A pyrolysis plant is a complex system designed to thermally decompose organic materials in the absence of oxygen, producing valuable by-products such as bio-oil, syngas, and biochar. The core components of a pyrolysis plant include the reactor, feeding system, heating system, discharging system, and emission control systems. These components work together to ensure efficient waste treatment and resource recovery. The design of the plant may vary depending on the specific application, such as whether the goal is to produce solid, liquid, or gaseous products. Advanced systems also incorporate energy recovery and emission control mechanisms to enhance sustainability and compliance with environmental standards.
Key Points Explained:
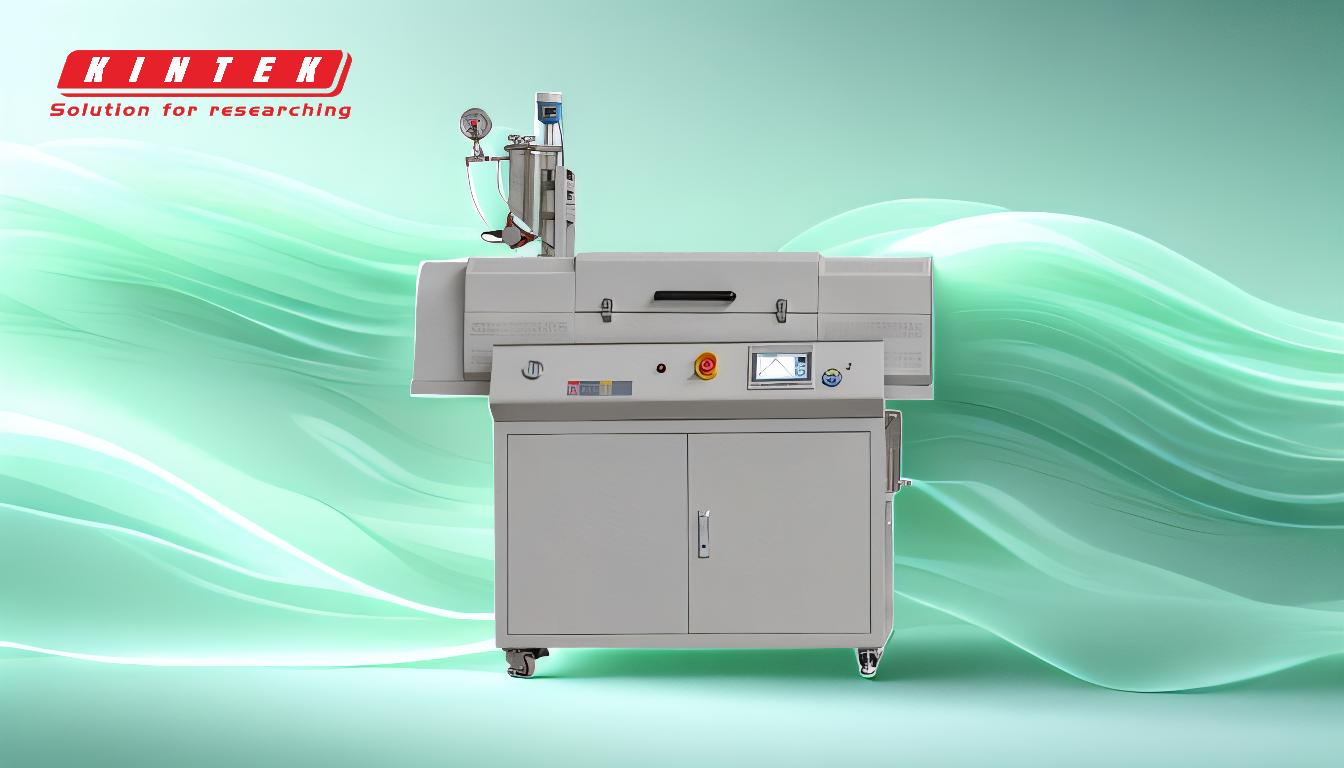
-
Reactor (Pyrolysis Chamber)
- The reactor is the core component where the pyrolysis process occurs. It is designed to withstand high temperatures and is typically made of high-quality materials to ensure durability and efficiency.
