Plasma-enhanced chemical vapor deposition (PECVD) is a widely used technique for depositing thin films, particularly in semiconductor and optical industries. While it offers several advantages, such as low-temperature operation and the ability to coat complex geometries, it also has notable disadvantages. These include high equipment and operational costs, complexity in process control, limitations in substrate size, and challenges in achieving uniform film quality. Additionally, PECVD often involves hazardous gases, raising health and safety concerns. Understanding these drawbacks is crucial for equipment and consumable purchasers to make informed decisions.
Key Points Explained:
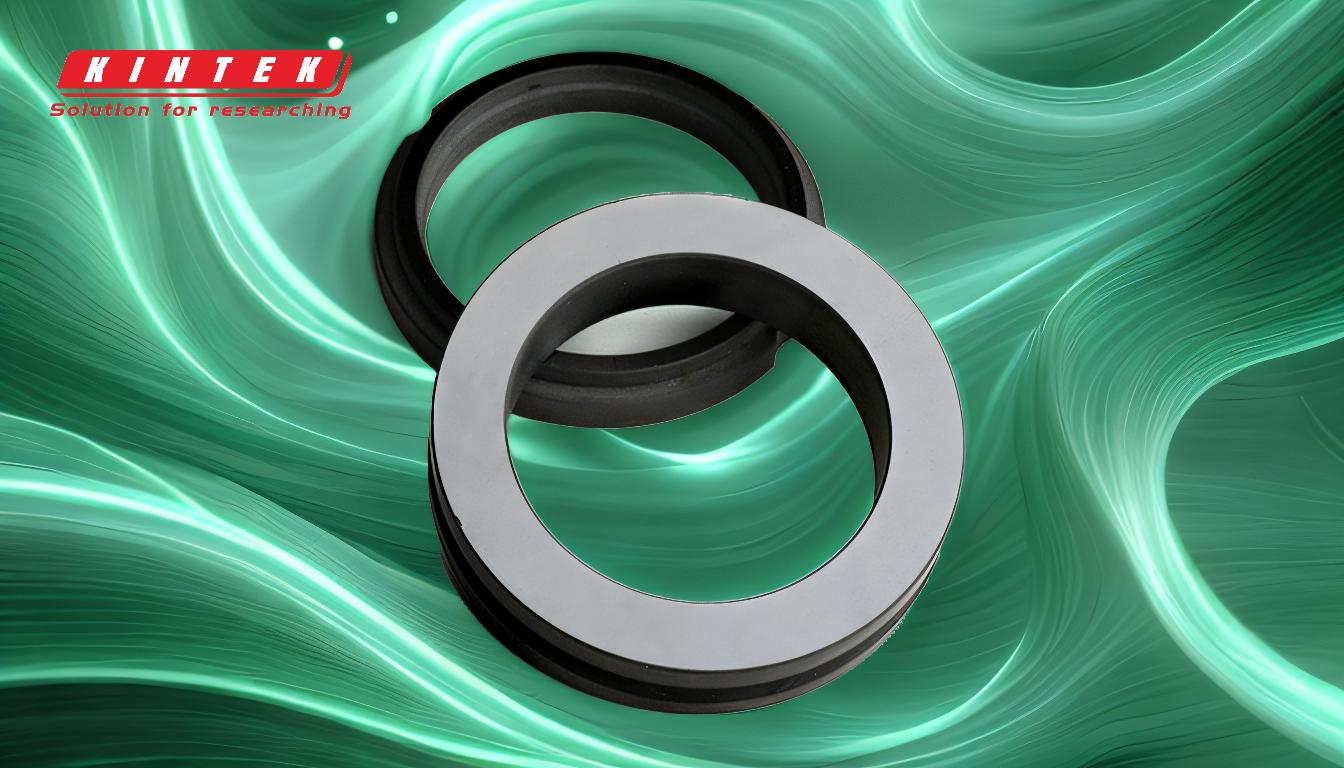
-
High Equipment and Operational Costs:
- PECVD systems are expensive due to the sophisticated technology required to generate and maintain plasma. The equipment includes vacuum chambers, gas delivery systems, and high-frequency power supplies, which contribute to the overall cost.
- Operational costs are also high, as the process consumes significant amounts of energy and requires precise control over parameters like gas flow rates, pressure, and temperature.
-
Complexity in Process Control:
- PECVD requires precise control over multiple parameters, including gas composition, flow rates, substrate temperature, and plasma power. Any deviation can lead to defects in the deposited film, such as poor adhesion, non-uniform thickness, or cracking.
- The complexity increases when depositing multi-component materials, as variations in vapor pressure, nucleation, and growth rates can result in heterogeneous compositions.
-
Limitations in Substrate Size:
- The size of the vacuum chamber in PECVD systems limits the size of substrates that can be processed. This makes it difficult to coat larger surfaces or complex geometries, which can be a significant drawback for industries requiring large-scale production.
- Additionally, parts often need to be broken down into individual components for processing, adding to the complexity and time required.
-
Challenges in Achieving Uniform Film Quality:
- While PECVD can produce high-quality thin films, achieving uniform thickness and composition across the entire substrate can be challenging. This is particularly true for substrates with complex geometries or when depositing multi-component materials.
- The process is often described as "all or nothing," meaning it can be difficult to achieve partial coverage or to completely cover a material without defects.
-
Health and Safety Concerns:
- PECVD processes often involve hazardous gases and chemicals, such as silane, ammonia, and various fluorocarbons. These substances can pose significant health and safety risks, requiring stringent safety measures and proper ventilation systems.
- The use of hazardous materials also complicates the disposal of waste products, adding to the operational challenges and costs.
-
Limited to Thin Films:
- PECVD is primarily suited for depositing thin films with thicknesses ranging from a few nanometers to a few micrometers. This makes it unsuitable for applications requiring thicker films or three-dimensional structures.
- The technique's limitation to thin films can be a significant drawback for industries needing bulk material deposition or thicker coatings.
-
Temperature Constraints:
- Although PECVD operates at lower temperatures compared to traditional CVD, it still requires elevated temperatures, which can be problematic for heat-sensitive substrates. This limits the range of materials that can be effectively coated using PECVD.
-
Comparison with MPCVD:
- While PECVD has its disadvantages, it's worth noting that microwave plasma chemical vapor deposition (MPCVD) offers some advantages, such as the ability to generate high-density plasma without the use of metal electrodes, leading to more stable and high-quality film growth. However, MPCVD also shares some of the drawbacks of PECVD, including high equipment costs and complexity.
In summary, while PECVD is a powerful technique for thin film deposition, its high costs, complexity, and limitations in substrate size and film quality make it less suitable for certain applications. Equipment and consumable purchasers should carefully consider these factors when selecting a deposition method for their specific needs.
Summary Table:
Disadvantage | Details |
---|---|
High Equipment and Operational Costs | Expensive systems due to sophisticated technology; high energy consumption and precise control. |
Complexity in Process Control | Requires precise control over gas composition, flow rates, and temperature; deviations cause defects. |
Limitations in Substrate Size | Vacuum chamber size restricts substrate dimensions; challenging for large-scale production. |
Challenges in Uniform Film Quality | Difficulty achieving uniform thickness and composition, especially on complex geometries. |
Health and Safety Concerns | Use of hazardous gases like silane and ammonia; requires stringent safety measures. |
Limited to Thin Films | Suitable only for thin films (nanometers to micrometers); unsuitable for thicker coatings. |
Temperature Constraints | Elevated temperatures can limit use on heat-sensitive substrates. |
Need help choosing the right deposition method? Contact our experts today for tailored advice!