Induction soldering, while advantageous in many industrial applications, has several notable disadvantages. These include high initial costs, complexity in operation, material limitations, and challenges related to refining and maintaining material composition. Below, we explore these disadvantages in detail, providing a comprehensive understanding of the limitations associated with induction soldering.
Key Points Explained:
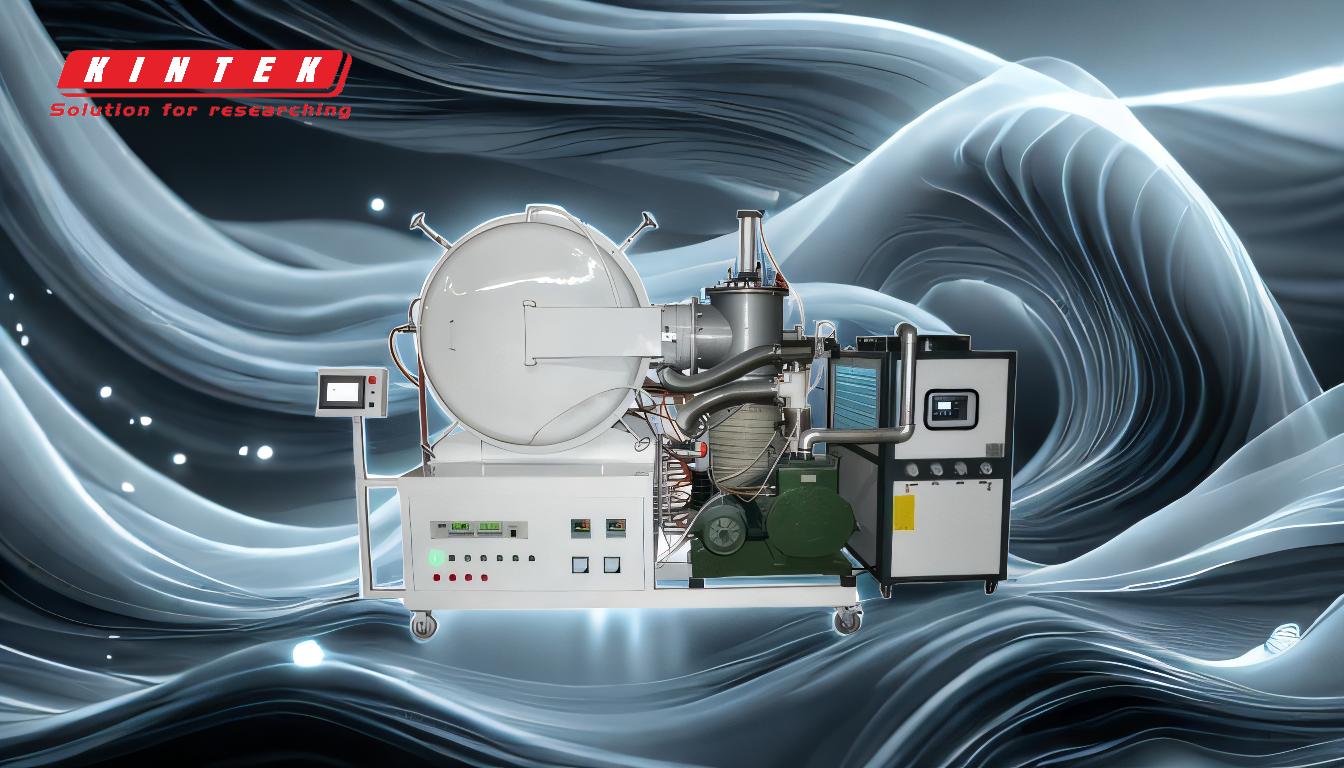
-
High Initial Cost
- Induction soldering equipment is significantly more expensive compared to traditional soldering methods.
- The cost includes not only the machine itself but also the associated infrastructure, such as power supplies and cooling systems.
- For small-scale operations or businesses with limited budgets, this high upfront investment can be a major barrier to adoption.
-
Complex Process and Operation
- Induction soldering requires specialized knowledge and training to operate effectively.
- The process involves precise control of parameters such as frequency, power, and heating time, which can be challenging for inexperienced operators.
- Maintenance of the equipment also demands technical expertise, adding to operational complexity.
-
Material Limitations
- Induction soldering is not suitable for all materials. It works best with conductive metals like copper, brass, and steel.
- Non-conductive materials or those with poor thermal conductivity may not heat evenly or efficiently, leading to inconsistent results.
- Certain materials may also degrade or oxidize under the high temperatures generated by induction heating.
-
Lack of Refining Capacity
- Induction soldering does not have the ability to refine or purify materials during the process.
- The materials used must be free of oxides and contaminants beforehand, as these can negatively impact the quality of the solder joint.
- This limitation requires additional pre-processing steps, increasing time and cost.
-
Oxidation and Alloying Element Loss
- High temperatures during induction soldering can cause oxidation of certain materials, particularly those with reactive alloying elements.
- Oxidation can lead to the loss of critical alloying elements, which may need to be re-added to maintain the desired material properties.
- This issue can compromise the integrity and performance of the final product.
-
Energy Consumption and Efficiency
- Induction soldering systems can be energy-intensive, especially when operating at high frequencies or power levels.
- While induction heating is generally efficient, the overall energy consumption may still be higher compared to other soldering methods, depending on the application.
-
Limited Flexibility for Small or Complex Parts
- Induction soldering is less effective for small, intricate, or irregularly shaped parts due to difficulties in achieving uniform heating.
- Custom coil designs may be required for specific applications, adding to the complexity and cost.
-
Safety Concerns
- The high temperatures and electromagnetic fields generated during induction soldering pose safety risks to operators.
- Proper safety measures, such as shielding and protective equipment, are necessary to mitigate these risks.
In summary, while induction soldering offers advantages such as speed, precision, and localized heating, its disadvantages—including high costs, material limitations, and operational complexity—must be carefully considered. These factors make it less suitable for certain applications or businesses with limited resources. Understanding these limitations is crucial for making informed decisions about whether induction soldering is the right choice for a specific use case.
Summary Table:
Disadvantage | Details |
---|---|
High Initial Cost | Expensive equipment and infrastructure; barrier for small-scale operations. |
Complex Process and Operation | Requires specialized training and precise parameter control. |
Material Limitations | Best for conductive metals; challenges with non-conductive materials. |
Lack of Refining Capacity | No material purification during the process; pre-processing required. |
Oxidation and Alloying Loss | High temperatures cause oxidation and loss of critical alloying elements. |
Energy Consumption | Can be energy-intensive, especially at high frequencies. |
Limited Flexibility | Less effective for small or complex parts; custom coils may be needed. |
Safety Concerns | High temperatures and electromagnetic fields pose risks to operators. |
Need help deciding if induction soldering is right for your application? Contact our experts today for personalized advice!