The factors affecting the performance and efficiency of a ball mill can be categorized into three main areas: material characteristics, equipment design, and operating conditions. Material characteristics include the physical and chemical properties of the feed material, such as hardness, density, and moisture content. Equipment design factors encompass the drum diameter, length-to-diameter ratio, grinding media type and size, and the lining material. Operating conditions involve rotation speed, filling ratio of the mill, feed rate, and timely removal of the ground product. Understanding these factors is crucial for optimizing the grinding process and achieving desired milling outcomes.
Key Points Explained:
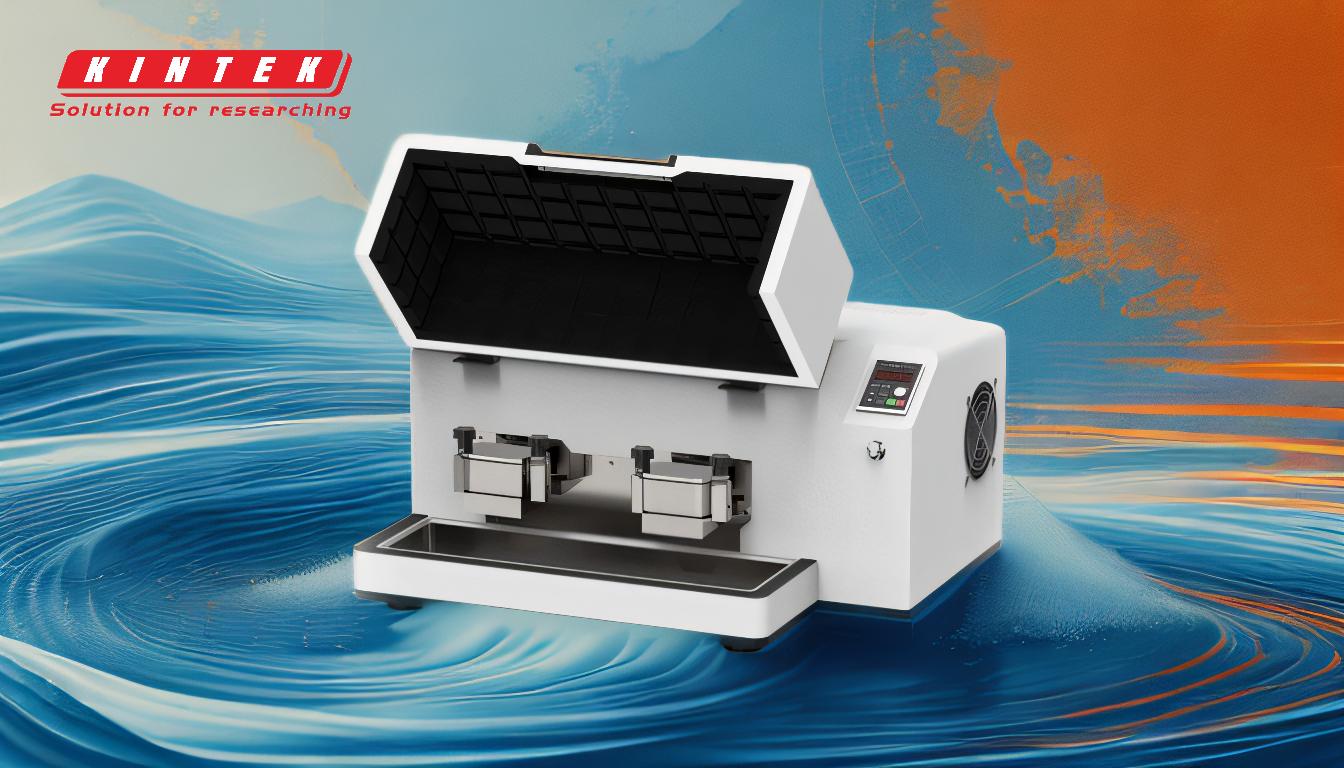
-
Material Characteristics:
- Hardness: Harder materials require more energy to grind, affecting the efficiency of the ball mill.
- Density: Denser materials may require adjustments in the grinding media to achieve effective milling.
- Moisture Content: High moisture content can lead to clogging and reduced grinding efficiency.
-
Equipment Design:
- Drum Diameter and Length-to-Diameter Ratio: The productivity of ball mills is influenced by the drum diameter and the optimal length-to-diameter ratio, typically between 1.56 and 1.64.
- Grinding Media: The size, type, and density of the grinding balls (steel, stainless steel, ceramic, or rubber) significantly impact the grinding efficiency.
- Lining Material: The inner surface of the mill is lined with abrasion-resistant materials like manganese steel or rubber to protect the shell and enhance grinding.
-
Operating Conditions:
- Rotation Speed: The speed at which the mill rotates affects the motion of the grinding media and the material, influencing the grinding efficiency.
- Filling Ratio: The percentage of the mill volume filled with grinding medium (balls) must be optimized to balance grinding efficiency and energy consumption.
- Feed Rate and Level: Controlling the feed rate and maintaining an appropriate level of material in the mill ensures consistent grinding and prevents overloading.
- Timely Removal of Ground Product: Efficient removal of the ground product is essential to maintain continuous operation and prevent re-grinding.
-
Additional Considerations:
- Residence Time: The time material spends in the mill chamber affects the degree of milling. Longer residence times can lead to finer grinding but may also increase energy consumption.
- Armor Surface Shape: The shape of the armor surface can influence the movement and impact of the grinding media, affecting the overall grinding performance.
By carefully considering and optimizing these factors, operators can enhance the performance and efficiency of ball mills, leading to better grinding outcomes and reduced operational costs.
Summary Table:
Category | Key Factors |
---|---|
Material Characteristics | Hardness, Density, Moisture Content |
Equipment Design | Drum Diameter, Length-to-Diameter Ratio, Grinding Media, Lining Material |
Operating Conditions | Rotation Speed, Filling Ratio, Feed Rate, Timely Removal of Ground Product |
Additional Considerations | Residence Time, Armor Surface Shape |
Optimize your ball mill performance today—contact our experts for a consultation!