Fast pyrolysis is a thermal conversion process designed to efficiently convert biomass into bio-oil, biogas, and other by-products. It operates at moderate temperatures (400–600°C) with high heating rates (10–200°C/s) and short residence times (0.5–10 seconds). The process maximizes bio-oil yields, which can reach 50–70 wt% on a dry biomass basis, making it a promising method for producing liquid fuels and chemical commodities. Key features include precise temperature control, rapid cooling of products, and a variety of reactor configurations tailored to optimize liquid yields. The bio-oil produced can be used in boilers, engines, turbines, and as a feedstock for chemical production.
Key Points Explained:
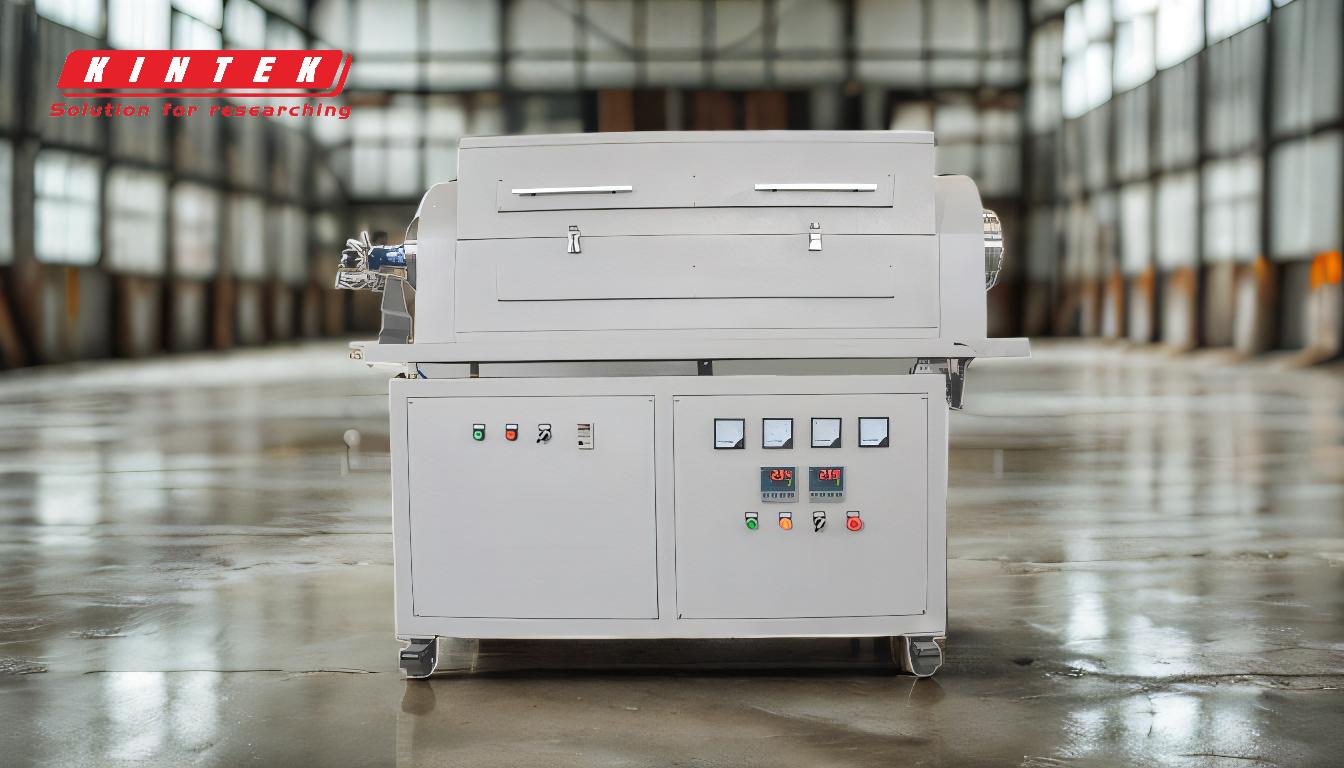
-
High Heating Rates (10–200°C/s):
- Fast pyrolysis relies on extremely high heating rates to rapidly decompose biomass into vapors, liquids, and gases. This rapid heating minimizes secondary reactions that could degrade the quality of the bio-oil.
