Pyrolysis is a thermochemical process that decomposes organic materials at elevated temperatures in the absence of oxygen. This process is widely used to convert waste materials, biomass, and other carbon-based substances into smaller molecules, liquids (such as pyrolysis oil or bio-oil), and gaseous products. The conditions for pyrolysis include specific temperature ranges, an oxygen-free environment, and often the application of pressure. The process is irreversible and involves the breakdown of chemical bonds due to thermal instability, leading to the formation of new compounds. Understanding these conditions is crucial for optimizing pyrolysis processes in industrial applications.
Key Points Explained:
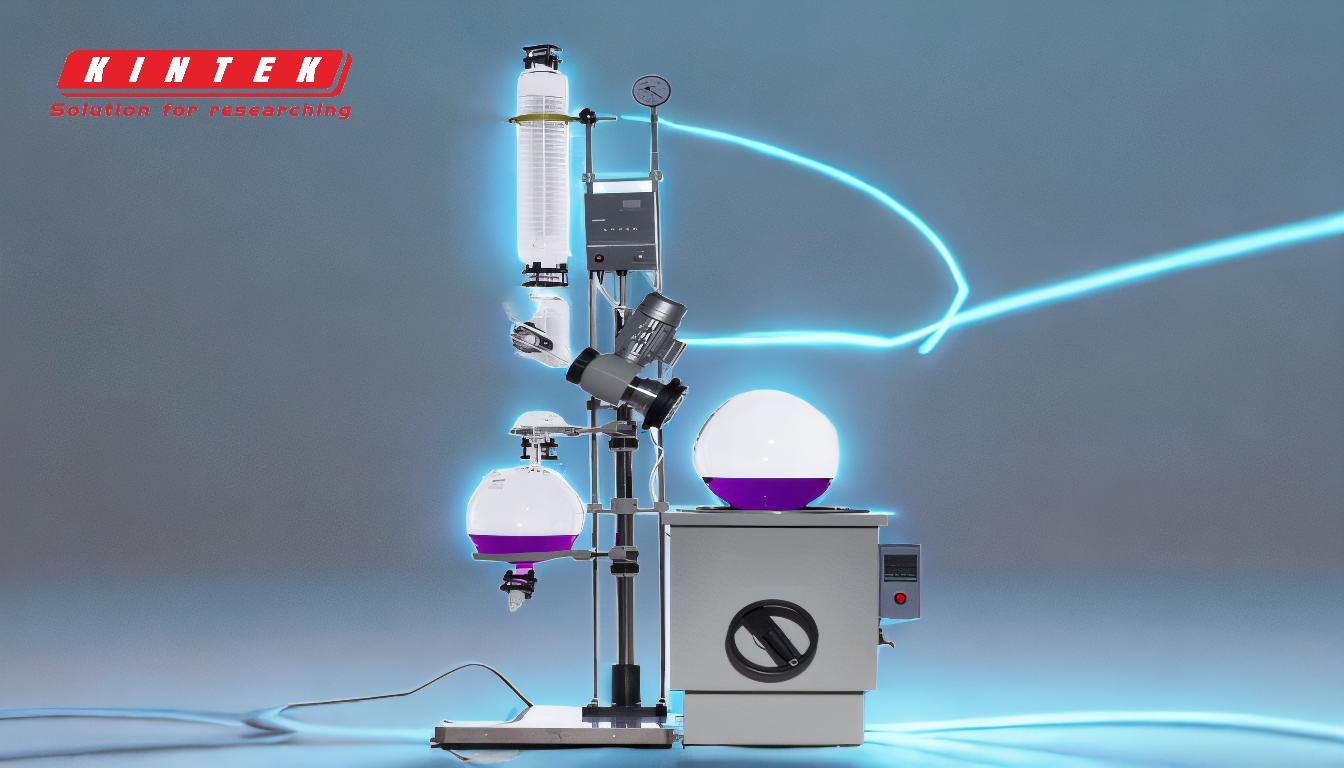
-
Temperature Range:
- Pyrolysis typically occurs within a temperature range of 350°C to 800°C, depending on the material being processed and the desired end products.
