Selective Laser Sintering (SLS) is a complex additive manufacturing process influenced by multiple factors that determine the quality, efficiency, and properties of the final product. Key factors include temperature, heating rate, pressure, particle size, and material composition. Temperature governs sintering kinetics and material properties, while the heating rate affects densification and microstructure. Pressure aids in particle rearrangement and porosity reduction. Particle size and composition play critical roles in sintering behavior, with smaller particles and homogeneous compositions leading to improved densification and mechanical properties. Understanding these factors is essential for optimizing the SLS process and achieving high-quality parts.
Key Points Explained:
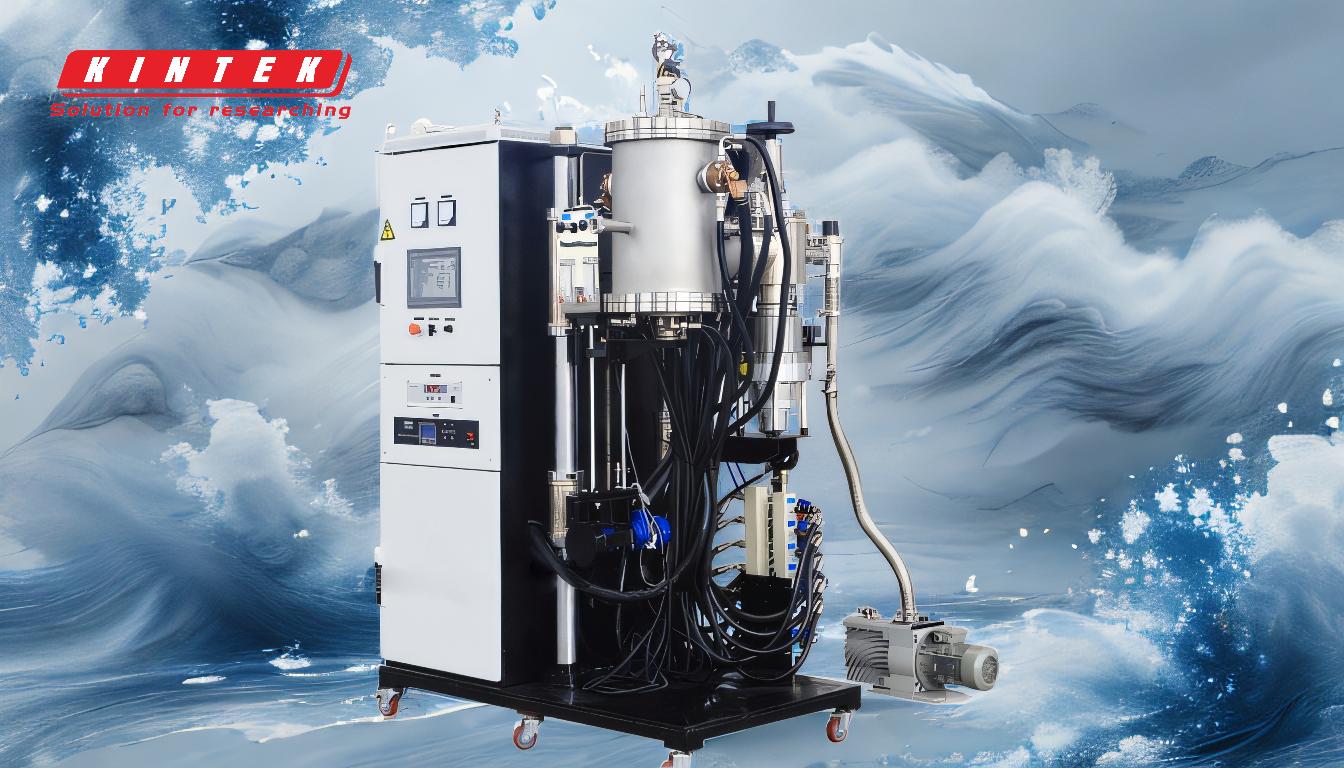
-
Temperature:
- Role: Temperature is a critical factor in SLS as it directly influences sintering kinetics and the final material properties. It determines the rate at which particles bond and the degree of densification.
