Physical Vapor Deposition (PVD) is a versatile vacuum-based coating process used to deposit thin films of material onto substrates. The process involves vaporizing a solid material in a vacuum environment and then condensing it onto a substrate to form a thin, uniform coating. PVD is widely used in industries such as automotive, cosmetics, home furnishings, and fashion due to its ability to create durable, corrosion-resistant, and scratch-resistant coatings. The main types of PVD processes include thermal evaporation, sputter deposition, and ion plating, with advanced techniques like electron-beam physical vapor deposition, cathodic arc deposition, and laser ablation also gaining prominence.
Key Points Explained:
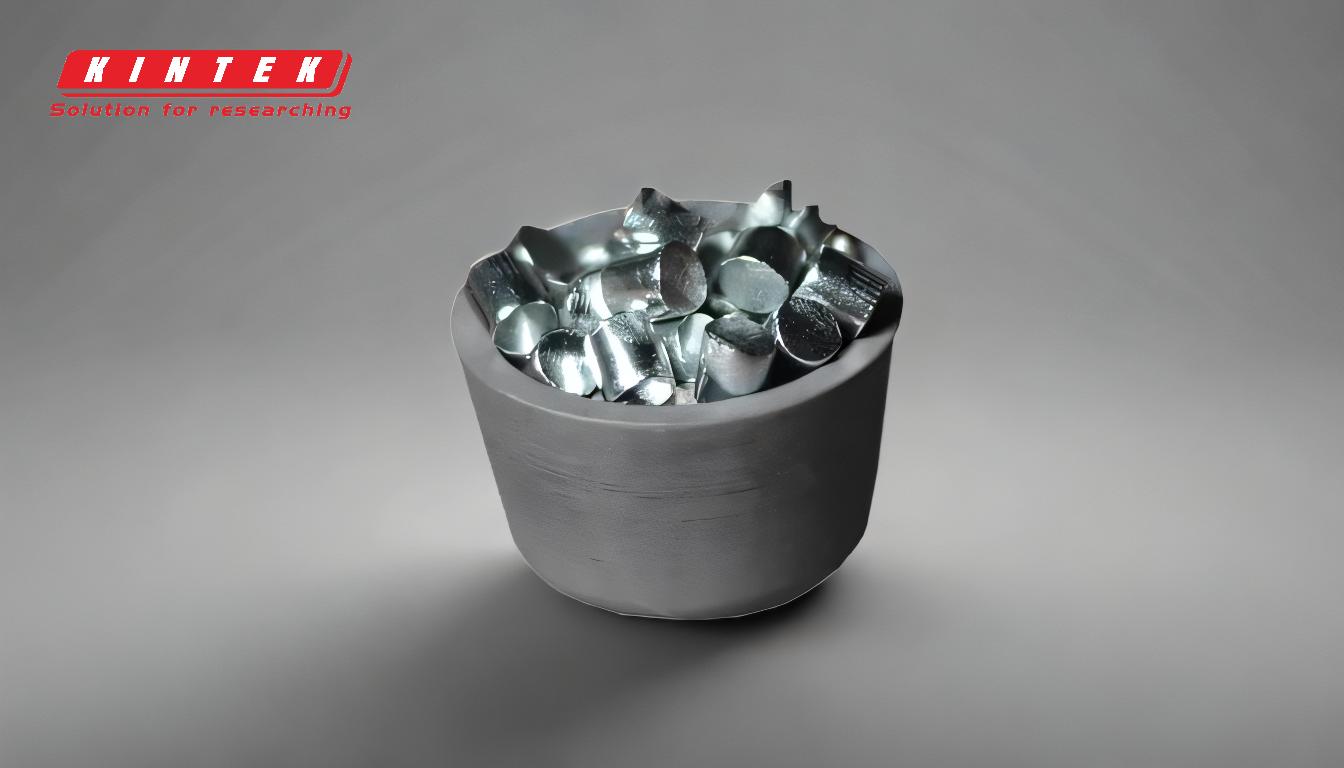
-
Thermal Evaporation:
- Process: In thermal evaporation, the source material is heated to a high temperature in a vacuum until it vaporizes. The vaporized atoms then travel through the vacuum and condense on the substrate, forming a thin film.
- Applications: This method is commonly used for depositing metals and simple compounds. It is favored for its simplicity and ability to produce high-purity films.
- Example: Thermal evaporation is often used in the production of optical coatings, such as anti-reflective coatings on lenses.
-
Sputter Deposition:
- Process: Sputter deposition involves bombarding a target material with high-energy ions, causing atoms to be ejected from the target. These ejected atoms then deposit onto the substrate.
- Types: Common types include DC sputtering, RF sputtering, and magnetron sputtering. Magnetron sputtering is particularly popular due to its high deposition rates and ability to produce dense, uniform films.
- Applications: Sputter deposition is widely used in the semiconductor industry for depositing thin films of metals, oxides, and nitrides.
