Physical Vapor Deposition (PVD) coatings are widely used across industries for their ability to enhance the durability, performance, and appearance of various materials. PVD coatings are thin, hard, and highly adherent, making them suitable for applications in medical devices, automotive components, and more. The most common PVD coating for medical devices is titanium nitride (TiN), known for its hardness and gold color. Other coatings like aluminum titanium nitride (AlTiN) and chrome nitride (CrN) offer specific properties tailored to different needs. PVD processes, such as sputtering and thermal evaporation, are used to deposit these coatings, ensuring precise control over thickness and properties.
Key Points Explained:
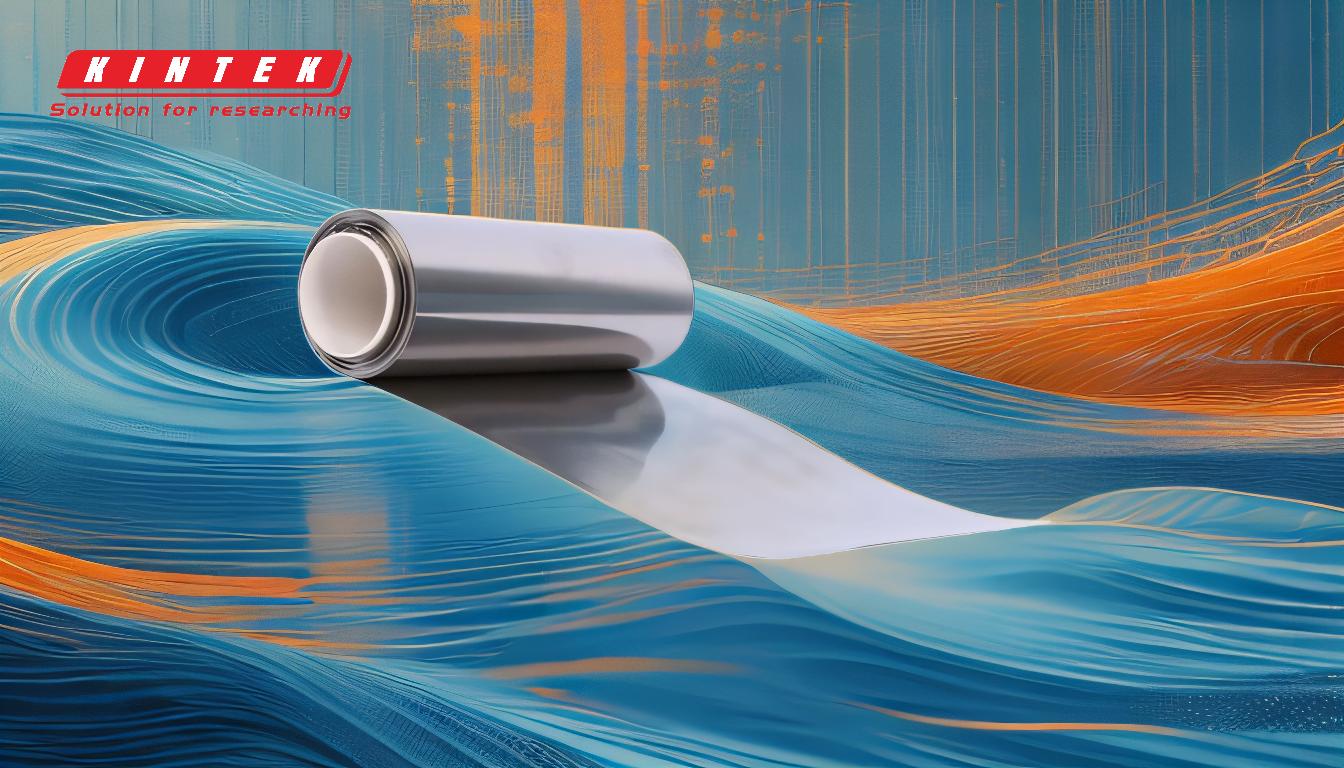
-
Common PVD Coatings and Their Properties:
- Titanium Nitride (TiN): This is the most widely used PVD coating, especially in medical devices. It has a thickness of 0.0001 to 0.0002 inch, a Vickers hardness of 2,400 to 2,600 Hv, and a distinctive gold color. TiN is valued for its wear resistance, corrosion resistance, and biocompatibility.
- Aluminum Titanium Nitride (AlTiN): This coating is known for its high hardness and thermal stability, making it suitable for high-temperature applications. It is often used in cutting tools and industrial components.
- Chrome Nitride (CrN): CrN offers excellent corrosion resistance and is commonly used in applications where both durability and aesthetic appeal are important, such as decorative trim and automotive parts.
- Alpha Coatings: These are specialized coatings with unique properties tailored to specific applications, often used in industries requiring high precision and performance.
-
PVD Coating Processes:
- Sputtering: This process involves bombarding the coating material (target) with a high-energy electrical charge to release atoms or molecules. These particles then deposit onto a substrate, forming a thin, uniform coating. Sputtering is widely used due to its ability to produce high-quality coatings with excellent adhesion.
- Thermal Evaporation: In this process, the coating material is heated to its boiling point in a high vacuum, creating a vapor that condenses on the substrate. Thermal evaporation is particularly effective for depositing materials with low melting points and is often used in optical and decorative applications.
-
Applications of PVD Coatings:
- Medical Devices: PVD coatings like TiN are used to enhance the durability and biocompatibility of surgical instruments, implants, and other medical devices. The thin, hard coatings reduce wear and corrosion, extending the life of these devices.
- Automotive Industry: PVD coatings are applied to engine components, decorative trim, and wheels to improve wear resistance, corrosion resistance, and aesthetic appeal. These coatings help automotive parts withstand harsh conditions while maintaining their appearance.
- Industrial Tools: Coatings like AlTiN and CrN are used on cutting tools, molds, and other industrial components to enhance their hardness, thermal stability, and resistance to wear and corrosion.
-
Advantages of PVD Coatings:
- Thin and Uniform: PVD coatings are extremely thin, ranging from atomic layers (less than 10 angstroms) to several microns. This allows for precise control over the coating thickness and properties.
- High Hardness and Durability: PVD coatings are known for their high hardness, making them resistant to wear, abrasion, and impact.
- Corrosion Resistance: These coatings provide excellent protection against corrosion, making them suitable for use in harsh environments.
- Aesthetic Appeal: PVD coatings can be tailored to achieve a variety of colors and finishes, enhancing the visual appeal of coated products.
In summary, PVD coatings offer a versatile and effective solution for improving the performance and appearance of various materials. With a range of coatings and processes available, PVD technology can be tailored to meet the specific needs of different industries, from medical devices to automotive components and industrial tools.
Summary Table:
Coating Type | Key Properties | Common Applications |
---|---|---|
Titanium Nitride (TiN) | Hardness (2,400-2,600 Hv), wear resistance, corrosion resistance, biocompatibility | Medical devices, surgical instruments |
Aluminum Titanium Nitride (AlTiN) | High hardness, thermal stability, wear resistance | Cutting tools, industrial components |
Chrome Nitride (CrN) | Excellent corrosion resistance, aesthetic appeal | Decorative trim, automotive parts |
Alpha Coatings | Specialized properties for high precision and performance | Precision industries, specialized applications |
Need the right PVD coating for your application? Contact our experts today for tailored solutions!