Thermal evaporation is a widely used physical vapor deposition (PVD) technique, but it has several disadvantages that can affect its efficiency, scalability, and the quality of the deposited films. Key drawbacks include high impurity levels, low-density film quality, moderate film stress, challenges in achieving uniform thickness, and sensitivity to contamination. Additionally, issues like boat cracking, thermal shock, and limited scalability further complicate its use. While some of these issues can be mitigated with techniques like ion-assist or careful power management, they remain significant limitations for certain applications.
Key Points Explained:
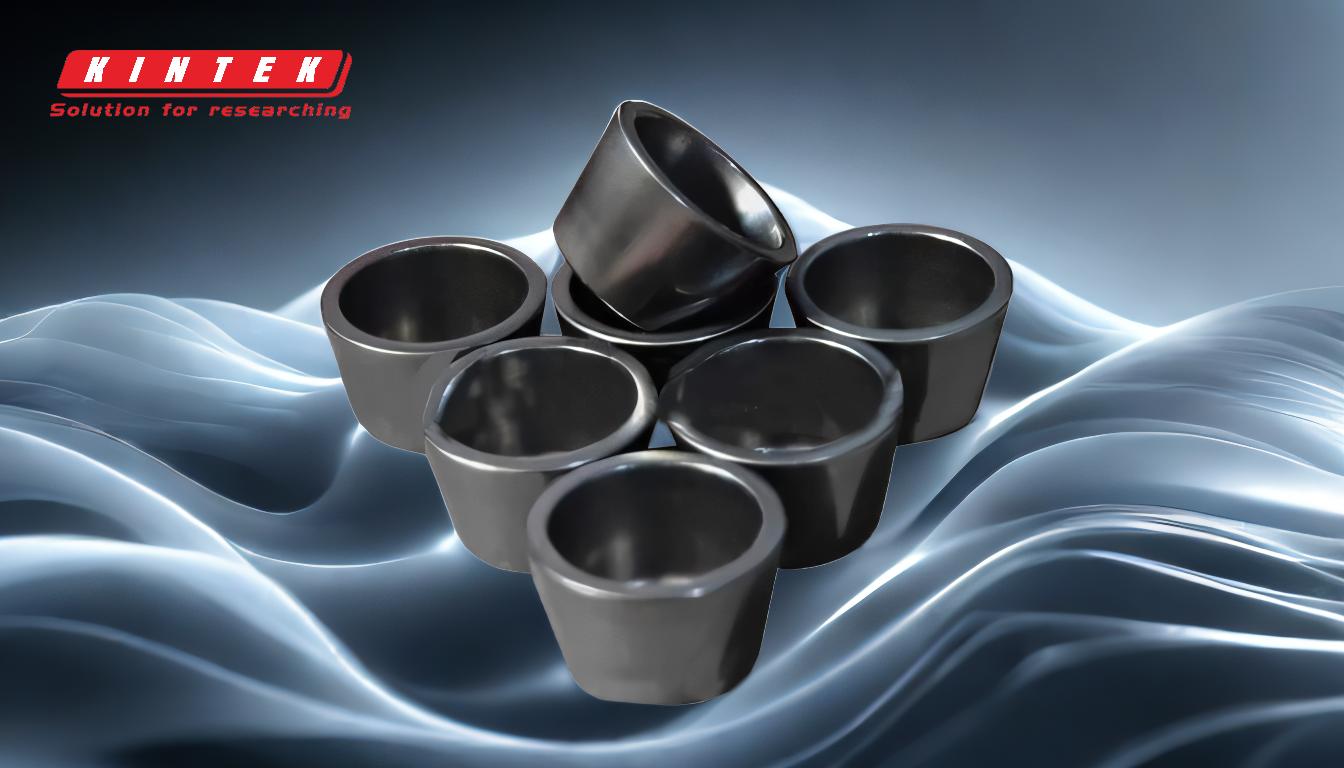
-
High Impurity Levels
- Thermal evaporation is known for having the highest impurity levels among PVD methods. This is due to the potential for contamination from the crucible or boat materials, especially at high temperatures.
- Graphite crucibles, often used for high-temperature evaporation, can introduce carbon impurities into the deposited material.
- Contamination-free crucibles are expensive, making it challenging to achieve high-purity coatings cost-effectively.
-
Low-Density Film Quality
- Films produced by thermal evaporation tend to have low density, which can affect their mechanical and optical properties.
- This issue can be partially addressed using ion-assist techniques, but these add complexity and cost to the process.
-
Moderate Film Stress
- Thermal evaporation often results in films with moderate stress levels, which can lead to cracking or delamination over time.
- This stress is primarily caused by the thermal expansion mismatch between the substrate and the deposited material during cooling.
-
Challenges in Achieving Uniform Thickness
- Without the use of masks or planetary systems, achieving uniform film thickness is difficult.
- This limitation makes thermal evaporation less suitable for applications requiring precise, uniform coatings over large or complex surfaces.
-
Sensitivity to Contamination
- The process requires a high-vacuum environment to minimize contamination, which adds to the operational complexity and cost.
- Contamination from the crucible or boat materials can further degrade the quality of the deposited films.
-
Boat Cracking and Thermal Shock
- Boat cracking is a common issue caused by alloying between the boat and evaporant materials at high temperatures. Once cracked, the boat must be replaced, increasing costs.
- Thermal shock, resulting from rapid heating and cooling, can also lead to boat cracking. To mitigate this, power must be ramped up and down smoothly, which adds complexity to the process.
-
Limited Scalability
- Thermal evaporation is less scalable compared to other PVD methods, particularly at reduced deposition rates.
- This limitation makes it less suitable for large-scale industrial applications where high throughput is required.
-
Temperature Constraints and Cooling Stresses
- The deposition process is constrained by temperature limits, which can affect the types of materials that can be evaporated.
- Undesirable stresses can develop during cooling, further compromising the integrity of the deposited films.
-
Moderate System Complexity and Costs
- While thermal evaporation systems are generally simpler than some other PVD methods, they still involve moderate complexity and costs, especially when additional features like ion-assist or planetary systems are required.
-
Limited Material Compatibility
- Not all materials are suitable for thermal evaporation, particularly those with very high melting points or those that react with crucible materials.
- This limits the versatility of the technique for certain advanced applications.
In summary, while thermal evaporation is a versatile and widely used deposition technique, its disadvantages—such as high impurity levels, low-density films, moderate stress, and challenges in achieving uniformity—make it less suitable for certain high-precision or large-scale applications. Careful process optimization and the use of auxiliary techniques can mitigate some of these issues, but they remain inherent limitations of the method.
Summary Table:
Disadvantage | Explanation |
---|---|
High Impurity Levels | Contamination from crucibles or boats, especially at high temperatures. |
Low-Density Film Quality | Films lack density, affecting mechanical and optical properties. |
Moderate Film Stress | Stress from thermal expansion mismatch can cause cracking or delamination. |
Uniform Thickness Challenges | Difficult to achieve without masks or planetary systems. |
Sensitivity to Contamination | Requires high-vacuum environments, increasing complexity and cost. |
Boat Cracking and Thermal Shock | Cracking due to alloying or thermal shock, requiring careful power management. |
Limited Scalability | Less suitable for large-scale applications due to reduced deposition rates. |
Temperature Constraints | Material limitations and cooling stresses affect film integrity. |
Moderate System Complexity | Additional features like ion-assist increase costs and complexity. |
Limited Material Compatibility | Not all materials are suitable, especially high-melting-point or reactive ones. |
Need help optimizing your thermal evaporation process? Contact our experts today!