reaction products diffuse across the surface to growth sites, where nucleation and growth of the film occur. This step determines the quality and uniformity of the deposited film.
- Desorption and Transport of By-Products: Finally, any gaseous by-products desorb from the surface and are transported away, completing the deposition cycle.
-
Major Steps in CVD:
- Evaporation of Volatile Compounds: The first step involves the evaporation of a volatile compound of the material to be deposited. This compound is transported to the substrate in the vapor phase.
- Thermal Decomposition and Chemical Reactions: The vaporized compound decomposes into atoms and molecules, often in the presence of heat. These species may react with other gases, vapors, or liquids near the substrate to form the desired material.
- Deposition of Nonvolatile Reaction Products: The nonvolatile reaction products deposit on the substrate, forming a thin film or coating.
-
Methods of Chemical Vapor Deposition:
- Chemical Transport Method: This method involves the transport of a solid material in the form of a volatile compound, which is then decomposed or reacted to form the desired deposit.
- Pyrolysis Method: In this method, a precursor compound is thermally decomposed at high temperatures to deposit the desired material on the substrate.
- Synthesis Reaction Method: This method involves the reaction of two or more gaseous precursors to form the desired material on the substrate.
-
Advantages of Chemical Vapor Deposition:
- Versatility: CVD can be used to deposit a wide range of materials, including ceramics, metals, and glass. The process can be tailored to produce coatings with specific properties.
- Control Over Process Timing: The timing of the CVD process can be precisely controlled, allowing for the deposition of ultra-thin layers with high precision.
- Durable Coatings: CVD coatings are highly durable and can withstand high-stress environments, making them suitable for demanding applications.
- Complex Surface Coating: CVD can be used to coat precision and complex surfaces, ensuring uniform coverage even on intricate geometries.
- Temperature Resistance: CVD coatings maintain their properties even when exposed to extreme temperatures or temperature variations.
-
Key Chemical Process Elements in CVD:
- Target Materials: The choice of target materials is critical in CVD. These materials can range from metals to semiconductors and determine the properties of the deposited film.
- Deposition Technology: Various deposition technologies, such as electron beam lithography (EBL), atomic layer deposition (ALD), atmospheric pressure chemical vapor deposition (APCVD), and plasma-enhanced chemical vapor deposition (PECVD), can be used in CVD. Each technology offers unique advantages and is suited to specific applications.
- Chamber Pressure: The pressure inside the deposition chamber affects the rate and type of material deposition. Lower pressures often result in higher-quality films with fewer defects.
- Substrate Temperature: The temperature of the substrate plays a crucial role in the deposition process. Higher temperatures can enhance the rate of chemical reactions and improve film quality, but must be carefully controlled to avoid damaging the substrate.
In summary, chemical vapor deposition is a highly versatile and controllable process for depositing thin films and coatings. The key parameters, including target materials, deposition technology, chamber pressure, and substrate temperature, play a critical role in determining the quality and properties of the deposited material. By carefully controlling these parameters, CVD can be used to produce coatings with specific properties, making it suitable for a wide range of applications.
Summary Table:
Parameter | Description |
---|---|
Target Materials | Determines the properties of the deposited film (e.g., metals, semiconductors). |
Deposition Technology | Includes methods like PECVD, APCVD, ALD, and EBL for tailored applications. |
Chamber Pressure | Influences deposition rate and film quality; lower pressure reduces defects. |
Substrate Temperature | Controls reaction rates and film quality; must be carefully managed. |
Ready to optimize your CVD process? Contact our experts today for tailored solutions!