- Lower Temperature Range (350°C–550°C): Suitable for producing bio-oil and other liquid products.
- Higher Temperature Range (700°C–800°C): Often used for producing gaseous products and solid residues like char.
- The temperature must be carefully controlled to ensure efficient decomposition of the material without combustion, which requires oxygen.
- Pyrolysis typically occurs within a temperature range of 350°C to 800°C, depending on the material being processed and the desired end products.
-
Absence of Oxygen:
- Pyrolysis requires an oxygen-free environment to prevent combustion and ensure the decomposition of organic materials into smaller molecules.
- The process is carried out in a non-reactive atmosphere, such as nitrogen or other inert gases, to avoid oxidation reactions.
- The absence of oxygen allows the material to break down thermally rather than burn, leading to the formation of pyrolysis oil, gases, and char.
-
Pressure Conditions:
- Pyrolysis often occurs under pressure, which helps in controlling the reaction rates and the distribution of end products.
- Pressure can influence the yield and quality of the pyrolysis oil and gaseous products, making it an important variable in industrial applications.
-
Material Characteristics:
- Pyrolysis can be applied to any organic (carbon-based) material, whether pure or mixed.
- The thermal stability of the material's chemical bonds determines the efficiency of the process. Materials with weaker bonds decompose more readily at lower temperatures.
- Common feedstocks include biomass, plastics, rubber, and other waste materials.
-
Irreversible Process:
- Pyrolysis is an irreversible process, meaning the original material cannot be recovered once it has undergone thermal decomposition.
- The process involves simultaneous and successive reactions that lead to the formation of new compounds, such as pyrolysis oil, syngas, and solid residues.
-
End Products:
- The primary products of pyrolysis include:
- Pyrolysis Oil (Bio-Oil): A liquid product used as a fuel or chemical feedstock.
- Gaseous Products: Such as syngas (a mixture of hydrogen, carbon monoxide, and methane), which can be used for energy generation.
- Solid Residues: Such as char or biochar, which can be used as a soil amendment or fuel.
- The primary products of pyrolysis include:
-
Industrial Applications:
- Pyrolysis is widely used in industries for:
- Waste Management: Converting waste materials into valuable products.
- Energy Production: Generating biofuels and syngas.
- Chemical Production: Producing chemicals and feedstocks from organic materials.
- Pyrolysis is widely used in industries for:
-
Process Optimization:
- The efficiency of pyrolysis depends on optimizing factors such as:
- Temperature Control: Ensuring the material is heated uniformly to the desired temperature range.
- Residence Time: The duration the material spends in the reactor, which affects the extent of decomposition.
- Feedstock Preparation: Proper sizing and drying of the feedstock to improve reaction efficiency.
- The efficiency of pyrolysis depends on optimizing factors such as:
By understanding and controlling these conditions, pyrolysis can be effectively utilized to convert organic materials into valuable products, contributing to waste reduction, energy production, and sustainable industrial practices.
Summary Table:
Key Condition | Description |
---|---|
Temperature Range | 350°C–800°C; lower for bio-oil, higher for gases and char. |
Absence of Oxygen | Requires an oxygen-free environment to prevent combustion. |
Pressure Conditions | Often occurs under pressure to control reaction rates and product distribution. |
Material Characteristics | Works with any carbon-based material, including biomass and plastics. |
Irreversible Process | Original material cannot be recovered; forms new compounds. |
End Products | Pyrolysis oil, syngas, and solid residues (char/biochar). |
Industrial Applications | Waste management, energy production, and chemical feedstock generation. |
Process Optimization | Controlled temperature, residence time, and feedstock preparation. |
Ready to optimize your pyrolysis process? Contact our experts today for tailored solutions!