Slow pyrolysis is a thermal decomposition process that occurs in an oxygen-limited or oxygen-free environment, typically at lower temperatures (around 400 °C) and with longer residence times (several hours). The process is designed to maximize the production of biochar, a solid carbon-rich material, while also generating bio-gas and bio-oil as by-products. Key conditions for slow pyrolysis include controlled heating rates (1–30 °C/min), atmospheric pressure, and proper feedstock preparation (drying and mechanical comminution). The efficiency and product yield depend on factors such as biomass type, moisture content, pyrolysis temperature, and residence time. External energy sources, such as combustion of produced gases or partial combustion of the feedstock, are often used to supply process heat.
Key Points Explained:
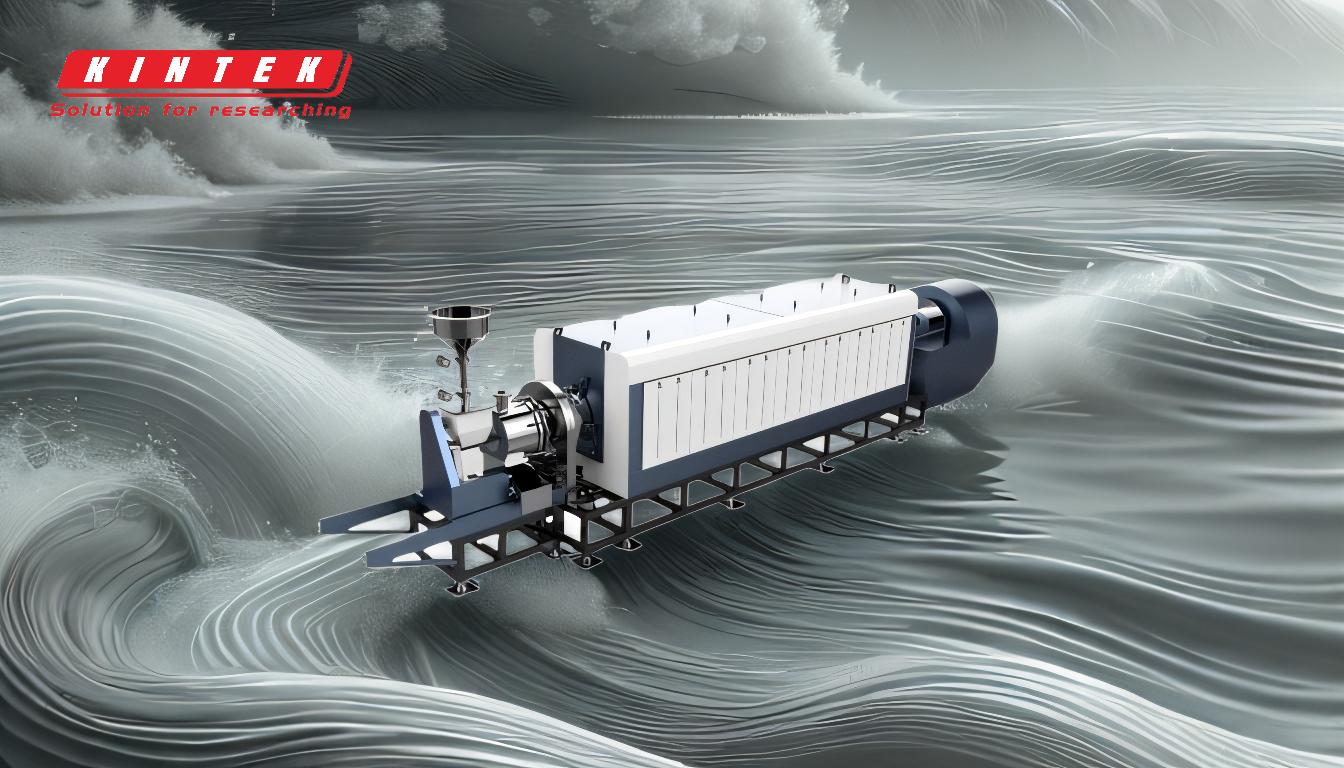
-
Oxygen-Limited or Oxygen-Free Environment
- Slow pyrolysis requires an environment with limited or no oxygen to prevent combustion and ensure thermal decomposition.
- This condition is critical for producing biochar, as oxygen exposure would lead to oxidation and loss of carbon content.
-
Temperature Range
- The process typically operates at lower temperatures, around 400 °C.
- Temperatures above 270 °C initiate biomass degradation, but the optimal range for slow pyrolysis ensures maximum biochar yield while minimizing energy loss.
-
Heating Rates
- Slow pyrolysis uses controlled heating rates, typically between 1 and 30 °C per minute.
- Slower heating rates allow for more complete carbonization and higher biochar production.
-
Residence Time
- Longer residence times (several hours) are a hallmark of slow pyrolysis.
- This extended duration ensures thorough thermal decomposition of the biomass, leading to higher biochar yields and more stable end products.
-
Atmospheric Pressure
- Slow pyrolysis is usually conducted at atmospheric pressure.
- This simplifies the reactor design and reduces operational costs compared to processes requiring high-pressure environments.
-
Feedstock Preparation
- Biomass must be prepared by drying and mechanical comminution (reducing particle size).
- Proper preparation ensures uniform heating and efficient decomposition during pyrolysis.
-
Energy Source for Process Heat
- External energy sources, such as combustion of produced gases or partial combustion of the feedstock, are often used to supply heat.
- This ensures the process is self-sustaining and reduces reliance on external energy inputs.
-
Factors Influencing Efficiency and Yield
- Biomass Type and Moisture Content: Different feedstocks (e.g., wood, agricultural residues) have varying pyrolysis behaviors. Low moisture content is essential to avoid energy loss from water evaporation.
- Pyrolysis Temperature and Residence Time: These are the most critical factors affecting biochar yield and properties.
- Vapor Residence Time: Longer vapor residence times can influence the composition of bio-gas and bio-oil.
-
End Products
- The primary product of slow pyrolysis is biochar, a stable carbon-rich material used for soil amendment, carbon sequestration, and other applications.
- Secondary products include bio-gas (a mixture of methane, hydrogen, and carbon monoxide) and bio-oil (a liquid by-product).
-
Environmental and Energy Considerations
- Slow pyrolysis releases far less CO₂ compared to combustion, making it a more environmentally friendly process.
- The energy efficiency of the process depends on proper control of temperature, residence time, and pressure.
By carefully controlling these conditions, slow pyrolysis can be optimized to produce high-quality biochar and other valuable by-products, making it a sustainable and efficient method for biomass conversion.
Summary Table:
Key Aspect | Details |
---|---|
Environment | Oxygen-limited or oxygen-free to prevent combustion. |
Temperature Range | ~400 °C, optimal for biochar yield and energy efficiency. |
Heating Rates | 1–30 °C/min for controlled thermal decomposition. |
Residence Time | Several hours for thorough biomass decomposition. |
Pressure | Atmospheric pressure for cost-effective operation. |
Feedstock Preparation | Drying and mechanical comminution for uniform heating. |
Energy Source | Combustion of produced gases or partial feedstock combustion. |
End Products | Biochar (primary), bio-gas, and bio-oil (secondary). |
Environmental Impact | Lower CO₂ emissions compared to combustion. |
Discover how slow pyrolysis can benefit your biomass conversion process—contact our experts today!