Two-plate molds are widely used in injection molding due to their simplicity and cost-effectiveness. However, they come with certain disadvantages, particularly in multi-cavity designs. One of the primary challenges is balancing the flow of molten plastic across multiple cavities, which can lead to uneven filling and defects in the final product. Additionally, the alignment of the parting line with the gate in a two-plate mold can complicate the design and manufacturing process. These limitations can impact the efficiency, quality, and cost of production, making it essential to carefully evaluate their suitability for specific applications.
Key Points Explained:
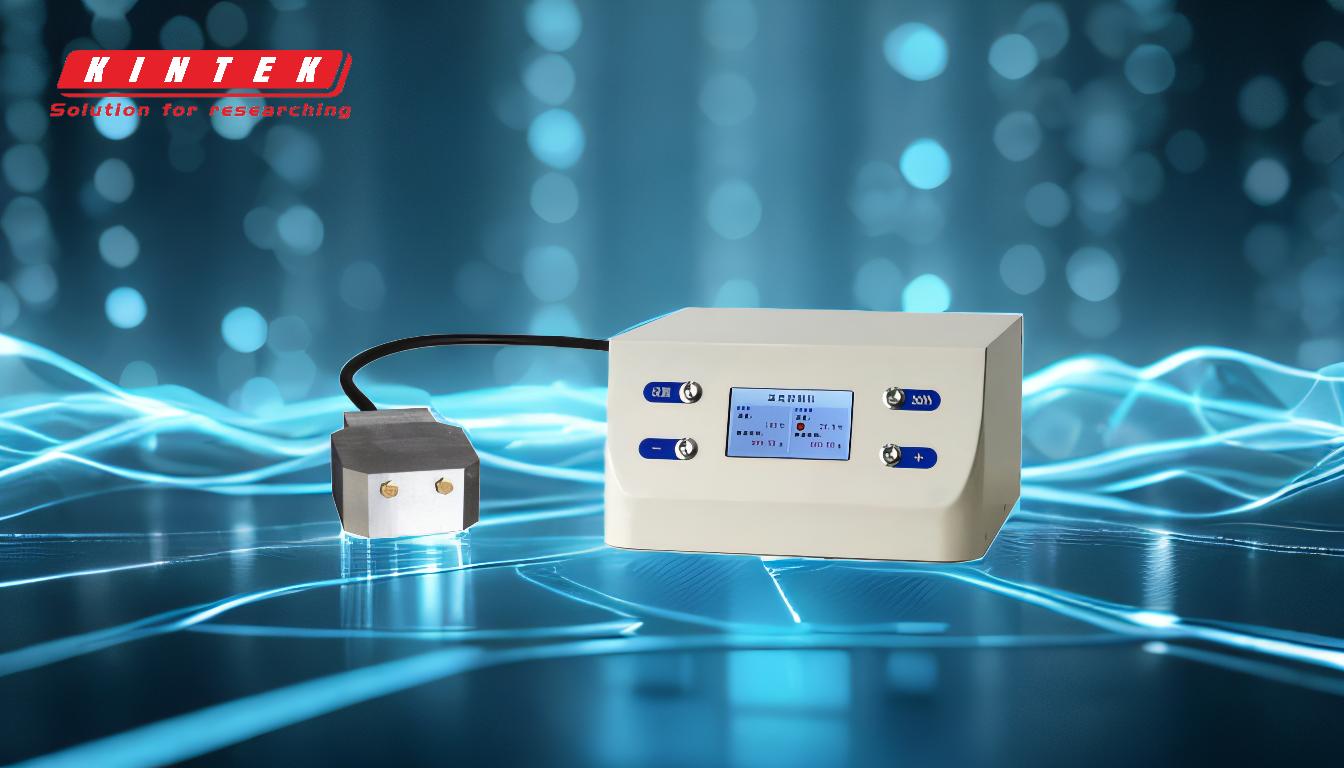
-
Challenges in Balancing Molten Plastic Flow:
- In multi-cavity two-plate molds, ensuring uniform distribution of molten plastic to each cavity is difficult.
- Uneven flow can result in defects such as short shots, warping, or inconsistent part dimensions.
- This issue is exacerbated in complex designs where cavities are located at varying distances from the gate.
-
Alignment of Parting Line with Gate:
- The parting line in a two-plate mold must align with the gate, which restricts design flexibility.
- This alignment can complicate the mold design, especially for intricate parts or multi-cavity setups.
- It may also increase the risk of flash formation or other defects at the parting line.
-
Limited Design Flexibility:
- Two-plate molds are less versatile compared to three-plate molds or hot runner systems.
- They are not ideal for parts requiring complex gating or those with specific aesthetic requirements.
- The simplicity of two-plate molds often comes at the cost of reduced customization options.
-
Higher Risk of Defects:
- Due to the challenges in flow balancing and gate alignment, two-plate molds are more prone to defects.
- Common issues include weld lines, air traps, and inconsistent part quality.
- These defects can increase scrap rates and production costs.
-
Longer Cycle Times:
- The limitations of two-plate molds can lead to longer cooling and cycle times.
- This is particularly true for multi-cavity molds where uneven cooling can occur.
- Longer cycle times reduce overall production efficiency and increase operational costs.
-
Higher Maintenance Requirements:
- The complexity of balancing flow and aligning gates can lead to increased wear and tear on the mold.
- Regular maintenance is required to ensure consistent performance, adding to the total cost of ownership.
-
Not Suitable for All Applications:
- Two-plate molds are best suited for simple parts with straightforward gating requirements.
- For complex parts or high-precision applications, alternative mold designs (e.g., three-plate molds or hot runner systems) may be more appropriate.
By understanding these disadvantages, manufacturers can make informed decisions about whether a two-plate mold is the right choice for their specific production needs. While they offer simplicity and cost savings, their limitations must be carefully weighed against the requirements of the project.
Summary Table:
Disadvantage | Impact |
---|---|
Flow Balancing Challenges | Uneven filling, defects like short shots, warping, or inconsistent dimensions. |
Parting Line Alignment | Restricted design flexibility, increased risk of flash formation. |
Limited Design Flexibility | Less versatile for complex parts or specific aesthetic requirements. |
Higher Risk of Defects | Weld lines, air traps, and inconsistent part quality increase scrap rates. |
Longer Cycle Times | Uneven cooling leads to reduced production efficiency. |
Higher Maintenance Needs | Increased wear and tear, requiring regular upkeep. |
Not Suitable for All Applications | Best for simple parts; complex designs may need alternative molds. |
Need help choosing the right mold for your project? Contact our experts today for tailored solutions!