- Impact: Higher temperatures generally accelerate sintering but must be carefully controlled to avoid defects such as warping or excessive grain growth. Optimal temperature ensures proper bonding without compromising part integrity.
-
Heating Rate:
- Role: The heating rate affects how quickly the material reaches the sintering temperature and influences the densification process.
- Impact: A controlled heating rate ensures uniform densification and minimizes thermal gradients, which can lead to internal stresses and part distortion. Rapid heating may cause incomplete sintering, while slow heating can result in excessive energy consumption.
-
Pressure:
- Role: Pressure, though not always applied in SLS, can enhance particle rearrangement and reduce porosity.
- Impact: Applied pressure helps in achieving better particle contact and densification, leading to improved mechanical properties. However, excessive pressure may cause deformation or damage to the part.
-
Particle Size:
- Role: Particle size significantly impacts sintering behavior, as smaller particles have higher surface energy and greater driving force for sintering.
- Impact: Smaller particles promote faster and more uniform densification, resulting in parts with higher density and better mechanical properties. Larger particles may lead to incomplete sintering and increased porosity.
-
Material Composition:
- Role: The composition of the material determines its sintering behavior, including melting point, thermal conductivity, and bonding characteristics.
- Impact: Homogeneous compositions with uniform particle distribution ensure consistent sintering and better part quality. Inhomogeneous compositions can lead to uneven densification and defects.
-
Laser Power and Scan Speed:
- Role: Laser power and scan speed are critical parameters in SLS that control the energy input and interaction time with the material.
- Impact: Higher laser power and slower scan speeds increase energy input, promoting better sintering but risking overheating. Lower power and faster speeds may result in insufficient sintering. Balancing these parameters is crucial for optimal part quality.
-
Layer Thickness:
- Role: Layer thickness affects the resolution and surface finish of the final part.
- Impact: Thinner layers provide higher resolution and smoother surfaces but increase build time. Thicker layers reduce build time but may compromise part accuracy and surface quality.
-
Atmosphere:
- Role: The sintering environment, typically an inert atmosphere, prevents oxidation and contamination.
- Impact: A controlled atmosphere ensures consistent material properties and prevents defects caused by oxidation or contamination. Inadequate atmosphere control can lead to part degradation.
-
Post-Processing:
- Role: Post-processing steps such as heat treatment or surface finishing can enhance part properties.
- Impact: Proper post-processing improves mechanical properties, dimensional accuracy, and surface finish. Neglecting post-processing may result in suboptimal part performance.
By carefully controlling and optimizing these factors, manufacturers can achieve high-quality SLS parts with desirable properties, ensuring the process is efficient and cost-effective.
Summary Table:
Factor | Role | Impact |
---|---|---|
Temperature | Governs sintering kinetics and material properties. | Higher temps accelerate sintering but risk defects; optimal temps ensure bonding. |
Heating Rate | Affects densification and microstructure. | Controlled heating ensures uniform densification; rapid heating may cause issues. |
Pressure | Enhances particle rearrangement and reduces porosity. | Improves densification but excessive pressure can deform parts. |
Particle Size | Smaller particles have higher surface energy for sintering. | Smaller particles lead to better densification and mechanical properties. |
Material Composition | Determines sintering behavior and bonding characteristics. | Homogeneous compositions ensure consistent sintering and part quality. |
Laser Power & Scan Speed | Controls energy input and interaction time. | Balancing these parameters is crucial for optimal sintering. |
Layer Thickness | Affects resolution and surface finish. | Thinner layers improve resolution but increase build time. |
Atmosphere | Prevents oxidation and contamination. | Controlled atmosphere ensures consistent material properties. |
Post-Processing | Enhances mechanical properties, accuracy, and surface finish. | Proper post-processing improves part performance. |
Ready to optimize your SLS process? Contact our experts today for tailored solutions!