Pyrolysis furnaces are essential equipment used in various industries, including chemical production, waste material processing, biofuel production, and research. They facilitate the pyrolysis process, which involves the thermal decomposition of organic materials at high temperatures in the absence of oxygen. The primary types of pyrolysis furnaces include batch furnaces, continuous furnaces, and rotary kilns. Each type is designed for specific applications, ranging from small-scale laboratory use to large-scale industrial operations. Additionally, pyrolysis processes can vary, such as fast pyrolysis, slow pyrolysis, and gasification, each producing distinct byproducts like liquid hydrocarbons, char, biogas, and organic acids. Understanding the different types of pyrolysis furnaces and their applications is crucial for selecting the right equipment for specific industrial or research needs.
Key Points Explained:
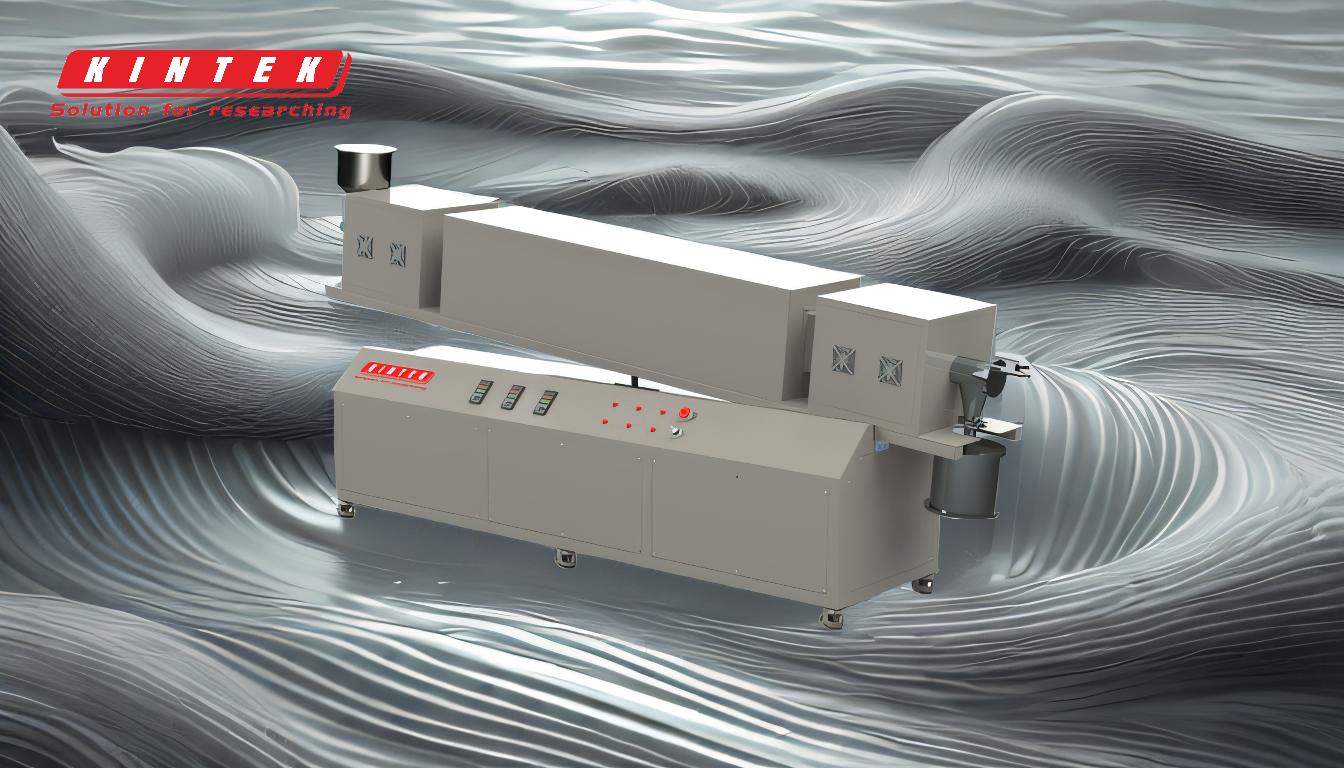
-
Batch Pyrolysis Furnaces
- Definition: Batch furnaces are designed for small-scale or laboratory use, where materials are processed in discrete batches.
