Milling efficiency is influenced by a variety of factors, ranging from the physical properties of the materials being milled to the operational parameters of the milling equipment. Key factors include the size, type, and density of the grinding media (balls), the design and condition of the mill internals (such as liner profiles), and the operational settings like mill velocity, circulating load, and pulp density. Understanding and optimizing these factors can significantly enhance the efficiency of the milling process, leading to better performance and reduced operational costs.
Key Points Explained:
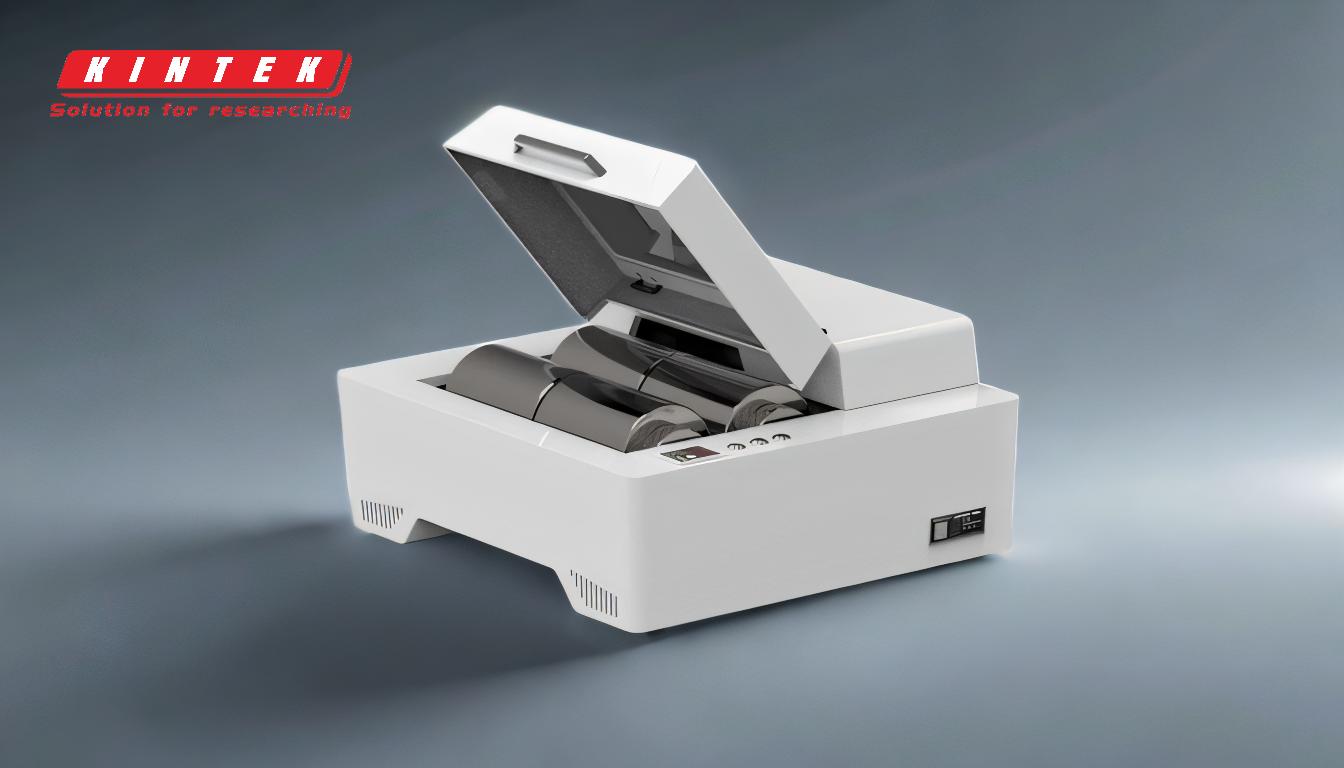
-
Ball Size, Type, and Density:
- Ball Size: The size of the grinding balls affects the energy transfer and the size reduction of the material. Larger balls can break down larger particles but may not be as effective for finer grinding. Conversely, smaller balls are better for fine grinding but may not efficiently break down larger particles.
- Type and Density: The material composition and density of the grinding balls influence their impact force and wear rate. Harder and denser balls can provide more effective grinding but may also increase wear on the mill liners.
-
Grinding Circuit Parameters:
- Circulating Load: This refers to the amount of material that is returned to the mill after being classified. A higher circulating load can increase the grinding efficiency by providing more opportunities for particle size reduction, but it also requires more energy and can lead to over-grinding.
- Pulp Density: The concentration of solids in the slurry affects the viscosity and flow characteristics. Optimal pulp density ensures efficient grinding by maintaining the right balance between the grinding media and the material being ground.
-
Mill Internals:
- Liner Profile: The design and condition of the mill liners play a crucial role in the grinding process. The liner profile affects the trajectory of the grinding media and the material, influencing the energy transfer and the efficiency of size reduction.
- Liner Material: The material of the liners affects their wear resistance and the overall durability of the mill. Choosing the right material can reduce maintenance costs and downtime.
-
Mill Operating Parameters:
- Velocity: The rotational speed of the mill determines the kinetic energy of the grinding media. Optimal velocity ensures that the grinding media cascade and impact the material effectively, leading to efficient size reduction.
- Percentage of Circulating Load: This parameter influences the residence time of the material in the mill and the overall grinding efficiency. Adjusting the circulating load can help achieve the desired particle size distribution.
- Pulp Density: Maintaining the right pulp density is crucial for efficient grinding. Too high or too low pulp density can negatively impact the grinding efficiency and the quality of the final product.
By carefully considering and optimizing these factors, operators can significantly improve the efficiency of their milling operations, leading to better product quality and reduced operational costs.
Summary Table:
Factor | Impact on Milling Efficiency |
---|---|
Ball Size | Larger balls for coarse grinding; smaller balls for fine grinding. |
Ball Type & Density | Harder, denser balls improve grinding but may increase liner wear. |
Circulating Load | Higher load increases efficiency but requires more energy and risks over-grinding. |
Pulp Density | Optimal density ensures efficient grinding by balancing media and material flow. |
Liner Profile | Affects grinding media trajectory and energy transfer for better size reduction. |
Liner Material | Durable materials reduce maintenance costs and downtime. |
Mill Velocity | Optimal speed ensures effective grinding media impact for efficient size reduction. |
Circulating Load % | Adjust to achieve desired particle size distribution and improve efficiency. |
Pulp Density Control | Maintain optimal levels to avoid negative impacts on grinding efficiency and product quality. |
Ready to optimize your milling process? Contact our experts today for tailored solutions!