Electron beam evaporation is a widely used technique in thin film deposition, known for its ability to handle high-melting-point materials and achieve high deposition rates. However, it comes with several disadvantages that can limit its applicability in certain scenarios. These include high equipment costs, safety hazards due to high voltage, challenges in achieving uniform deposition, and the production of porous layers. Additionally, the process requires complex electronics and faces difficulties in scaling linearly, making it less suitable for some lab applications. Despite its advantages, these drawbacks must be carefully considered when choosing this method for specific applications.
Key Points Explained:
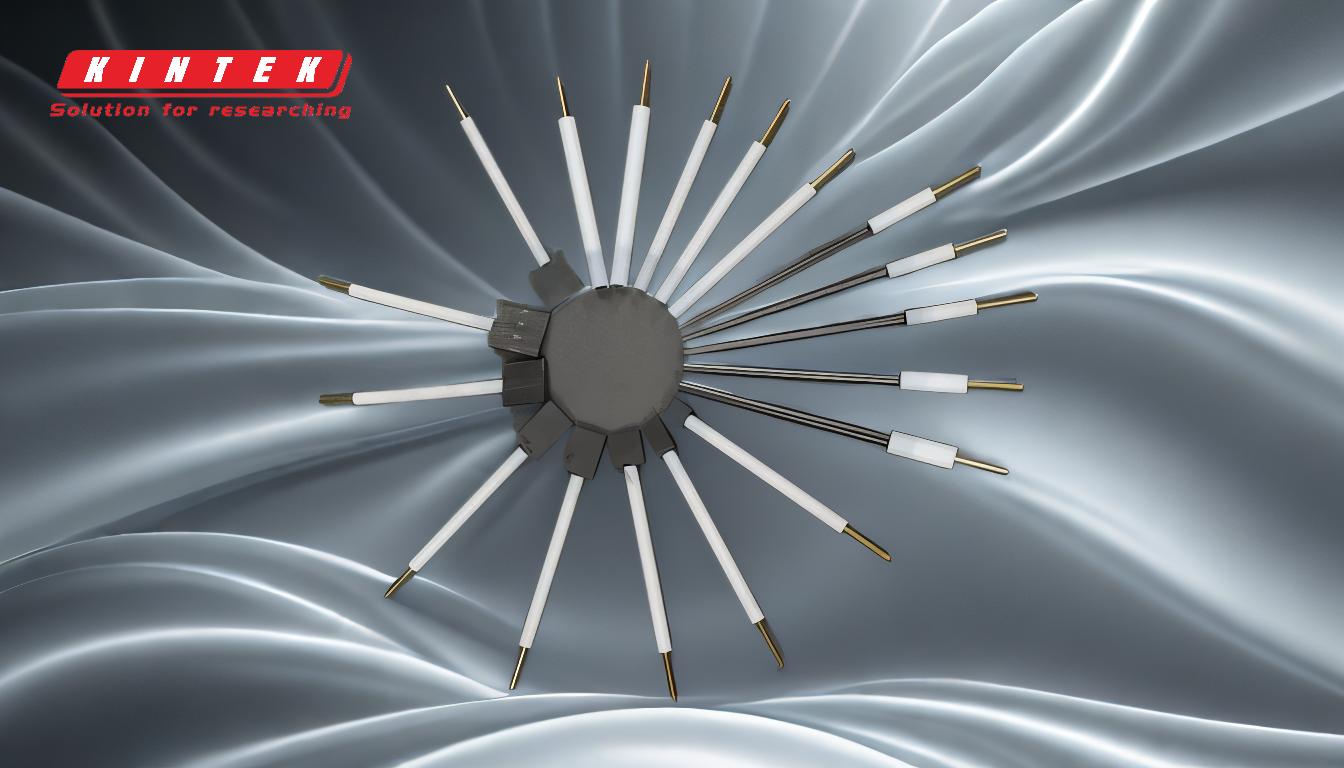
-
High Equipment Costs:
- Electron beam evaporation systems are significantly more expensive than traditional thermal evaporation methods such as filament or boat evaporation. This is due to the complexity of the equipment, which includes high-power electron beam guns and advanced drive electronics. The high initial investment can be a barrier for smaller labs or applications with limited budgets.
-
High Voltage Safety Hazards:
- The process involves the use of high voltages to generate the electron beam, posing significant safety risks. Proper safety protocols and equipment are essential to mitigate these risks, but they add to the overall complexity and cost of the system.
-
Deposition Uniformity Challenges:
- Electron beam evaporation is an isotropic process, meaning atoms are evaporated in all directions equally. This can lead to non-uniform deposition, with wafers directly above the crucible being coated more heavily than those off to the side. While manufacturers use spherical wafer holders to address this issue, achieving perfect uniformity remains a challenge.
-
Production of Porous Layers:
- One of the notable disadvantages of electron beam evaporation is the tendency to produce porous deposited layers. This porosity can be a significant limitation, especially in applications requiring dense, non-porous coatings, such as in climatic environments where moisture ingress could be problematic.
-
Complex Drive Electronics:
- The process requires sophisticated drive electronics to control the electron beam and deposition rates accurately. This complexity not only increases the cost but also makes the system more challenging to operate and maintain.
-
Difficulty in Scaling Linearly:
- Electron beam evaporation does not scale linearly, making it less suitable for some lab applications where scalability is a concern. This limitation can restrict its use in processes requiring consistent results across different scales.
-
Challenges with Chemical Compounds:
- When evaporating chemical compounds, there is a risk of unwanted side reactions, decomposition products, or unstable melts. Specialized techniques are required to control these issues, adding another layer of complexity to the process.
-
Limited Suitability for Certain Applications:
- Despite its advantages, the disadvantages of electron beam evaporation make it less suitable for some applications, particularly those requiring dense, non-porous coatings or those with stringent budget constraints.
In summary, while electron beam evaporation offers significant advantages in terms of high-temperature capabilities and deposition rates, its disadvantages—such as high costs, safety hazards, deposition uniformity issues, and the production of porous layers—must be carefully weighed when selecting this method for specific applications.
Summary Table:
Disadvantage | Description |
---|---|
High Equipment Costs | Complex systems with high-power electron beam guns and advanced electronics. |
High Voltage Safety Hazards | Requires strict safety protocols due to high-voltage risks. |
Deposition Uniformity Challenges | Isotropic process leads to non-uniform coating. |
Production of Porous Layers | Deposited layers tend to be porous, limiting use in dense coating applications. |
Complex Drive Electronics | Sophisticated electronics increase cost and operational complexity. |
Difficulty in Scaling Linearly | Limited scalability for consistent results across different scales. |
Challenges with Chemical Compounds | Risk of side reactions, decomposition, or unstable melts. |
Limited Suitability for Some Apps | Less ideal for dense coatings or budget-constrained applications. |
Need help deciding if electron beam evaporation is right for your application? Contact our experts today!