- High heating rates ensure that the biomass is quickly brought to the desired pyrolysis temperature, which is critical for maximizing liquid yields.
-
Short Residence Time (0.5–10 seconds):
- The residence time in fast pyrolysis is kept very short (typically less than one second) to prevent further cracking of the primary pyrolysis vapors into non-condensable gases and char.
- Short residence times are essential for maintaining high bio-oil yields and ensuring that the process remains efficient.
-
Moderate Pyrolysis Temperatures (400–600°C):
- The process operates within a moderate temperature range to maximize the production of condensable vapors, which are then rapidly cooled to form bio-oil.
- Temperatures above 700°C tend to favor gas production, while lower temperatures (up to 650°C) are optimal for liquid yields.
-
High Bio-Oil Yields (50–70 wt%):
- Fast pyrolysis is designed to maximize the yield of bio-oil, which can account for 50–70% of the dry biomass weight. This high yield makes the process economically viable for producing liquid fuels.
- The bio-oil produced is a versatile product that can be used directly as fuel or further refined into chemicals.
-
Rapid Cooling of Products:
- After pyrolysis, the vapors are rapidly cooled to condense into bio-oil. This step is crucial to prevent the re-polymerization of vapors into char or non-condensable gases.
- Rapid cooling ensures that the bio-oil retains its quality and is suitable for downstream applications.
-
Inert Atmosphere:
- The process is carried out in an inert atmosphere (typically nitrogen) to prevent oxidation and unwanted chemical reactions that could degrade the quality of the bio-oil.
- An inert environment ensures that the pyrolysis reactions are controlled and predictable.
-
Wide Range of Reactor Configurations:
- Various reactor designs, such as fluidized beds, rotating cones, and ablative reactors, have been developed to meet the stringent requirements of fast pyrolysis.
- These configurations are optimized to achieve high heat transfer rates, precise temperature control, and efficient vapor recovery.
-
Versatile Applications of Bio-Oil:
- The bio-oil produced can be used as a fuel in boilers, engines, and turbines, or as a feedstock for the production of chemicals and other value-added products.
- This versatility makes fast pyrolysis an attractive option for both energy and chemical industries.
-
Controlled Pyrolysis Conditions:
- The process requires careful control of temperature, heating rate, and residence time to ensure optimal yields and product quality.
- Advanced control systems are often employed to maintain these conditions consistently.
-
Environmental and Economic Benefits:
- Fast pyrolysis offers a sustainable way to convert biomass into renewable fuels and chemicals, reducing reliance on fossil fuels and lowering greenhouse gas emissions.
- The high efficiency and yield of the process make it economically competitive with traditional fuel production methods.
By focusing on these essential features, fast pyrolysis provides a highly efficient and scalable method for converting biomass into valuable liquid fuels and chemicals, making it a key technology in the transition to a more sustainable energy future.
Summary Table:
Key Feature | Details |
---|---|
Heating Rates | 10–200°C/s for rapid biomass decomposition and high liquid yields. |
Residence Time | 0.5–10 seconds to prevent secondary reactions and maximize bio-oil quality. |
Temperature Range | 400–600°C for optimal condensable vapor production. |
Bio-Oil Yields | 50–70 wt% on a dry biomass basis. |
Rapid Cooling | Ensures bio-oil quality by preventing re-polymerization. |
Inert Atmosphere | Prevents oxidation and ensures controlled pyrolysis reactions. |
Reactor Configurations | Fluidized beds, rotating cones, and ablative reactors for optimized yields. |
Applications of Bio-Oil | Used in boilers, engines, turbines, and as a chemical feedstock. |
Environmental Benefits | Reduces fossil fuel reliance and greenhouse gas emissions. |
Economic Viability | High efficiency and yield make it competitive with traditional methods. |
Discover how fast pyrolysis can transform your biomass into renewable energy—contact us today for expert guidance!