Compression molding, while a widely used manufacturing process, comes with several disadvantages that can affect production efficiency, cost, and product quality. The process involves placing a pre-measured amount of material into a mold cavity, which is then compressed under heat and pressure to form the desired shape. However, challenges such as material waste, labor intensity, and potential defects often arise, making it less ideal for certain applications. Below, we explore the key disadvantages of compression molding in detail.
Key Points Explained:
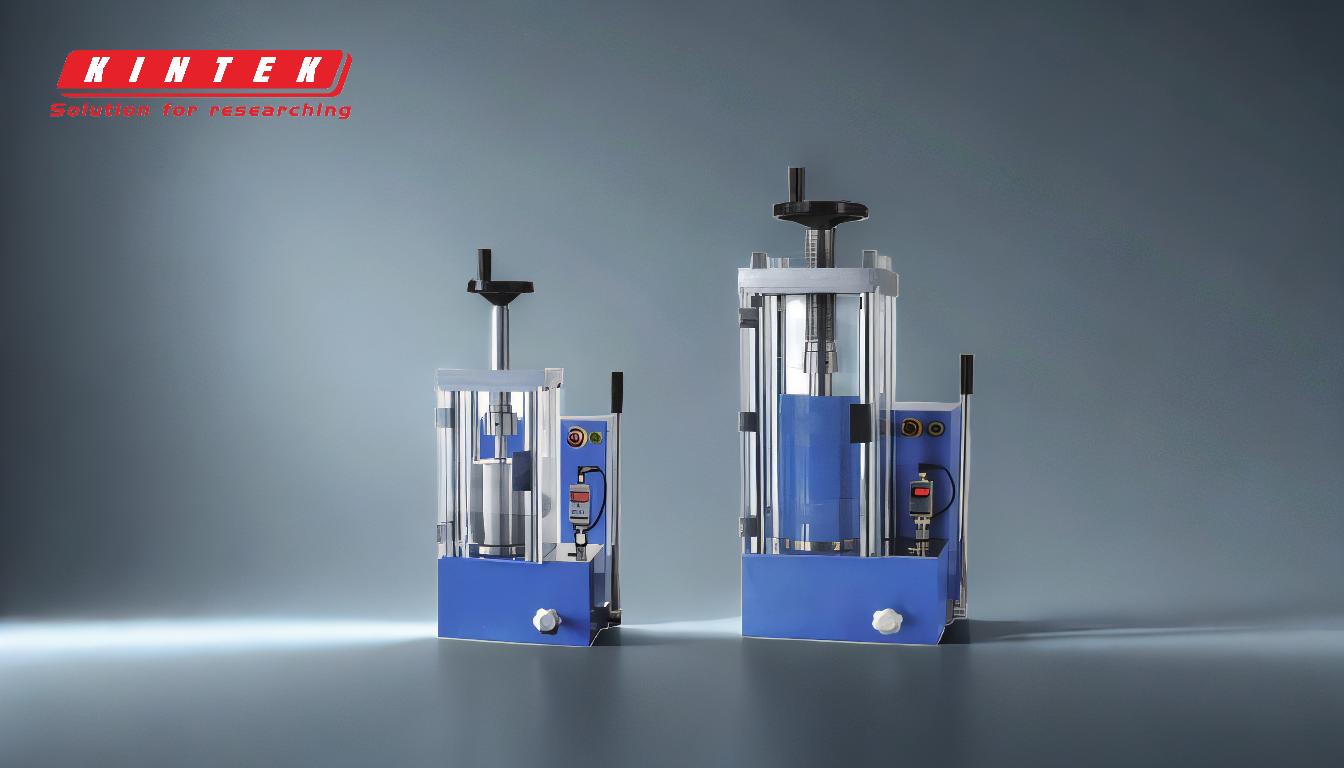
-
Material Waste and Inefficiency:
- One of the primary disadvantages of compression molding is the difficulty in accurately cutting or weighing the material (stock) for each mold cavity. If too little material is used, it can result in defects such as flow lines, blisters, or incomplete filling of the mold. On the other hand, excessive material leads to heavy flash, which is the excess material that escapes from the mold cavity and forms thin layers around the edges of the product. Removing this flash requires additional labor and can lead to material waste, increasing overall production costs.
-
Labor-Intensive Process:
- Compression molding is more labor-intensive compared to other molding techniques like injection molding. The process requires manual loading and unloading of the mold, which can slow down production cycles and increase labor costs. This makes it less suitable for high-volume manufacturing, where automation and faster cycle times are critical.
-
Potential for Defects:
- The process is prone to defects if the material is not placed correctly or if the mold design is not optimal. Common defects include:
- Flow Lines: These occur when the material does not flow evenly into the mold, leading to visible lines or streaks on the finished product.
- Blisters: These are caused by trapped air or gas during the molding process, resulting in raised areas on the surface of the product.
- Unfilled Parts: Insufficient material or improper placement can leave parts of the mold unfilled, leading to incomplete or defective products.
- The process is prone to defects if the material is not placed correctly or if the mold design is not optimal. Common defects include:
-
Limited Design Flexibility:
- Compression molding is less versatile in terms of design complexity compared to other methods like injection molding. It is better suited for simpler, less intricate shapes. Complex geometries or fine details are harder to achieve, limiting its application in industries that require highly detailed or intricate components.
-
Longer Cycle Times:
- The cycle times in compression molding are generally longer than in other molding processes. The need for manual loading and unloading, combined with the time required for the material to cure or set, can slow down production. This makes it less efficient for large-scale manufacturing where speed is a priority.
-
High Initial Tooling Costs:
- While compression molding can be cost-effective for small production runs, the initial tooling costs can be high. The molds must be precisely designed and manufactured to withstand the heat and pressure of the process, which can be expensive. This makes it less attractive for low-budget projects or prototypes.
-
Difficulty in Controlling Flash:
- Flash is a common issue in compression molding, especially when excessive material is used. Removing flash requires additional post-processing steps, which can increase labor costs and production time. In some cases, excessive flash can also affect the dimensional accuracy and surface finish of the final product.
-
Limited Material Options:
- Compression molding is typically used with thermosetting materials, which cure irreversibly under heat and pressure. This limits the range of materials that can be used compared to other processes like injection molding, which can work with both thermoplastics and thermosetting materials. This limitation can restrict the application of compression molding in industries that require specific material properties.
In summary, while compression molding is a useful manufacturing process for certain applications, it comes with several disadvantages, including material waste, labor intensity, potential defects, limited design flexibility, longer cycle times, high initial tooling costs, difficulty in controlling flash, and limited material options. These factors should be carefully considered when choosing a manufacturing method for a specific product or application.
Summary Table:
Disadvantage | Description |
---|---|
Material Waste and Inefficiency | Difficulty in accurate material measurement leads to defects or excessive flash. |
Labor-Intensive Process | Manual loading/unloading increases labor costs and slows production. |
Potential for Defects | Flow lines, blisters, and unfilled parts can occur due to improper material use. |
Limited Design Flexibility | Less suitable for complex or intricate designs compared to other methods. |
Longer Cycle Times | Manual processes and curing time slow down production. |
High Initial Tooling Costs | Expensive molds required, making it less ideal for low-budget projects. |
Difficulty in Controlling Flash | Excess material (flash) requires additional post-processing. |
Limited Material Options | Primarily works with thermosetting materials, restricting material choices. |
Need help choosing the right manufacturing process? Contact our experts today for tailored solutions!