Pyrolysis oil is a complex liquid product derived from the thermal decomposition of biomass in the absence of oxygen. It is characterized by its dark brown color, high oxygen content, and a mixture of oxygenated hydrocarbons, water, and various organic compounds. Pyrolysis oil is highly corrosive, thermally unstable, and non-volatile, making it distinct from traditional fossil fuels. The types of pyrolysis oil are primarily influenced by the pyrolysis process used, which includes slow pyrolysis, fast pyrolysis, and flash pyrolysis. Each process varies in heating rates, residence times, and product yields, resulting in different properties and compositions of the pyrolysis oil. Understanding these differences is crucial for selecting the appropriate pyrolysis method and oil type for specific applications.
Key Points Explained:
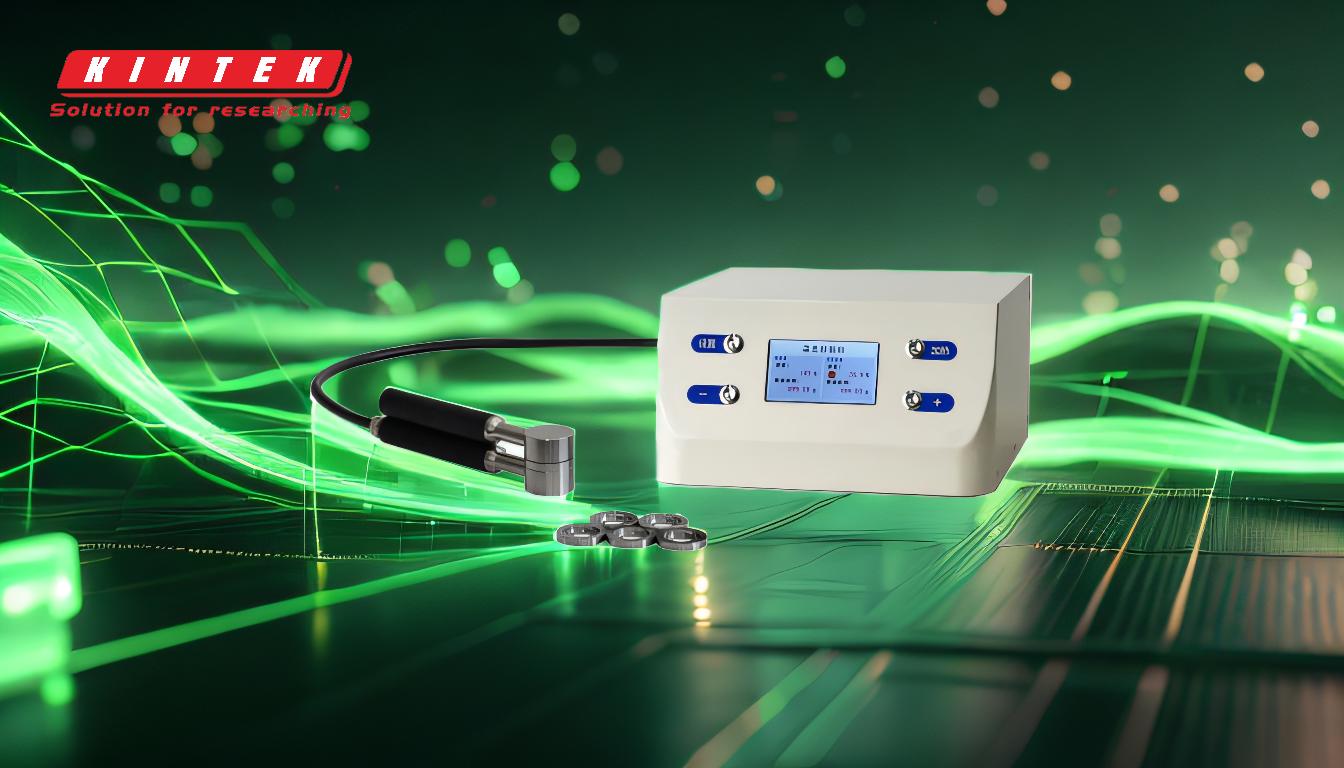
-
Types of Pyrolysis Processes:
-
Slow Pyrolysis:
- Heating Rate: Slow heating rates, typically less than 10°C per minute.
