The sintering process is a complex thermal treatment method used to bond particles into a solid mass, and its outcome is influenced by a variety of factors. These factors include the sintering atmosphere, temperature, cooling rate, applied pressure, particle size, composition, heating rate, and specific process parameters such as layer thickness, machine speed, and air volume. Each of these variables plays a critical role in determining the final properties of the sintered product, such as tensile strength, bending fatigue strength, and impact energy. Understanding and controlling these factors is essential for optimizing the sintering process to achieve desired material characteristics.
Key Points Explained:
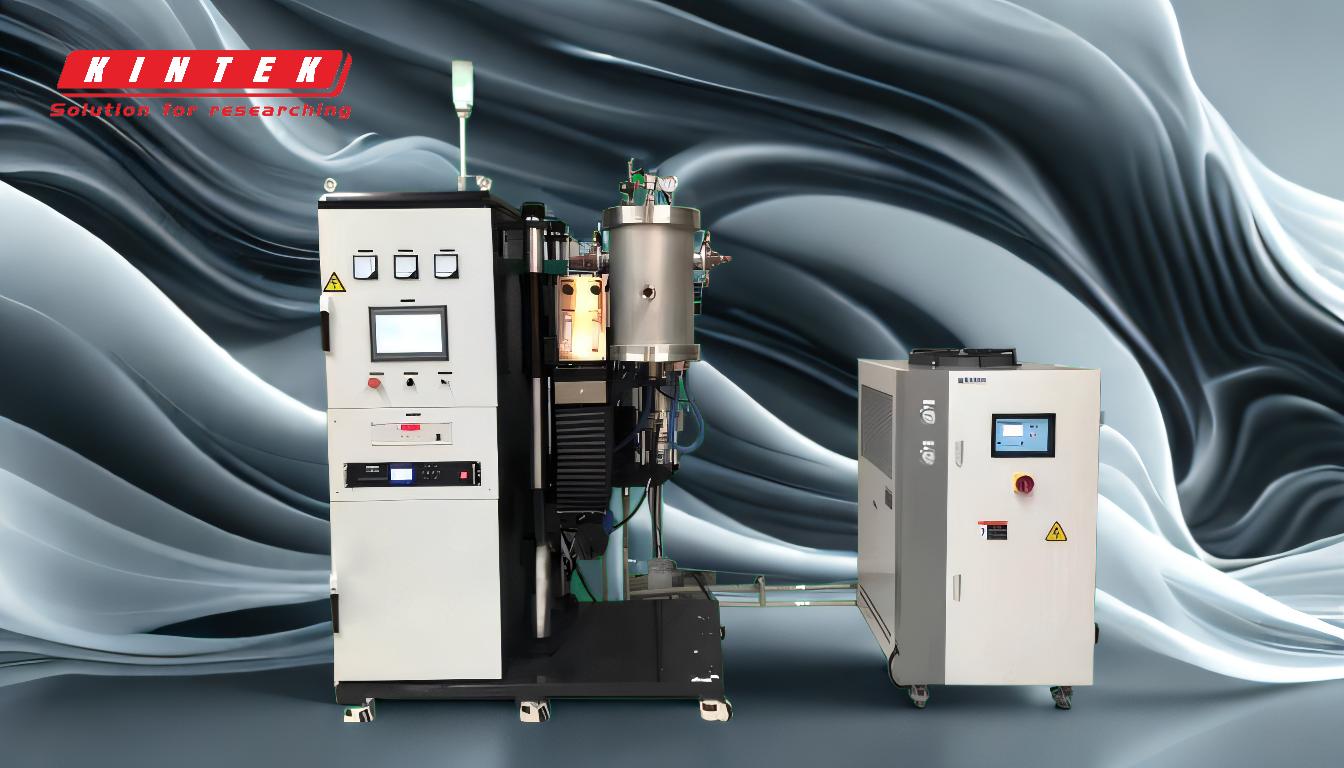
-
Sintering Atmosphere:
- The atmosphere in which sintering occurs (e.g., air, vacuum, argon, or nitrogen) significantly impacts the process. For instance, a vacuum or inert atmosphere can prevent oxidation and contamination, which is crucial for materials sensitive to oxygen or other reactive gases.
