Biomass gasification is a thermochemical process that converts biomass into various end products, including combustible gases, biochar, wood vinegar, wood tar, and ash. These products have diverse applications, ranging from direct energy generation to higher-value commodity production. The specific end products depend on the type of gasification process (air, oxygen, or steam gasification) and the operating conditions. Combustible gases like carbon monoxide, hydrogen, and methane are primary outputs, suitable for power and heat generation. Biochar, wood vinegar, and tar are valuable by-products with applications in agriculture, chemicals, and energy. Ash and other hydrocarbons are also generated, which can be further processed or utilized in various industrial applications.
Key Points Explained:
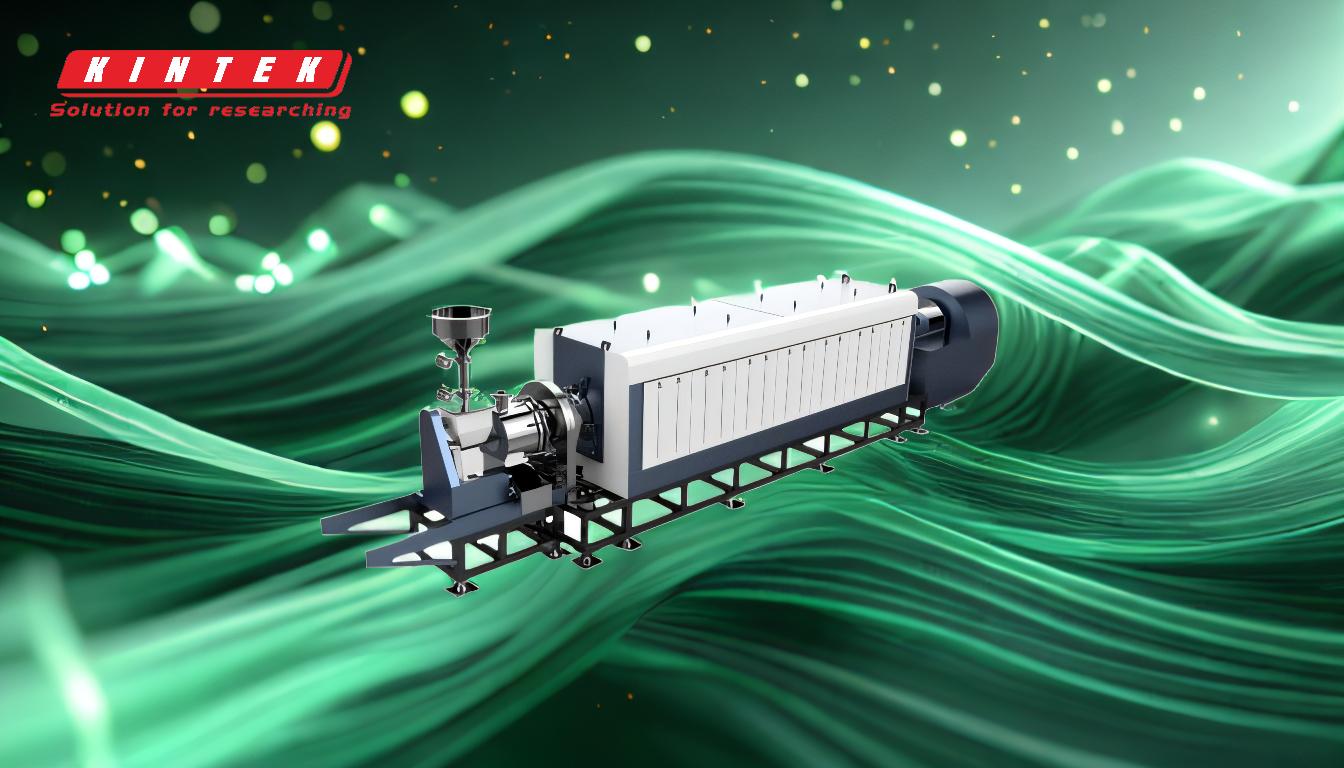
-
Combustible Gases
- Composition: The primary combustible gases produced during biomass gasification include carbon monoxide (CO), hydrogen (H₂), and methane (CH₄).
- Applications: These gases are used for power and heat generation, either directly in boilers, gas engines, or turbines, or as syngas for further processing into fuels like diesel, dimethyl ether, or gasoline.
- Calorific Value: The heating value of the gas depends on the gasification method. Air gasification produces low-calorific gas (4–6 MJ/nm³), oxygen gasification yields intermediate-calorific gas (10–12 MJ/m³), and steam gasification generates higher-calorific gas (15–20 MJ/m³).
-
Biochar (Biomass Charcoal)
- Formation: Biochar is a solid residue formed during the gasification process.
- Applications: It is widely used in agriculture as a soil amendment to improve soil fertility and carbon sequestration. It can also be used as a fuel or further processed into activated carbon for filtration and purification applications.
-
Wood Vinegar
- Composition: Wood vinegar is a liquid by-product containing water-soluble carbon species, organic acids, and other compounds.
- Applications: It is used in agriculture as a natural pesticide, herbicide, and soil conditioner. It also has applications in the chemical industry for producing organic solvents and other chemicals.
-
Wood Tar
- Formation: Wood tar is a viscous liquid produced during the gasification process.
- Applications: It is used in the production of adhesives, preservatives, and coatings. It can also be further refined into higher-value chemicals or used as a fuel.
-
Ash
- Formation: Ash is the inorganic residue left after the gasification process.
- Applications: It can be used as a soil amendment to provide essential minerals or as a raw material in the construction industry for making cement or bricks.
-
Other Hydrocarbons
- Formation: These are minor by-products formed during gasification.
- Applications: They can be processed further or used as feedstocks for chemical synthesis.
-
Gasification Process Variations
- Air Gasification: Produces low-calorific gas suitable for local energy generation but not for pipeline transportation.
- Oxygen Gasification: Yields intermediate-calorific gas, which can be used for limited pipeline transportation or converted into liquid fuels.
- Steam Gasification: Generates high-calorific gas with greater combustion heat, often implemented in fluidized bed reactors for efficient energy production.
-
Marketability of End Products
- The end products of biomass gasification, such as biochar, wood vinegar, and tar, are in demand in various markets due to their versatility and applications in agriculture, energy, and chemicals.
By understanding the end products and their applications, purchasers of biomass gasification equipment can make informed decisions about the type of gasification process to implement based on their specific needs and market opportunities.
Summary Table:
End Product | Composition/Formation | Applications |
---|---|---|
Combustible Gases | CO, H₂, CH₄ | Power/heat generation, syngas for fuels |
Biochar | Solid residue | Soil amendment, fuel, activated carbon |
Wood Vinegar | Water-soluble carbon compounds | Pesticide, herbicide, soil conditioner, chemicals |
Wood Tar | Viscous liquid | Adhesives, preservatives, coatings, fuel |
Ash | Inorganic residue | Soil amendment, construction materials |
Other Hydrocarbons | Minor by-products | Chemical synthesis feedstock |
Ready to explore biomass gasification solutions for your needs? Contact us today!