- Example: It is used to create the thin metal layers in integrated circuits and solar cells.
-
Ion Plating:
- Process: Ion plating combines elements of both evaporation and sputtering. The substrate is biased with a negative voltage, attracting positively charged ions from the vaporized source material. This results in a more adherent and dense coating.
- Applications: Ion plating is used for applications requiring high adhesion and durability, such as in the aerospace and automotive industries.
- Example: It is used to coat turbine blades with protective layers to enhance their resistance to high temperatures and corrosion.
-
Electron-Beam Physical Vapor Deposition (EBPVD):
- Process: EBPVD uses a focused electron beam to vaporize the source material. The high-energy electron beam allows for precise control over the deposition process and is capable of depositing high-melting-point materials.
- Applications: This method is used in the aerospace industry for depositing thermal barrier coatings on engine components.
- Example: EBPVD is used to apply ceramic coatings on jet engine turbine blades to protect them from extreme heat.
-
Cathodic Arc Deposition:
- Process: In cathodic arc deposition, an electric arc is used to vaporize material from a cathode target. The vaporized material is then deposited onto the substrate.
- Applications: This method is known for producing very hard and wear-resistant coatings, making it suitable for cutting tools and wear-resistant components.
- Example: It is used to coat drill bits and cutting tools with titanium nitride (TiN) to enhance their hardness and longevity.
-
Laser Ablation:
- Process: Laser ablation involves using a high-power laser to vaporize the source material. The vaporized material is then deposited onto the substrate.
- Applications: This method is used for depositing complex materials, such as high-temperature superconductors and complex oxides.
- Example: Laser ablation is used in the production of thin-film superconductors for electronic devices.
-
Reactive Deposition:
- Process: In reactive deposition, a reactive gas is introduced into the deposition chamber, where it reacts with the vaporized source material to form a compound film on the substrate.
- Applications: This method is used to deposit compound films such as oxides, nitrides, and carbides.
- Example: Reactive deposition is used to create titanium nitride (TiN) coatings, which are known for their hardness and golden color, often used in decorative applications.
-
Molecular Beam Epitaxy (MBE):
- Process: MBE is a highly controlled form of PVD where atoms or molecules are deposited onto a substrate in an ultra-high vacuum environment, allowing for the growth of single-crystal films.
- Applications: MBE is used in the semiconductor industry for the precise growth of thin films and quantum wells.
- Example: It is used to produce high-quality semiconductor layers for advanced electronic and optoelectronic devices.
-
Ion Beam Enhanced Deposition (IBED):
- Process: IBED combines ion implantation with PVD to enhance the adhesion and properties of the deposited film. The substrate is bombarded with ions during the deposition process, which improves the film's density and adhesion.
- Applications: This method is used for applications requiring high adhesion and dense films, such as in the aerospace and medical industries.
- Example: IBED is used to coat medical implants with biocompatible materials to improve their integration with body tissues.
-
Electric Spark Deposition:
- Process: Electric spark deposition uses electrical discharges to vaporize the source material, which is then deposited onto the substrate. This method allows for localized deposition and is often used for repair and surface modification.
- Applications: It is used for repairing damaged components and enhancing surface properties.
- Example: Electric spark deposition is used to repair worn-out machine parts by depositing a hard, wear-resistant coating.
These examples illustrate the diversity and versatility of PVD processes, each tailored to specific applications and material requirements. The choice of PVD method depends on factors such as the desired film properties, substrate material, and the specific application.
Summary Table:
PVD Process | Key Features | Applications |
---|---|---|
Thermal Evaporation | Heats material to vaporize; simple, high-purity films | Optical coatings (e.g., anti-reflective lenses) |
Sputter Deposition | Bombards target with ions; dense, uniform films | Semiconductor thin films (e.g., integrated circuits, solar cells) |
Ion Plating | Combines evaporation and sputtering; high adhesion, durable coatings | Aerospace and automotive coatings (e.g., turbine blades) |
EBPVD | Uses electron beams; precise, high-melting-point materials | Thermal barrier coatings (e.g., jet engine turbine blades) |
Cathodic Arc Deposition | Electric arc vaporization; hard, wear-resistant coatings | Cutting tools (e.g., titanium nitride-coated drill bits) |
Laser Ablation | High-power laser vaporization; complex material deposition | Thin-film superconductors (e.g., electronic devices) |
Reactive Deposition | Introduces reactive gas; forms compound films | Decorative coatings (e.g., titanium nitride coatings) |
Molecular Beam Epitaxy | Ultra-high vacuum; single-crystal film growth | Advanced semiconductor layers (e.g., optoelectronic devices) |
Ion Beam Enhanced Deposition | Combines ion implantation; high adhesion, dense films | Medical implants (e.g., biocompatible coatings) |
Electric Spark Deposition | Electrical discharges; localized deposition, repair | Surface modification (e.g., worn-out machine parts repair) |
Discover the perfect PVD solution for your needs—contact our experts today!