Rotary furnaces, while beneficial for processing dross and low-grade scrap, come with several disadvantages that can impact their efficiency, maintenance, and environmental footprint. These include low energy efficiency, higher maintenance requirements, and the production of hazardous waste in the form of salt cake. Additionally, the continuous movement of materials in a rotary furnace, while improving gas diffusion and heat treatment efficiency, can also lead to challenges such as sample loss and the need for careful temperature monitoring. Understanding these drawbacks is crucial for making informed decisions about their use in various industrial applications.
Key Points Explained:
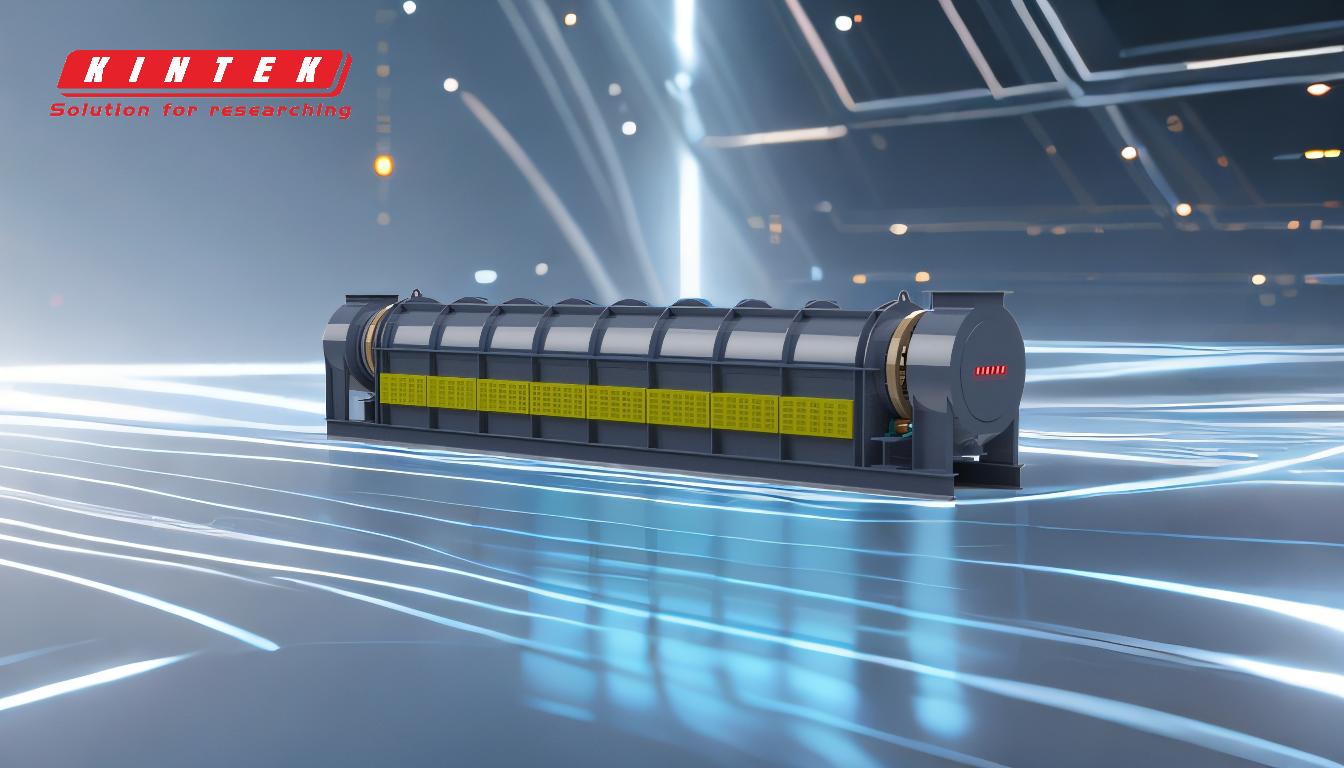
-
Low Energy Efficiency:
- Rotary furnaces are often less energy-efficient compared to other types of furnaces. The continuous rotation and movement of materials require significant energy input, which can lead to higher operational costs. This is particularly true when compared to static furnaces, where the energy required for rotation is not a factor.
- The energy inefficiency is further compounded by the need to maintain consistent temperature profiles, which can be challenging in a rotary setup.
-
Higher Maintenance Requirements:
- The mechanical components of a rotary furnace, such as the rotating drum and seals, are subject to wear and tear due to continuous operation. This necessitates frequent maintenance to ensure the furnace operates efficiently and safely.
- Maintenance can be complex and may require specialized knowledge or professional assistance, adding to the overall cost of operation.
-
Production of Hazardous Waste:
- One of the significant environmental drawbacks of rotary furnaces is the production of salt cake, a byproduct that must be disposed of as hazardous waste. This not only increases the environmental impact but also adds to the operational costs due to the need for proper waste management and disposal.
- The handling and disposal of hazardous waste require compliance with strict regulations, which can further complicate the operation of rotary furnaces.
-
Sample Loss and Boiling Issues:
- In some applications, such as distillation, rotary furnaces can lead to sample loss, particularly with volatile substances like ethanol and water. This is due to the boiling of samples, which can be difficult to control even with adjustments to the vacuum pump or heating pot temperature.
- Mitigating sample loss may require additional equipment or modifications, such as the use of anti-boiling particles or specialized condensers, which can increase the complexity and cost of the process.
-
Temperature Monitoring and Control:
- Maintaining a consistent temperature profile in a rotary furnace is crucial for product uniformity and quality. However, the continuous movement of materials can make temperature monitoring and control more challenging compared to static furnaces.
- Inconsistent temperature distribution can lead to uneven heat treatment, affecting the final product's properties and potentially leading to waste or rework.
-
Material Handling and Size Limitations:
- While rotary furnaces are efficient for continuous processing, they may have limitations in terms of the size and type of materials that can be effectively processed. Large or irregularly shaped materials may not be suitable for rotary furnaces, limiting their versatility.
- The design of the furnace and the type of material being processed can also impact the overall efficiency, requiring careful consideration during the selection and setup of the furnace.
In summary, while rotary furnaces offer several advantages, such as improved gas diffusion and continuous processing capabilities, they also come with significant disadvantages. These include low energy efficiency, higher maintenance requirements, the production of hazardous waste, sample loss, and challenges in temperature control and material handling. Understanding these drawbacks is essential for making informed decisions about the use of rotary furnaces in various industrial applications. For more information on rotating furnaces, you can visit rotating furnace.
Summary Table:
Disadvantage | Key Details |
---|---|
Low Energy Efficiency | High energy input due to continuous rotation; challenges in maintaining temperature. |
Higher Maintenance | Frequent wear and tear of mechanical parts; requires specialized maintenance. |
Hazardous Waste Production | Produces salt cake, a hazardous byproduct requiring strict disposal compliance. |
Sample Loss | Boiling issues in distillation; volatile substances like ethanol may be lost. |
Temperature Control | Inconsistent temperature profiles due to material movement; affects product quality. |
Material Handling | Limited suitability for large or irregularly shaped materials. |
Need help choosing the right furnace for your industrial needs? Contact our experts today!