- In batch processes, the reactor is often referred to as a retort. It is where the raw materials are thermally decomposed into smaller molecules, producing biochar, bio-oil, and syngas.
- Some designs integrate the reactor with the energy module (furnace) to minimize energy losses, although this requires precise temperature control and robust construction materials.
-
Feeding System
- The feeding system is responsible for delivering raw materials into the reactor in a controlled and automated manner. It ensures a continuous supply of feedstock, which is crucial for maintaining the efficiency of the pyrolysis process.
- The system is fully sealed to prevent the escape of gases and to maintain the oxygen-free environment necessary for pyrolysis.
-
Heating System (Energy Module/Furnace)
- The heating system provides the thermal energy required to initiate and sustain the pyrolysis reactions. It can be powered by external energy sources or by recycling combustible gases produced during the process.
- In some designs, the furnace is combined with the reactor to reduce energy losses, although this complicates temperature regulation.
-
Condenser
- The condenser is used to cool and liquefy the vapor-gas mixture produced during pyrolysis, resulting in the production of bio-oil. This component is essential if the goal is to recover liquid products.
- In systems designed solely for solid product recovery, the condenser may be omitted, and the vapor-gas mixture is burned in the furnace for energy recovery.
-
Discharging System
- The discharging system handles the removal of solid residues, such as biochar, from the reactor. It often includes a water-cooling mechanism to lower the temperature of the biochar before storage or further processing.
- This system ensures the continuous operation of the pyrolysis plant by efficiently managing the output of solid products.
-
Syn-Gas Recycling System
- The syn-gas recycling system captures and recycles the combustible gases (syngas) produced during pyrolysis. These gases can be used to heat the reactor, reducing the need for external energy sources and enhancing the overall energy efficiency of the plant.
- This system is crucial for optimizing the energy balance and sustainability of the pyrolysis process.
-
De-Dusting System (Emission Cleaning Line)
- The de-dusting system is responsible for purifying the emission gases to meet environmental standards, such as those set by the EU. It removes particulate matter and other pollutants from the exhaust gases before they are released into the atmosphere.
- This component is essential for ensuring that the pyrolysis plant operates in an environmentally friendly manner.
-
Emission Cleaning Line
- In biomass pyrolysis plants, the emission cleaning line is specifically designed to handle the purification of gases released during the process. It ensures compliance with environmental regulations and minimizes the plant's ecological footprint.
-
Biomass Pyrolysis Line
- This line refers to the entire process chain in a biomass pyrolysis plant, from feeding the raw materials to discharging the final products. It includes all the necessary components to ensure efficient and sustainable pyrolysis of biomass materials.
By integrating these components, a pyrolysis plant can effectively convert waste materials into valuable resources while minimizing environmental impact. The specific configuration and design of the plant will depend on the intended application and the types of products to be recovered.
Summary Table:
Component | Function |
---|---|
Reactor (Pyrolysis Chamber) | Core unit for thermal decomposition, producing biochar, bio-oil, and syngas. |
Feeding System | Delivers raw materials into the reactor in a sealed, automated manner. |
Heating System (Furnace) | Provides thermal energy, often recycling combustible gases for efficiency. |
Condenser | Cools vapor-gas mixture to produce bio-oil (optional for solid recovery). |
Discharging System | Removes and cools biochar for storage or further processing. |
Syn-Gas Recycling System | Captures and recycles syngas to heat the reactor, enhancing energy balance. |
De-Dusting System | Purifies emission gases to meet environmental standards. |
Emission Cleaning Line | Ensures compliance with regulations in biomass pyrolysis plants. |
Biomass Pyrolysis Line | Full process chain for efficient and sustainable biomass pyrolysis. |
Ready to transform waste into valuable resources? Contact us today to learn more about our pyrolysis solutions!