Plastic pyrolysis is a thermal decomposition process that converts waste plastic into useful products like fuel oil, carbon black, and syngas in the absence of oxygen. The efficiency and quality of pyrolysis depend on several key factors, including temperature, residence time, feedstock quality, and reactor conditions. Higher temperatures generally increase gas production, while lower temperatures favor solid products. The type of plastic, its cleanliness, and particle size also significantly influence the yield and composition of the pyrolysis products. Understanding these conditions is crucial for optimizing the process and achieving desired outcomes.
Key Points Explained:
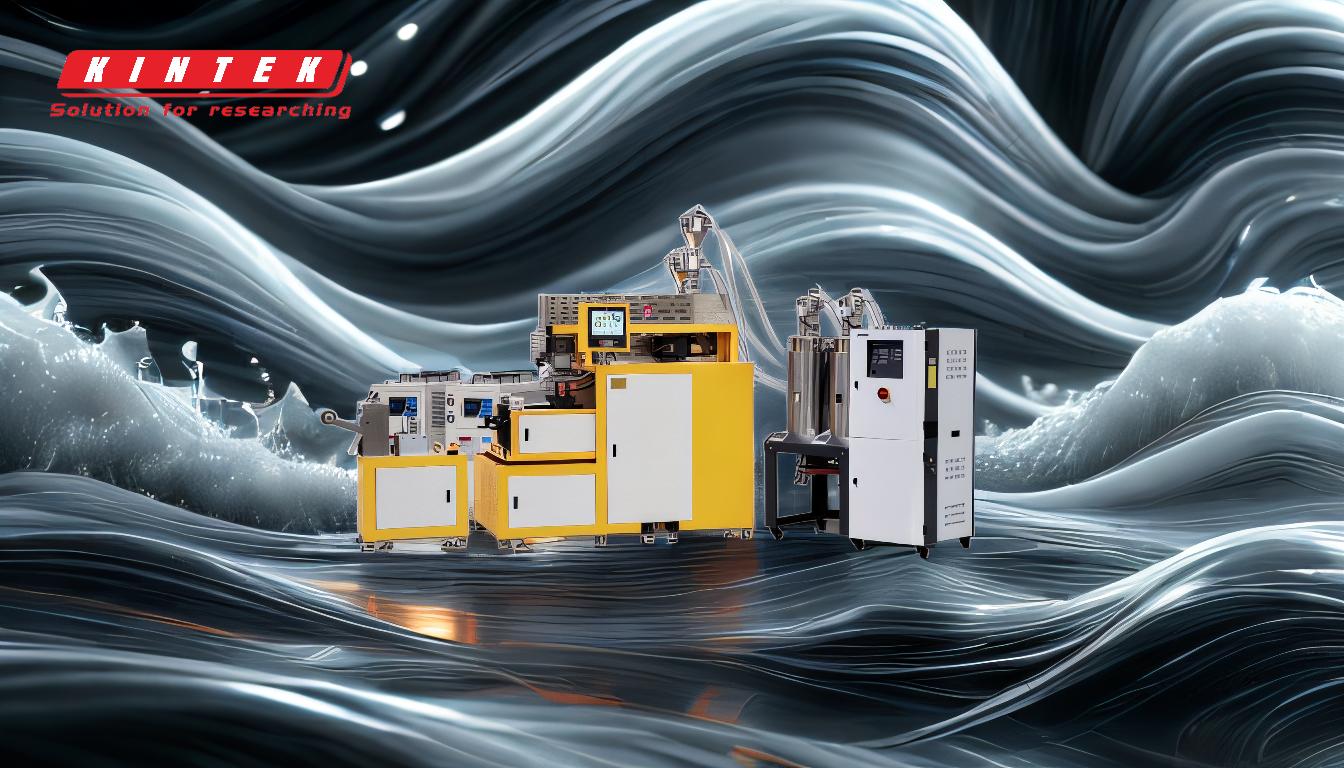
-
Temperature:
- Temperature is one of the most critical factors in plastic pyrolysis. It determines the breakdown of plastic molecules and the distribution of pyrolysis products (gas, liquid, and solid).
- Higher temperatures (typically above 400°C) favor the production of non-condensable gases, such as syngas (a mixture of hydrogen and carbon monoxide).
