Sputtering, while a widely used technique for thin film deposition, has several notable disadvantages that can impact its efficiency, cost, and suitability for certain applications. These drawbacks include high capital expenses, low deposition rates for some materials, potential film contamination, and challenges in controlling film thickness and uniformity. Additionally, sputtering often requires complex equipment and cooling systems, which can increase operational costs and reduce production rates. The process is also less compatible with certain materials, particularly organic solids, which can degrade under ionic bombardment. Furthermore, sputtering can introduce impurities into the substrate, and its diffuse transport mechanism complicates integration with lift-off processes for film structuring.
Key Points Explained:
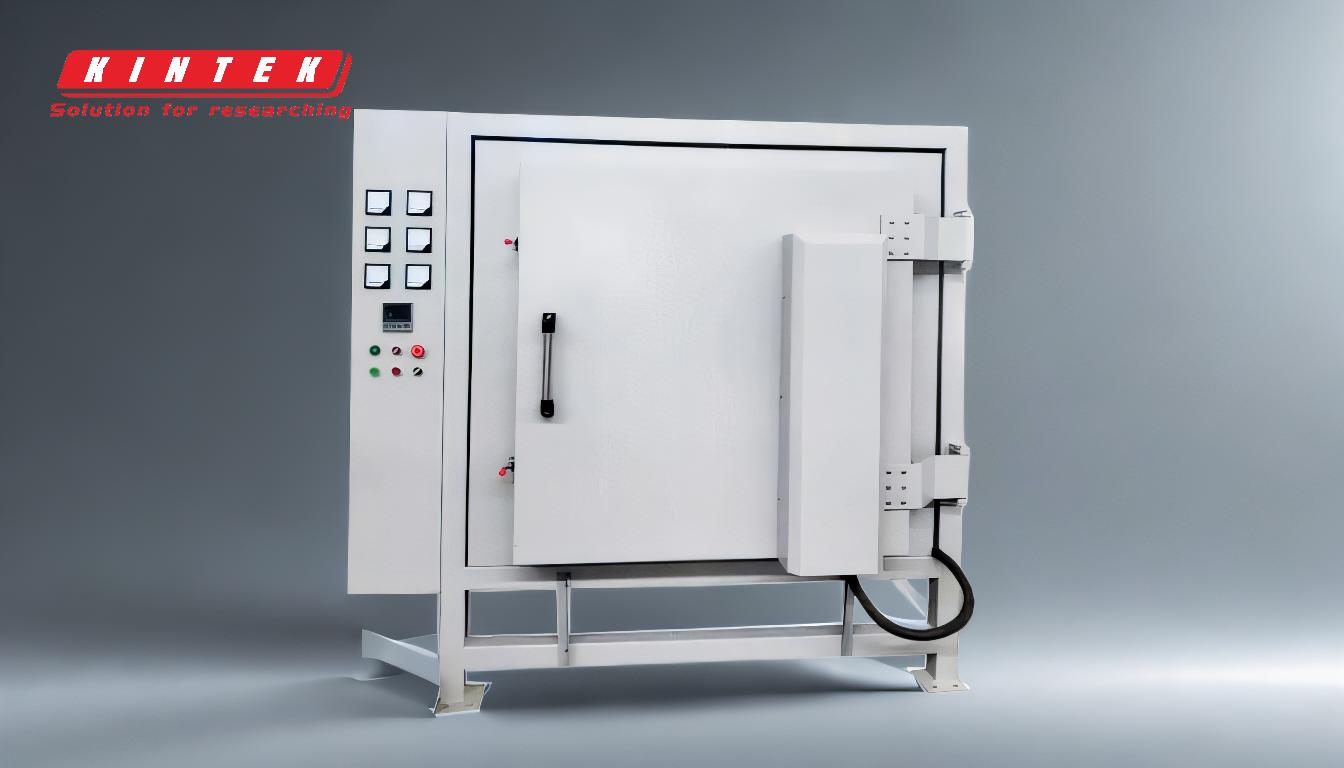
-
High Capital Expenses:
- Sputtering equipment is often expensive, requiring significant upfront investment. This includes the cost of high-pressure devices, cooling systems, and other specialized components.
- The need for a cooling system not only adds to the initial capital cost but also increases ongoing energy expenses, reducing the overall cost-effectiveness of the process.
-
Low Deposition Rates:
- Sputtering generally has lower deposition rates compared to other techniques like thermal evaporation. This is particularly true for certain materials, such as SiO2, which can slow down production rates.
- The low sputtering rates can be a significant limitation in high-throughput manufacturing environments where speed is critical.
-
Film Contamination:
- One of the major drawbacks of sputtering is the risk of film contamination. Impurities from the target material or the sputtering environment can be introduced into the film, degrading its quality.
- Gaseous contaminants in the plasma can become activated and incorporated into the growing film, further increasing the risk of contamination.
- In reactive sputter deposition, careful control of gas composition is necessary to prevent target poisoning, which can also lead to contamination.
-
Difficulty in Controlling Film Thickness and Uniformity:
- Achieving uniform film thickness can be challenging in sputtering due to the non-uniform distribution of the deposition flux. This often necessitates the use of moving fixtures to ensure even coating.
- The diffuse transport of sputtered atoms makes it difficult to achieve full shadowing, complicating the integration with lift-off processes for film structuring.
-
Material Limitations:
- Some materials, particularly organic solids, are susceptible to degradation under the ionic bombardment inherent in the sputtering process. This limits the range of materials that can be effectively deposited using this technique.
- The selection of coating materials is also constrained by their melting temperature, as materials with very high melting points may not be suitable for sputtering.
-
Impurity Introduction:
- Sputtering operates under a lesser vacuum range compared to evaporation, which increases the likelihood of introducing impurities into the substrate. This can affect the purity and performance of the deposited films.
-
Complex Equipment and Maintenance:
- The sputtering process requires complex equipment, including high-pressure devices and cooling systems, which can be difficult to maintain and operate.
- The need for user-supplied maintenance and the limitations of process parameters can further complicate the use of sputtering in industrial applications.
-
High Substrate Temperature Rise:
- The sputtering process can cause a significant rise in substrate temperature, which may be undesirable for temperature-sensitive materials or applications.
- This temperature rise can also make the substrate more susceptible to contamination from impurity gases.
In summary, while sputtering is a versatile and widely used deposition technique, it comes with several disadvantages that can limit its effectiveness in certain applications. These include high costs, low deposition rates, contamination risks, difficulties in controlling film properties, material limitations, and complex equipment requirements. Understanding these drawbacks is crucial for selecting the appropriate deposition method for specific applications and for optimizing the sputtering process to mitigate its limitations.
Summary Table:
Disadvantage | Description |
---|---|
High Capital Expenses | Expensive equipment and cooling systems increase upfront and ongoing costs. |
Low Deposition Rates | Slower rates for materials like SiO2 limit high-throughput production. |
Film Contamination | Impurities from targets or plasma can degrade film quality. |
Film Thickness Control | Non-uniform deposition flux complicates achieving even coatings. |
Material Limitations | Organic solids degrade under ionic bombardment; high-melting materials are less suitable. |
Impurity Introduction | Lesser vacuum range increases impurity risks in substrates. |
Complex Equipment | High-pressure devices and cooling systems require significant maintenance. |
Substrate Temperature Rise | Temperature-sensitive materials may degrade due to heat generated during sputtering. |
Need help selecting the right thin film deposition method? Contact our experts today for tailored solutions!