DC magnetron sputtering, while widely used for thin film deposition, has several notable disadvantages. These include limitations in material compatibility, such as the inability to sputter low-conductivity and insulating materials due to charge accumulation. Additionally, the process can lead to higher substrate heating and structural defects due to intense ion bombardment. The optimization of film properties is often complex and time-consuming due to the numerous control parameters involved. Furthermore, the process has limitations in terms of plasma stability, target utilization, and cost-effectiveness. These drawbacks make it less suitable for certain applications, particularly those requiring precise control over material properties or involving non-conductive materials.
Key Points Explained:
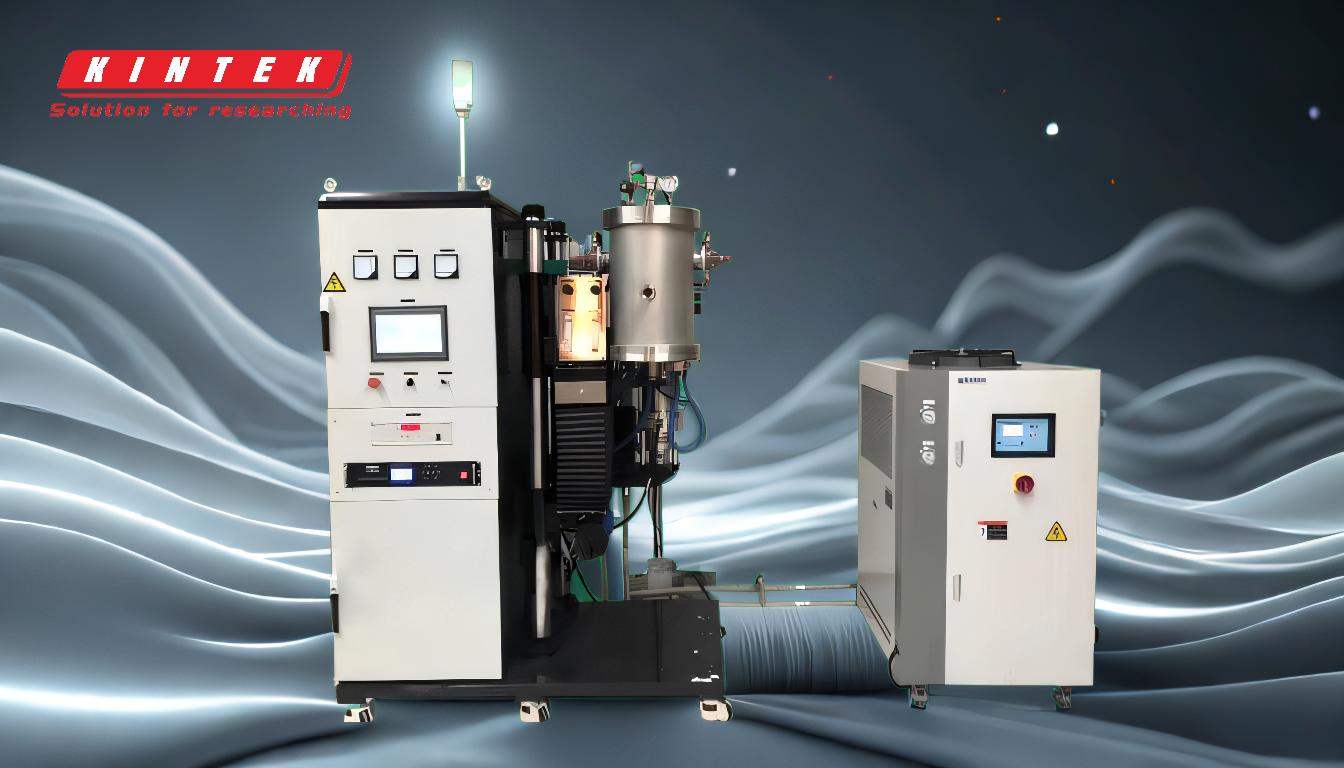
-
Inability to Sputter Low-Conductivity and Insulating Materials:
- DC magnetron sputtering relies on the passage of current through the target material. This makes it unsuitable for low-conductivity or insulating materials, as charge accumulation on the target surface disrupts the sputtering process. This limitation is addressed by RF magnetron sputtering, which uses alternating current to handle such materials effectively.
-
Higher Substrate Heating and Structural Defects:
- The process can cause significant substrate heating, with temperatures rising up to 250°C. This is due to the high-energy ion bombardment on the substrate, which can also lead to structural defects in the deposited films. Such defects may compromise the quality and performance of the thin films.
-
Complex Optimization of Film Properties:
- DC magnetron sputtering involves numerous control parameters, such as power, pressure, and gas composition, which must be carefully optimized to achieve desired film properties. This optimization process can be time-consuming and requires significant expertise, making the process less efficient for certain applications.
-
Limited Plasma Stability and Target Utilization:
- The plasma used in DC magnetron sputtering can be unstable, affecting the consistency of the deposition process. Additionally, the target material is often underutilized, leading to higher costs and material waste.
-
High Process Costs:
- The equipment and operational costs associated with DC magnetron sputtering are relatively high. This includes the cost of maintaining vacuum conditions, specialized targets, and the energy required for the process. These factors can make the process less economical for large-scale or low-budget applications.
-
Geometric Limitations and Poor Film Bonding:
- The effective coating area in DC magnetron sputtering is limited, restricting the size and shape of workpieces that can be coated. Moreover, the energy of the sputtered particles is often low, resulting in poor bonding strength between the film and substrate. This can lead to the formation of porous and rough columnar structures, which may not meet the requirements for certain high-performance applications.
By understanding these disadvantages, users can make informed decisions about whether DC magnetron sputtering is suitable for their specific needs or if alternative deposition methods, such as RF magnetron sputtering, should be considered.
Summary Table:
Disadvantage | Description |
---|---|
Inability to Sputter Low-Conductivity Materials | Charge accumulation disrupts sputtering of insulating or low-conductivity materials. |
Higher Substrate Heating | Temperatures up to 250°C can cause structural defects in films. |
Complex Optimization | Numerous control parameters make achieving desired film properties time-consuming. |
Limited Plasma Stability | Unstable plasma affects deposition consistency and target utilization. |
High Process Costs | Equipment, energy, and material costs make it less economical for some applications. |
Geometric Limitations | Limited coating area and poor film bonding reduce suitability for certain applications. |
Need help choosing the right sputtering method? Contact our experts today for tailored solutions!