The synthesis of nanoparticles, particularly aluminium nanoparticles, involves overcoming several challenges such as achieving high yield, purity, and controlling agglomeration. The method of synthesis plays a crucial role in determining these properties. Here, we explore five primary methods of nanoparticle synthesis, focusing on their principles, advantages, and limitations.
Key Points Explained:
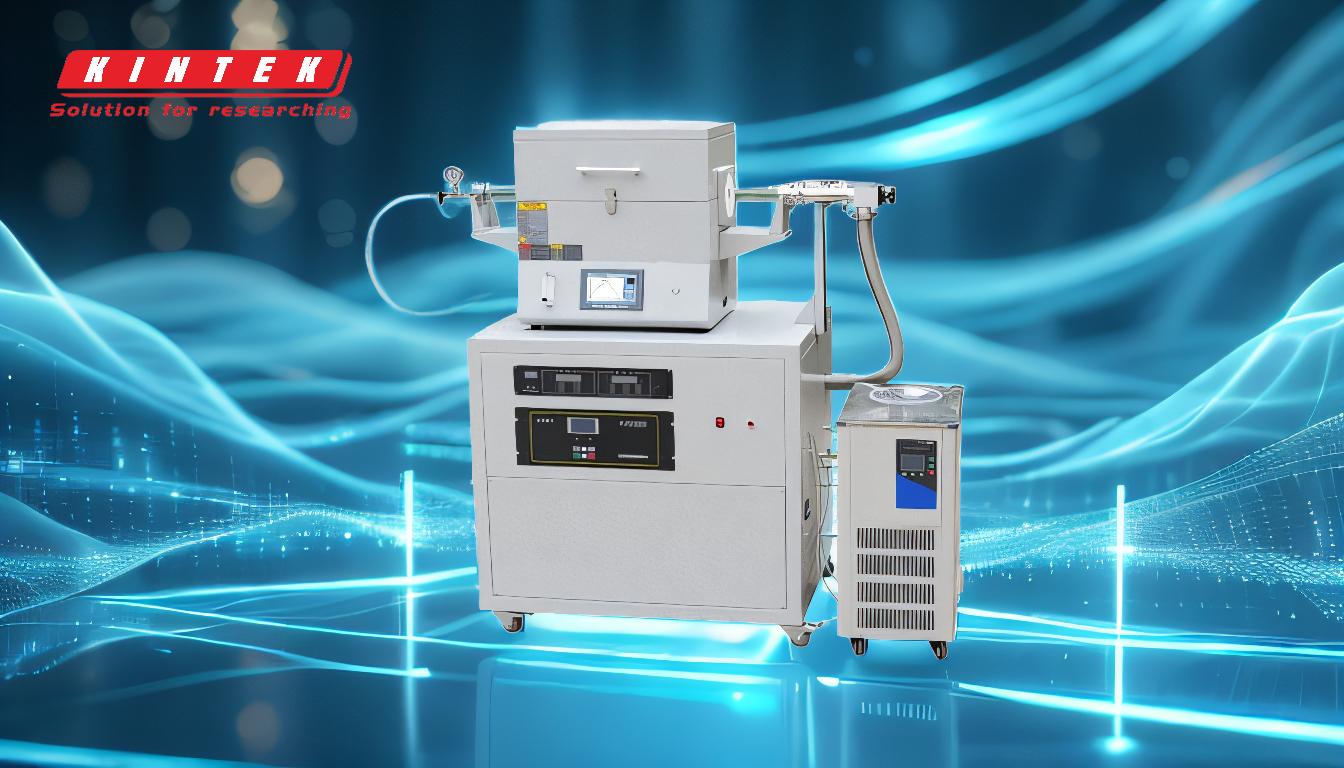
-
Chemical Reduction Method:
- Principle: This method involves the reduction of metal salts in a solution using reducing agents like sodium borohydride or hydrazine.
- Advantages: It is relatively simple and cost-effective. It allows for the production of nanoparticles with controlled size and shape.
- Limitations: The use of toxic reducing agents and the need for post-synthesis purification to remove unreacted chemicals and by-products.
-
Physical Vapor Deposition (PVD):
- Principle: PVD involves the vaporization of a solid material in a vacuum, followed by its deposition onto a substrate to form nanoparticles.
- Advantages: Produces high-purity nanoparticles with minimal contamination. Suitable for creating thin films and coatings.
- Limitations: Requires sophisticated equipment and is generally more expensive. The process can be slow and is limited by the types of materials that can be vaporized.
-
Green Synthesis:
- Principle: Utilizes biological materials such as plant extracts, bacteria, or fungi to reduce metal ions into nanoparticles.
- Advantages: Environmentally friendly and sustainable. It avoids the use of toxic chemicals and can produce nanoparticles with unique biological properties.
- Limitations: The yield and size control can be less predictable compared to chemical methods. The process may also be slower.
-
Sol-Gel Method:
- Principle: Involves the transformation of a solution (sol) into a gel, which is then dried and calcined to form nanoparticles.
- Advantages: Allows for the synthesis of nanoparticles with high purity and homogeneity. It is versatile and can be used to produce a wide range of materials.
- Limitations: The process can be time-consuming and requires careful control of conditions to avoid defects. The calcination step can also lead to particle agglomeration.
-
Mechanical Milling:
- Principle: Involves the grinding of bulk materials into nanoparticles using high-energy ball mills.
- Advantages: Simple and scalable. It can be used to produce a wide range of nanoparticle materials.
- Limitations: Can introduce impurities from the milling media. The process may also result in a broad size distribution and significant agglomeration.
Each of these methods has its own set of challenges and benefits, and the choice of method depends on the specific requirements of the nanoparticles being synthesized, such as desired size, purity, and application. For instance, the chemical reduction method might be preferred for its simplicity and cost-effectiveness, while PVD might be chosen for applications requiring high purity and thin film formation. Green synthesis offers an eco-friendly alternative, though it may come with trade-offs in terms of yield and control. The sol-gel method and mechanical milling provide additional options, each with its own unique advantages and limitations.
Summary Table:
Method | Principle | Advantages | Limitations |
---|---|---|---|
Chemical Reduction | Reduction of metal salts using reducing agents like sodium borohydride. | Simple, cost-effective, controlled size and shape. | Toxic reducing agents, requires post-synthesis purification. |
Physical Vapor Deposition (PVD) | Vaporization of solid material in vacuum, deposition onto substrate. | High purity, minimal contamination, suitable for thin films. | Expensive, slow, limited material types. |
Green Synthesis | Uses biological materials like plant extracts, bacteria, or fungi. | Eco-friendly, avoids toxic chemicals, unique biological properties. | Less predictable yield and size control, slower process. |
Sol-Gel Method | Transformation of sol into gel, dried and calcined to form nanoparticles. | High purity, homogeneity, versatile for various materials. | Time-consuming, requires careful control, potential agglomeration. |
Mechanical Milling | Grinding bulk materials into nanoparticles using high-energy ball mills. | Simple, scalable, produces wide range of materials. | Introduces impurities, broad size distribution, significant agglomeration. |
Need help choosing the right nanoparticle synthesis method for your project? Contact our experts today!