Spray pyrolysis, while a versatile and widely used technique for producing fine powders and thin films, has several disadvantages that can limit its application and efficiency. These drawbacks include high operational and investment costs, technical challenges related to heat transfer and reactor design, the production of harmful by-products, and difficulties in scaling the technology for real-world applications. Additionally, the process often requires sophisticated monitoring and air purification systems to comply with environmental regulations, further increasing the complexity and cost. Below, we explore these disadvantages in detail.
Key Points Explained:
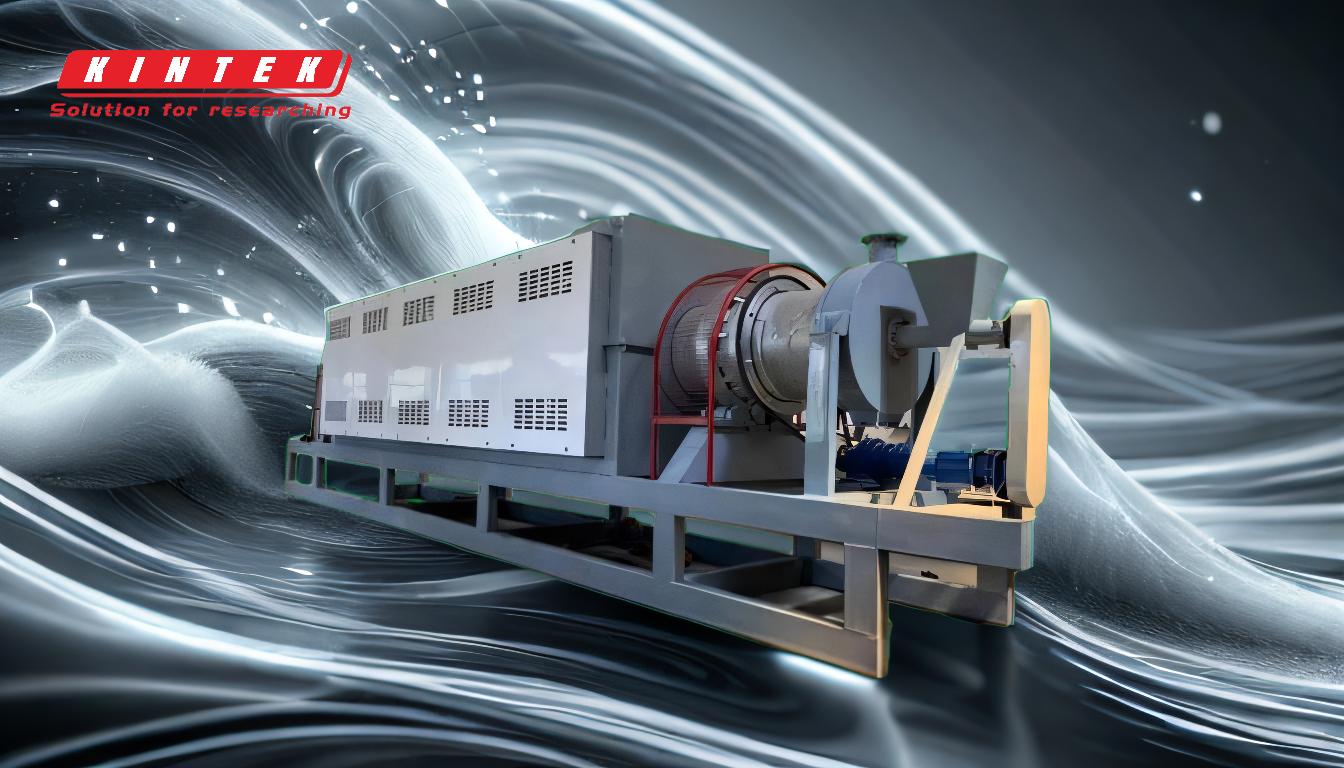
-
High Operational and Investment Costs:
- Spray pyrolysis involves complex equipment and processes, which can be expensive to set up and maintain. The need for high-purity precursors, precise control systems, and energy-intensive heating mechanisms contributes to the overall cost.
- The process often requires an air purification installation to treat flue gases, adding to the operational expenses. Compliance with environmental regulations, such as EU clean air standards, can further escalate costs due to the need for advanced flue gas clean-up systems.
-
Technical Challenges in Heat Transfer and Reactor Design:
- Achieving efficient heat transfer into solid biomass particles is a significant challenge in spray pyrolysis. The process often requires high heating rates, which can be difficult to achieve consistently.
- Reactor designs must be optimized to ensure uniform heat distribution and prevent hot spots or cold zones, which can lead to incomplete pyrolysis or uneven product quality. This may involve the use of solid heat carriers, hot gas streams, or indirect heat exchange via reactor walls or built-in tubes/plates.
-
Production of Harmful By-Products:
- The thermal decomposition of materials during spray pyrolysis can generate damaging chemicals and unwanted by-products. These substances must be removed from the flue gas to comply with environmental regulations, adding complexity to the process.
- The produced ashes often contain high levels of heavy metals and are classified as dangerous waste, requiring proper disposal methods. This not only increases operational costs but also poses environmental and safety risks.
-
Variability of Feed Materials:
- The performance of spray pyrolysis can be highly dependent on the quality and consistency of the feedstock. Variability in feed materials, such as moisture content, particle size, and chemical composition, can lead to inconsistent product quality and process inefficiencies.
- Sophisticated monitoring and auto-adjusting systems are often required to handle this variability, further increasing the complexity and cost of the process.
-
Difficulty in Scaling for Real-World Applications:
- While spray pyrolysis has been successfully demonstrated at laboratory and pilot scales, scaling the technology for industrial applications remains a significant challenge. Factors such as reactor design, heat transfer efficiency, and feedstock logistics become more complex at larger scales.
- The variability of real-world feed materials and the need for robust, scalable systems have limited the global adoption and reliability of spray pyrolysis for large-scale applications.
-
Environmental and Regulatory Challenges:
- The production of harmful by-products and the need for flue gas treatment make spray pyrolysis a technically demanding process. Compliance with stringent environmental regulations, such as those governing air quality and waste disposal, can be both challenging and costly.
- The disposal of dangerous waste, such as heavy metal-containing ashes, requires specialized handling and treatment, further adding to the operational burden.
In summary, while spray pyrolysis offers several advantages, such as the ability to produce fine powders and thin films with controlled properties, its disadvantages—including high costs, technical challenges, harmful by-products, and scalability issues—must be carefully considered. These factors can limit its applicability in certain contexts and necessitate ongoing research and development to overcome these challenges.
Summary Table:
Disadvantage | Key Details |
---|---|
High Operational and Investment Costs | Complex equipment, high-purity precursors, and air purification increase costs. |
Technical Challenges | Heat transfer inefficiencies and reactor design complexities. |
Harmful By-Products | Generates damaging chemicals and heavy metal-containing ashes. |
Variability of Feed Materials | Inconsistent feedstock quality affects product uniformity. |
Scaling Difficulties | Challenges in reactor design and feedstock logistics at industrial scales. |
Environmental and Regulatory Issues | Compliance with strict regulations increases complexity and costs. |
Need help overcoming the challenges of spray pyrolysis? Contact our experts today for tailored solutions!