- Lower temperatures (around 300-400°C) are more suitable for producing high-quality liquid fuels (pyrolysis oil) and solid residues like carbon black.
- The optimal temperature range depends on the type of plastic being processed. For example, polyethylene and polypropylene degrade at different temperatures.
-
Residence Time:
- Residence time refers to the duration the plastic material spends in the pyrolysis chamber.
- Longer residence times allow for more complete thermal decomposition, leading to higher yields of gas and liquid products.
- Shorter residence times may result in incomplete decomposition, leaving behind more solid residue.
- The ideal residence time varies based on the reactor design and the specific type of plastic being processed.
-
Feedstock Quality:
- The quality of the waste plastic feedstock significantly impacts the pyrolysis process and product yield.
- Clean, dry, and pure plastic waste generally produces higher yields of pyrolysis oil and gas.
- Contaminants such as moisture, dirt, or non-plastic materials (e.g., metals or fibers) can reduce the efficiency of the process and affect the quality of the end products.
- Pretreatment steps, such as shredding or cleaning the plastic, can improve feedstock quality and process outcomes.
-
Reactor Conditions:
- The type of reactor and its operating conditions play a crucial role in determining the efficiency and product distribution of pyrolysis.
- Common reactor types include fixed-bed, fluidized-bed, and rotary kiln reactors, each with its own advantages and limitations.
- Factors such as heating rate, pressure, and atmosphere (e.g., inert gas like nitrogen) influence the pyrolysis process.
- For example, a faster heating rate can lead to higher yields of liquid products, while slower heating rates may favor solid residue formation.
-
Type of Plastic:
- Different types of plastics have varying chemical structures and decomposition behaviors, which affect the pyrolysis process.
- Polyethylene (PE) and polypropylene (PP) are commonly used in pyrolysis due to their high yields of liquid fuels.
- Polyvinyl chloride (PVC) and polystyrene (PS) require careful handling due to the release of harmful gases like chlorine or styrene during pyrolysis.
- The choice of plastic feedstock should align with the desired end products and the capabilities of the pyrolysis system.
-
Particle Size and Physical Structure:
- Smaller particle sizes and uniform physical structures enhance the efficiency of thermal decomposition.
- Smaller particles heat up more quickly and evenly, leading to faster and more complete pyrolysis.
- Larger or irregularly shaped particles may result in uneven heating and incomplete decomposition, reducing the overall yield and quality of the products.
-
Atmosphere:
- Pyrolysis must be conducted in an oxygen-free environment to prevent combustion and ensure the breakdown of plastic into useful products.
- An inert atmosphere, typically achieved using nitrogen or argon gas, is essential for maintaining the desired chemical reactions.
- The absence of oxygen prevents the formation of unwanted byproducts, such as carbon dioxide and water, which can reduce the quality of the pyrolysis oil and gas.
-
Pressure:
- While pyrolysis is often conducted at atmospheric pressure, variations in pressure can influence the process.
- Higher pressures may increase the yield of certain products, such as liquid fuels, by altering the reaction kinetics.
- However, pressure control is less critical than temperature and residence time in most pyrolysis systems.
By carefully controlling these factors, the pyrolysis process can be optimized to maximize the yield and quality of valuable products like pyrolysis oil, syngas, and carbon black. This makes plastic pyrolysis a promising solution for waste management and resource recovery.
Summary Table:
Factor | Impact on Pyrolysis |
---|---|
Temperature | Higher temps favor gas production; lower temps favor liquid and solid products. |
Residence Time | Longer times increase gas and liquid yields; shorter times leave more solid residue. |
Feedstock Quality | Clean, dry, and pure plastics yield higher-quality products. |
Reactor Conditions | Reactor type, heating rate, and atmosphere influence product distribution. |
Type of Plastic | PE and PP yield more liquid fuels; PVC and PS require careful handling. |
Particle Size | Smaller particles heat evenly, improving decomposition efficiency. |
Atmosphere | Oxygen-free environments prevent combustion and ensure high-quality products. |
Pressure | Higher pressures may increase liquid fuel yields but are less critical than temperature. |
Optimize your plastic pyrolysis process today—contact our experts for tailored solutions!