Pyrolysis, a process that decomposes organic materials at high temperatures in the absence of oxygen, poses several significant dangers. These include risks of explosions, fires, and the release of toxic gases, particularly during system startup, shutdown, or operational upsets. The high temperatures involved can exceed the autoignition temperature of produced gases, making inert gas purging essential to prevent explosions. Additionally, pyrolysis releases harmful emissions and byproducts, such as carbon monoxide and ash, which can negatively impact air quality and the environment. Proper design, operation, and maintenance are critical to mitigate these risks and ensure safety.
Key Points Explained:
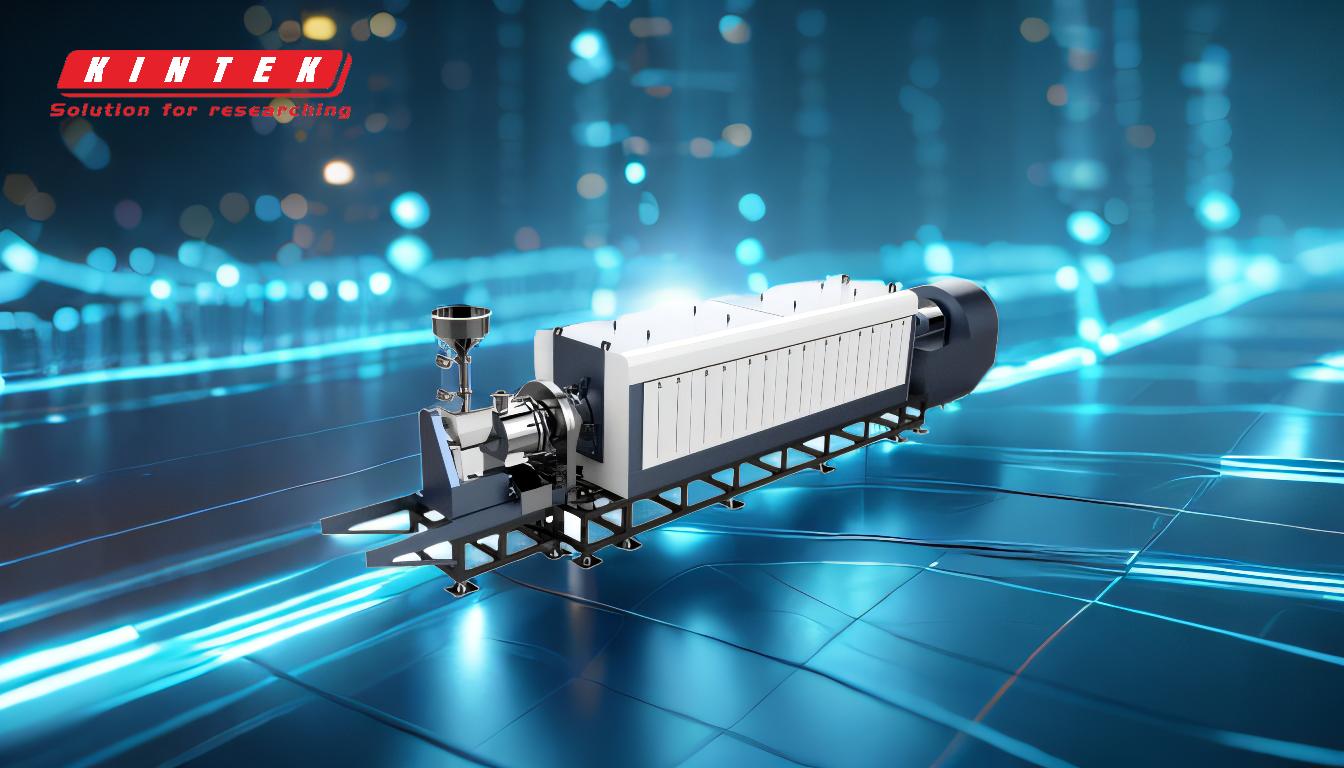
-
Explosion and Fire Risks
- Pyrolysis operates at temperatures that exceed the autoignition temperature of the gases produced.
- If oxygen is introduced into the system, these gases can ignite, leading to explosions or fires.
- The greatest risks occur during system startup, shutdown, intermittent operation, or operational upsets.
- Inert gas purging (e.g., using nitrogen) is essential to displace oxygen and prevent ignition.
- Historical accidents highlight the importance of maintaining oxygen-free conditions.
-
Release of Toxic Gases
- Pyrolysis produces toxic gases, with carbon monoxide being a primary concern.
- These gases pose significant health risks to workers and nearby populations if released.
- Proper ventilation and gas monitoring systems are necessary to detect and manage leaks.
-
High Temperatures and Pressures
- The process involves extreme temperatures and pressures, making equipment operation hazardous.
- Malfunctions or failures in temperature and pressure control systems can lead to catastrophic incidents.
- Regular monitoring, maintenance, and safety protocols are critical to prevent accidents.
-
Environmental Impact
- Pyrolysis releases gases, liquids, and ash that can harm the environment if not properly managed.
- Emissions can negatively affect air quality, contributing to pollution and health issues.
- Proper design and operation of pyrolysis systems are necessary to minimize emissions and ensure environmental compliance.
-
Operational Challenges
- The need for backup fuel, which may be produced during pyrolysis, adds complexity to the process.
- Ensuring consistent and safe operations requires advanced control systems and skilled personnel.
- Intermittent operation or system upsets increase the likelihood of accidents, emphasizing the need for robust safety measures.
In summary, pyrolysis presents significant risks, including explosions, toxic gas releases, and environmental harm. Addressing these dangers requires careful system design, rigorous operational protocols, and ongoing maintenance to ensure safety and minimize environmental impact.
Summary Table:
Risk Category | Key Dangers | Safety Measures |
---|---|---|
Explosion and Fire | High temperatures exceed autoignition of gases; oxygen introduction causes ignition. | Use inert gas purging (e.g., nitrogen) to displace oxygen; maintain oxygen-free conditions. |
Toxic Gas Release | Carbon monoxide and other harmful gases pose health risks. | Implement proper ventilation and gas monitoring systems to detect and manage leaks. |
High Temperatures | Extreme temperatures and pressures increase equipment hazards. | Regular monitoring, maintenance, and robust safety protocols to prevent accidents. |
Environmental Impact | Emissions and byproducts harm air quality and the environment. | Proper system design and operation to minimize emissions and ensure compliance. |
Operational Challenges | Backup fuel needs and intermittent operation increase accident risks. | Advanced control systems and skilled personnel for consistent and safe operations. |
Ensure your pyrolysis system is safe and efficient—contact our experts today for tailored solutions!