Chemical Vapor Deposition (CVD) is a widely used technique in Micro-Electro-Mechanical Systems (MEMS) for depositing thin films of materials. The process involves the reaction of gaseous precursors to form a solid material on a substrate. Different types of CVD processes are employed depending on the specific requirements of the MEMS application, such as the material to be deposited, the desired film properties, and the operating conditions. The main types of CVD include High Temperature CVD, Low Temperature CVD, Low Pressure CVD, Plasma Assisted CVD, Photo Assisted CVD, and others like Atmospheric Pressure CVD, Aerosol-Assisted CVD, and Metalorganic CVD. Each type has unique characteristics and applications, making them suitable for different MEMS fabrication needs.
Key Points Explained:
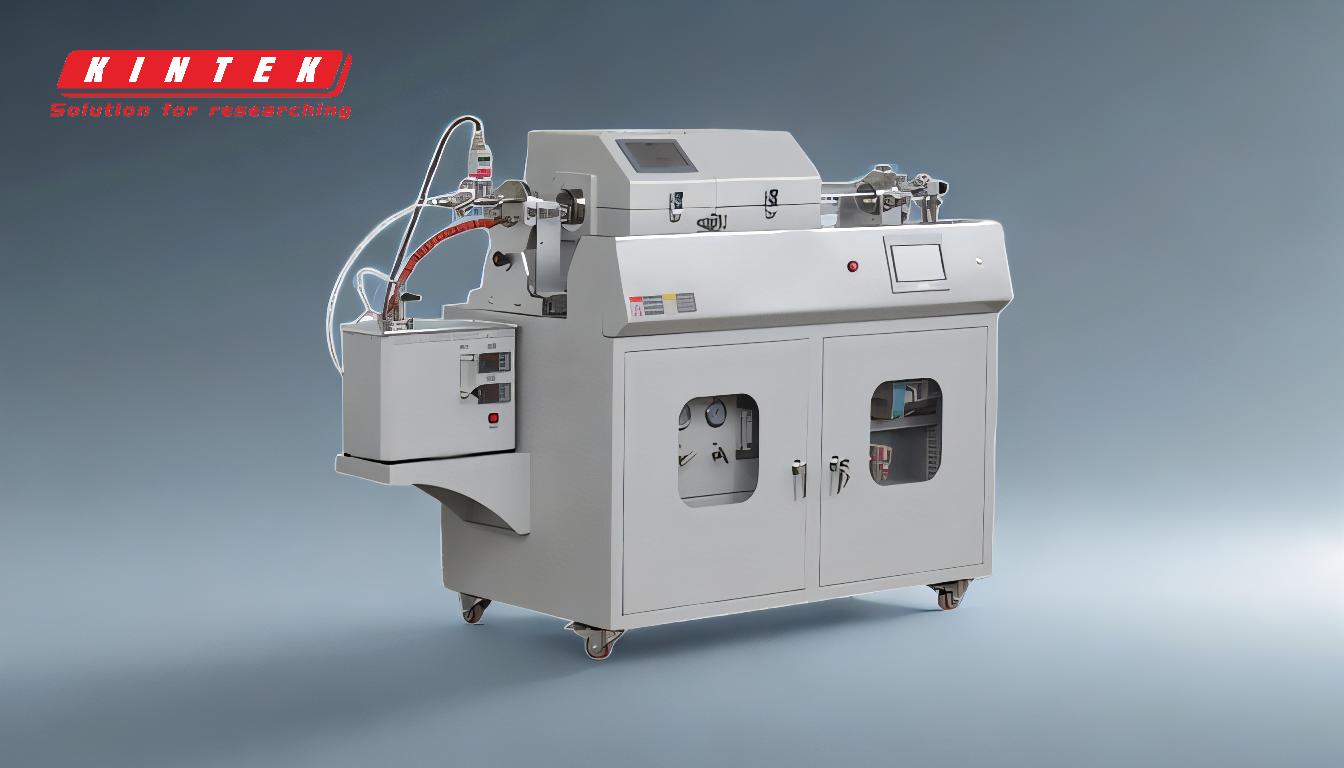
-
High Temperature CVD (HTCVD):
- Description: Operates at high temperatures, typically between 200°C to 1500°C.
- Applications: Used for depositing materials like silicon and titanium nitride.
- Advantages: High-quality films with excellent adhesion and uniformity.
- Disadvantages: High energy consumption and potential substrate damage due to high temperatures.
-
Low Temperature CVD (LTCVD):
- Description: Operates at lower temperatures compared to HTCVD.
