Biochar production relies on a variety of feedstocks, primarily derived from organic materials such as wood, agricultural residues, green waste, and algae. These feedstocks are chosen based on their availability, cost, and suitability for the pyrolysis process. Common sources include pine wood, wheat straw, green waste, and dried algae, as well as other biomass like agricultural residues (e.g., sugarcane bagasse, rice straw, cotton stalks), municipal solid waste, and invasive species. The choice of feedstock depends on factors such as composition, regional availability, and the intended application of the biochar.
Key Points Explained:
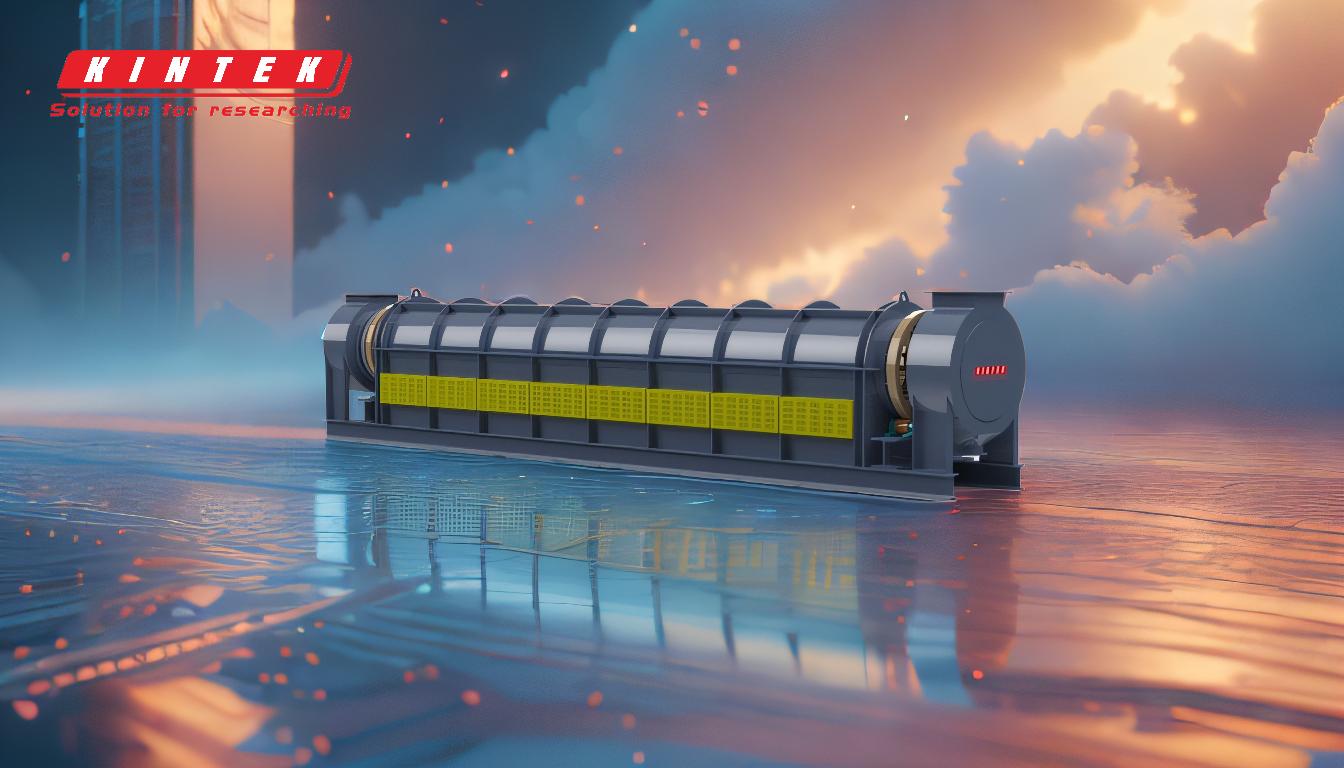
-
Primary Feedstocks for Biochar Production:
- Wood: Pine wood and other wood waste from sawmills, construction, and forest residues are widely used due to their high carbon content and availability.
- Agricultural Residues: Wheat straw, rice straw, sugarcane bagasse, and cotton stalks are common agricultural byproducts used in biochar production.
- Green Waste: Yard waste, municipal green waste, and other organic waste materials are increasingly being utilized.
- Algae: Dried algae is another feedstock, particularly in regions where algae farming is prevalent.
-
Secondary and Alternative Feedstocks:
- Municipal Solid Waste: Organic components of municipal waste can be processed into biochar, offering a sustainable waste management solution.
- Invasive Species: Biomass from invasive plants like phragmites and kudzu is being explored as a feedstock, helping to control these species while producing biochar.
- Energy Crops: Crops specifically grown for energy production, such as switchgrass, can also serve as feedstock.
-
Factors Influencing Feedstock Selection:
- Composition: The chemical composition of the feedstock, including lignin, cellulose, and hemicellulose content, affects the quality and yield of biochar.
- Availability: Regional availability of feedstocks plays a significant role in determining their use.
- Cost: Economic considerations often dictate the choice of feedstock, with cheaper and more abundant materials being preferred.
-
Applications and Suitability:
- Second-Generation Biofuels: Feedstocks like forest residues, agricultural waste, and energy crops are particularly suitable for second-generation biofuel applications.
- Environmental Benefits: Using waste materials and invasive species as feedstocks not only produces biochar but also addresses environmental issues like waste management and invasive species control.
-
Emerging Trends:
- Algae-Based Biochar: The use of algae as a feedstock is gaining traction due to its high growth rate and potential for carbon sequestration.
- Waste-to-Energy: The integration of biochar production with waste-to-energy initiatives is becoming more common, promoting a circular economy.
By understanding these key points, purchasers and producers can make informed decisions about the most suitable feedstocks for their biochar production needs, balancing cost, availability, and environmental impact.
Summary Table:
Feedstock Type | Examples | Key Benefits |
---|---|---|
Primary Feedstocks | Pine wood, wheat straw, green waste, dried algae | High carbon content, abundant availability, suitable for pyrolysis |
Secondary Feedstocks | Municipal solid waste, invasive species (e.g., phragmites, kudzu), switchgrass | Sustainable waste management, invasive species control, energy crop suitability |
Factors to Consider | Composition (lignin, cellulose), regional availability, cost | Influences biochar quality, yield, and economic feasibility |
Ready to choose the best feedstock for your biochar production? Contact our experts today for tailored advice!