- Applications: Ideal for research and development, testing new materials, or small-scale production.
-
Advantages:
- Precise control over temperature and processing conditions.
- Suitable for handling small quantities of materials.
- Cost-effective for experimental or low-volume operations.
-
Limitations:
- Not suitable for large-scale industrial applications due to lower throughput.
- Requires manual loading and unloading, which can be time-consuming.
-
Continuous Pyrolysis Furnaces
- Definition: Continuous furnaces are designed for industrial-scale operations, where materials are fed into the furnace continuously, and the pyrolysis process occurs without interruption.
- Applications: Used in large-scale chemical production, waste processing, and biofuel manufacturing.
-
Advantages:
- High throughput and efficiency for large-scale operations.
- Automated feeding and discharge systems reduce manual labor.
- Consistent product quality due to steady-state operation.
-
Limitations:
- Higher initial capital investment compared to batch furnaces.
- Requires precise control systems to maintain continuous operation.
-
Rotary Kiln Pyrolysis Furnaces
- Definition: Rotary kilns use rotational motion to mix and heat materials uniformly during the pyrolysis process.
- Applications: Commonly used in industries requiring uniform heat distribution, such as waste material processing and biochar production.
-
Advantages:
- Excellent heat transfer and mixing efficiency.
- Suitable for processing materials with varying particle sizes.
- Can handle both solid and semi-solid materials.
-
Limitations:
- Higher energy consumption due to rotational motion.
- Maintenance of rotating components can be complex and costly.
-
Types of Pyrolysis Processes
-
Fast Pyrolysis:
- Involves rapid heating of materials at high temperatures (400–700°C) with short residence times.
- Produces primarily liquid hydrocarbons (bio-oil) and some char and gas.
-
Slow Pyrolysis:
- Involves slower heating rates and longer residence times, typically producing more char and less liquid.
- Suitable for applications requiring solid byproducts like biochar.
-
Gasification:
- A high-temperature process that converts organic materials into syngas (a mixture of hydrogen, carbon monoxide, and carbon dioxide).
- Used in energy production and chemical synthesis.
-
Fast Pyrolysis:
-
Common Pyrolysis Reactors
-
Bubbling Fluidized Bed Pyrolyzers:
- Use a bed of inert particles fluidized by gas to ensure uniform heat transfer.
- Ideal for fast pyrolysis due to rapid heating and short residence times.
-
Circulating Fluid Beds and Transported Beds:
- Similar to bubbling fluidized beds but with continuous circulation of particles for enhanced heat transfer.
- Suitable for large-scale operations with high throughput.
-
Ablative Pyrolyzers:
- Use mechanical pressure to press materials against a heated surface, enabling rapid heat transfer.
- Effective for processing materials with low thermal conductivity.
-
Bubbling Fluidized Bed Pyrolyzers:
-
Selection Criteria for Pyrolysis Furnaces
- Scale of Operation: Batch furnaces for small-scale or experimental use, continuous furnaces for industrial-scale production.
- Material Characteristics: Rotary kilns for materials requiring uniform mixing, fluidized beds for rapid heating.
- Desired Products: Fast pyrolysis for bio-oil, slow pyrolysis for biochar, gasification for syngas.
- Energy Efficiency: Consider energy consumption and heat transfer efficiency when selecting a furnace type.
By understanding the different types of pyrolysis furnaces and their respective advantages, limitations, and applications, purchasers can make informed decisions tailored to their specific industrial or research needs.
Summary Table:
Type of Furnace | Applications | Advantages | Limitations |
---|---|---|---|
Batch Pyrolysis | Small-scale, R&D, testing | Precise control, cost-effective, suitable for small quantities | Lower throughput, manual loading/unloading |
Continuous Pyrolysis | Industrial-scale, waste processing | High throughput, automated systems, consistent product quality | High capital investment, requires precise control |
Rotary Kiln | Waste processing, biochar production | Excellent heat transfer, handles varying particle sizes, solid/semi-solid materials | Higher energy consumption, complex maintenance |
Need help selecting the right pyrolysis furnace? Contact our experts today for personalized guidance!