- Applications: Ideal for depositing insulating layers such as silicon dioxide.
- Advantages: Reduces thermal stress on the substrate, suitable for temperature-sensitive materials.
- Disadvantages: May result in lower deposition rates and less dense films.
-
Low Pressure CVD (LPCVD):
- Description: Conducted at reduced pressures, typically below atmospheric pressure.
- Applications: Used for materials like silicon carbide that require lower pressure for optimal performance.
- Advantages: Improved film uniformity and step coverage.
- Disadvantages: Requires more complex equipment and vacuum systems.
-
Plasma Assisted CVD (PECVD):
- Description: Utilizes plasma to activate the chemical reactions.
- Applications: Commonly used for depositing silicon nitride and amorphous silicon.
- Advantages: Lower deposition temperatures and higher deposition rates.
- Disadvantages: Potential for plasma-induced damage to the substrate.
-
Photo Assisted CVD (PACVD):
- Description: Uses photons from a laser to activate the vapor phase chemistry.
- Applications: Suitable for depositing materials requiring precise control over the deposition process.
- Advantages: High precision and control over film properties.
- Disadvantages: Limited by the availability of suitable laser sources and potential for high costs.
-
Atmospheric Pressure CVD (APCVD):
- Description: Conducted at atmospheric pressure.
- Applications: Used for depositing oxides and nitrides.
- Advantages: Simpler equipment and lower operational costs.
- Disadvantages: Less control over film uniformity and quality compared to low-pressure methods.
-
Aerosol-Assisted CVD (AACVD):
- Description: Uses an aerosol to deliver the precursor to the substrate.
- Applications: Suitable for depositing complex materials and multi-component films.
- Advantages: Easier handling and transport of precursors.
- Disadvantages: Potential for non-uniform film deposition due to aerosol distribution.
-
Metalorganic CVD (MOCVD):
- Description: Uses metalorganic compounds as precursors.
- Applications: Commonly used for depositing compound semiconductors like GaAs and InP.
- Advantages: High purity and precise control over film composition.
- Disadvantages: High cost of precursors and potential for toxic by-products.
-
Atomic Layer CVD (ALCVD):
- Description: A variant of CVD that deposits materials one atomic layer at a time.
- Applications: Used for ultra-thin films and precise control over film thickness.
- Advantages: Excellent control over film thickness and uniformity.
- Disadvantages: Slow deposition rates and complex process control.
-
Ultra High Vacuum CVD (UHVCVD):
- Description: Conducted under ultra-high vacuum conditions.
- Applications: Used for depositing high-purity materials with minimal contamination.
- Advantages: Extremely high purity and control over film properties.
- Disadvantages: Requires sophisticated vacuum systems and high operational costs.
Each type of CVD process has its own set of advantages and disadvantages, making it crucial to select the appropriate method based on the specific requirements of the MEMS application. Understanding these different types of CVD processes allows for better decision-making in the fabrication of MEMS devices, ensuring optimal performance and reliability.
Summary Table:
CVD Type | Temperature/Pressure | Applications | Advantages | Disadvantages |
---|---|---|---|---|
HTCVD | 200°C–1500°C | Silicon, titanium nitride | High-quality films, excellent adhesion | High energy consumption, substrate damage |
LTCVD | Lower than HTCVD | Insulating layers (e.g., silicon dioxide) | Reduces thermal stress | Lower deposition rates, less dense films |
LPCVD | Below atmospheric | Silicon carbide | Improved film uniformity | Complex equipment, vacuum systems required |
PECVD | Low temperatures | Silicon nitride, amorphous silicon | Lower deposition temperatures, faster rates | Plasma-induced substrate damage |
PACVD | Laser-activated | Precise material deposition | High precision, control over film properties | High costs, limited laser availability |
APCVD | Atmospheric pressure | Oxides, nitrides | Simpler equipment, lower costs | Less control over film uniformity |
AACVD | Aerosol delivery | Complex materials, multi-component films | Easier precursor handling | Non-uniform film deposition |
MOCVD | Metalorganic precursors | Compound semiconductors (e.g., GaAs, InP) | High purity, precise composition control | High precursor costs, toxic by-products |
ALCVD | Atomic layer deposition | Ultra-thin films | Excellent thickness control | Slow deposition, complex process control |
UHVCVD | Ultra-high vacuum | High-purity materials | Extremely high purity | Sophisticated vacuum systems, high costs |
Need help selecting the right CVD process for your MEMS application? Contact our experts today for tailored solutions!