- Residence Time: Long residence times, often several hours.
- Main Product: Biochar is the primary product, with lesser amounts of pyrolysis oil and syngas.
- Oil Characteristics: The oil produced is less abundant and may have a higher viscosity due to the longer exposure to heat, leading to more condensation reactions.
-
Fast Pyrolysis:
- Heating Rate: Rapid heating rates, often exceeding 100°C per second.
- Residence Time: Short residence times, typically a few seconds.
- Main Product: Bio-oil is the primary product, with yields of up to 60%. Biochar and syngas are also produced but in smaller quantities.
- Oil Characteristics: The oil is more abundant and has a lower viscosity compared to slow pyrolysis oil. It is more suitable for applications requiring liquid fuels.
-
Flash Pyrolysis:
- Heating Rate: Extremely rapid heating rates, often exceeding 1000°C per second.
- Residence Time: Very short residence times, often less than a second.
- Main Product: High yields of bio-oil, with minimal biochar and syngas production.
- Oil Characteristics: The oil is highly volatile and has a lower molecular weight compared to oils from other pyrolysis methods. It is more suitable for high-temperature applications.
-
Slow Pyrolysis:
-
Composition of Pyrolysis Oil:
- Oxygenated Hydrocarbons: Pyrolysis oil is primarily composed of oxygenated hydrocarbons, which include a wide range of compounds such as acids, alcohols, ketones, and aldehydes.
- Water Content: The oil contains a significant amount of water (20-30 wt-%), which contributes to its instability and corrosiveness.
- Organic Compounds: The oil includes both low molecular weight compounds (e.g., formaldehyde, acetic acid) and high molecular weight compounds (e.g., phenols, anhydrosugars, oligosaccharides).
- Polymerization: The high oxygen content makes the oil prone to polymerization, especially when exposed to air, leading to increased viscosity over time.
-
Properties of Pyrolysis Oil:
- Corrosiveness: The high acidity and presence of water make pyrolysis oil corrosive to metals, requiring specialized storage and handling equipment.
- Thermal Instability: The oil is thermally unstable and can degrade or polymerize when heated, making it unsuitable for direct use in some applications.
- Non-Volatility: Due to its high oxygen content, pyrolysis oil is non-volatile and cannot be completely re-vaporized once recovered.
- Immiscibility: Pyrolysis oil is immiscible with fossil fuels, limiting its use in blending with conventional fuels.
-
Applications of Pyrolysis Oil:
- Fuel: Despite its challenges, pyrolysis oil can be used as a fuel in boilers, engines, and turbines, often requiring modifications to handle its unique properties.
- Chemical Feedstock: The oil can be upgraded to produce chemicals and other valuable products, though this often requires further processing to reduce oxygen content and stabilize the oil.
- Energy Production: Pyrolysis oil can be co-fired with other fuels in power plants to generate electricity and heat.
-
Challenges and Considerations:
- Storage and Handling: Due to its corrosive and unstable nature, pyrolysis oil requires careful storage and handling to prevent degradation and equipment damage.
- Upgrading: To improve its quality and stability, pyrolysis oil often needs to be upgraded through processes such as hydrodeoxygenation, which reduces oxygen content and enhances fuel properties.
- Economic Viability: The cost of producing and upgrading pyrolysis oil must be balanced against its potential benefits, particularly in comparison to conventional fuels.
In summary, the different types of pyrolysis oil are primarily determined by the pyrolysis process used, with slow, fast, and flash pyrolysis each producing oils with distinct properties and compositions. Understanding these differences is essential for selecting the appropriate pyrolysis method and oil type for specific applications, while also addressing the challenges associated with its use.
Summary Table:
Pyrolysis Process | Heating Rate | Residence Time | Main Product | Oil Characteristics |
---|---|---|---|---|
Slow Pyrolysis | <10°C/min | Several hours | Biochar | Less abundant, higher viscosity |
Fast Pyrolysis | >100°C/sec | Few seconds | Bio-oil (up to 60%) | Abundant, lower viscosity |
Flash Pyrolysis | >1000°C/sec | <1 second | Bio-oil | Highly volatile, low molecular weight |
Need help selecting the right pyrolysis oil for your application? Contact our experts today!