- The choice of atmosphere can also affect the sintering kinetics and the final properties of the material, such as density and mechanical strength.
-
Temperature:
- Temperature is one of the most critical factors in sintering. Higher temperatures generally increase the rate of diffusion, leading to better particle bonding and densification.
- However, excessively high temperatures can lead to undesirable grain growth or the formation of unwanted phases, which may degrade the material's properties.
- The optimal sintering temperature depends on the material being processed and the desired final properties.
-
Cooling Rate:
- The cooling rate after sintering can influence the microstructure and mechanical properties of the material. Rapid cooling may result in a finer grain structure, which can enhance strength and toughness.
- Conversely, slower cooling rates may allow for more controlled phase transformations, which can be beneficial for certain materials.
-
Applied Pressure:
- Pressure applied during sintering (as in hot pressing or spark plasma sintering) can enhance densification by promoting particle rearrangement and reducing porosity.
- The use of pressure can also allow for lower sintering temperatures, which can be advantageous for materials that are sensitive to high temperatures.
-
Particle Size and Composition:
- Smaller particle sizes generally lead to better densification because they have a higher surface area-to-volume ratio, which enhances diffusion and bonding.
- The composition of the particles, including the presence of additives or impurities, can also affect sintering behavior. Homogeneous compositions tend to promote more uniform densification.
-
Heating Rate:
- The rate at which the material is heated can influence the sintering process. A slower heating rate may allow for more uniform temperature distribution and reduce thermal stresses, while a faster heating rate can be beneficial for certain materials that require rapid densification.
-
Process Parameters:
- Specific process parameters such as layer thickness, machine speed, air volume, and vacuum level are critical in industrial sintering processes. For example, the layer thickness (typically 250-500mm) and machine speed (1.5-4m/min) must be carefully controlled to ensure that the sintering feed is burned at the scheduled endpoint.
- The air volume (typically 3200m³ per ton of sintering ore) and vacuum level are also important, as they affect the efficiency of the sintering process and the quality of the final product.
-
Sintering Endpoint Control:
- The endpoint of the sintering process must be carefully controlled to ensure that the material reaches the desired level of densification without over-sintering, which can lead to defects or reduced mechanical properties.
- Factors such as the sintering area (calculated as 70-90 m³/(cm²·min)) and the fan capacity, air resistance, air permeability, and wind leakage loss all play a role in determining the optimal sintering endpoint.
In summary, the sintering process is governed by a complex interplay of factors, each of which must be carefully controlled to achieve the desired material properties. By understanding and optimizing these factors, manufacturers can produce high-quality sintered products with tailored mechanical and physical properties.
Summary Table:
Factor | Impact on Sintering Process |
---|---|
Sintering Atmosphere | Affects oxidation, contamination, and final material properties (e.g., density, strength). |
Temperature | Higher temps improve diffusion and bonding; excessive temps may cause grain growth or defects. |
Cooling Rate | Influences microstructure; rapid cooling enhances strength, slower cooling aids phase control. |
Applied Pressure | Enhances densification, reduces porosity, and allows lower sintering temps. |
Particle Size | Smaller particles improve densification due to higher surface area-to-volume ratio. |
Composition | Homogeneous compositions promote uniform densification. |
Heating Rate | Affects temperature distribution and thermal stresses; slower rates reduce stress. |
Process Parameters | Layer thickness, machine speed, air volume, and vacuum level impact efficiency and quality. |
Endpoint Control | Ensures optimal densification without defects or reduced mechanical properties. |
Ready to optimize your sintering process? Contact our experts today for tailored solutions!