Electron-beam welding (EBW) is a highly precise and efficient welding technique that has been widely adopted in various industries since the 1950s. It utilizes a focused beam of high-velocity electrons to generate intense heat, enabling the welding of materials with exceptional precision and minimal distortion. This method is particularly advantageous for applications requiring deep, narrow welds, high-quality joints, and the ability to weld refractory or dissimilar materials. Industrial applications of EBW span across aerospace, automotive, medical, energy, and semiconductor sectors, where its unique capabilities are leveraged to meet stringent performance and quality requirements.
Key Points Explained:
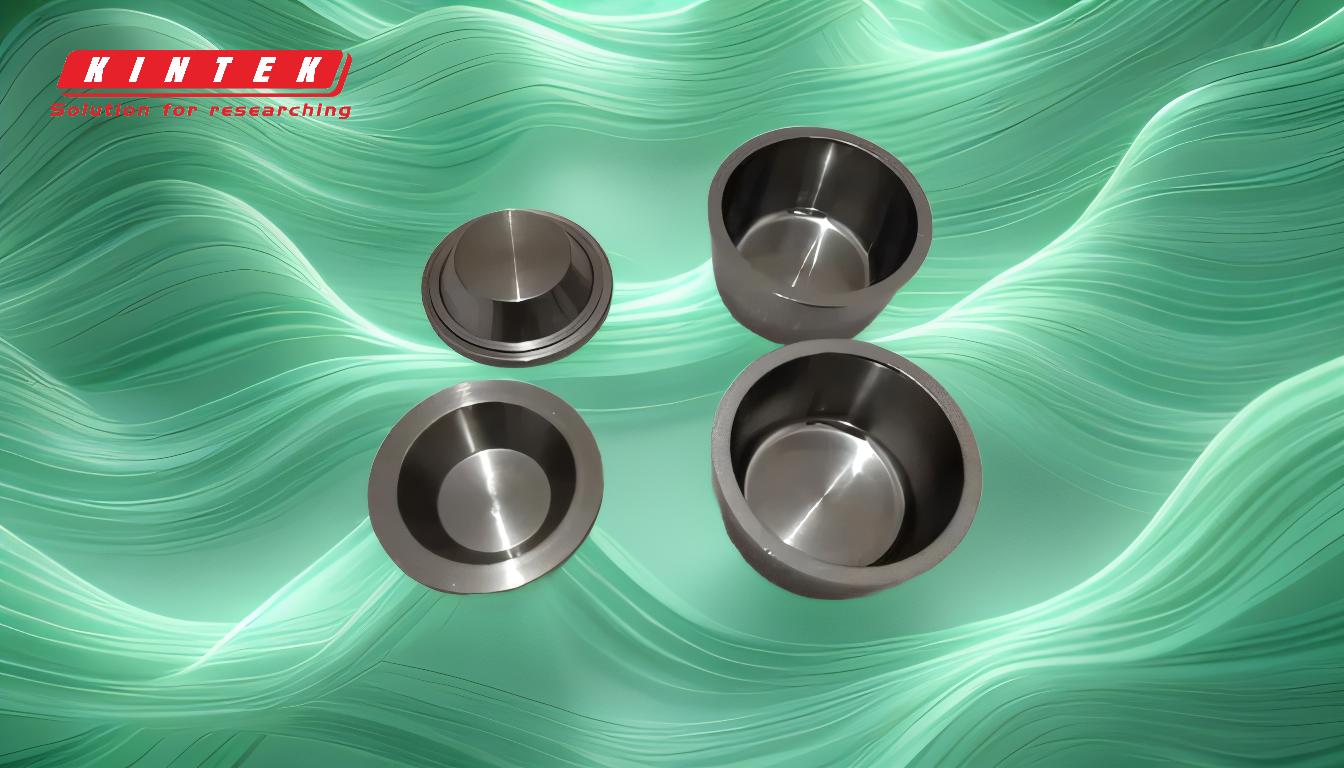
-
Aerospace Industry:
- Deep and Narrow Welds: EBW is ideal for aerospace components, such as turbine blades, engine components, and structural parts, where deep, narrow welds are required to maintain structural integrity without adding excessive weight.
- High-Strength Materials: The ability to weld refractory materials like titanium and nickel-based superalloys makes EBW indispensable in aerospace manufacturing, where these materials are commonly used for their strength and heat resistance.
- Precision and Repeatability: The high precision of EBW ensures consistent weld quality, which is critical for aerospace applications where safety and reliability are paramount.
-
Automotive Industry:
- Lightweight Components: EBW is used to join lightweight materials such as aluminum and magnesium alloys, contributing to the production of fuel-efficient vehicles.
- High-Speed Production: The rapid heating and cooling cycles of EBW enable high-speed production, making it suitable for mass manufacturing of automotive parts like gears, shafts, and transmission components.
- Dissimilar Material Joining: EBW is effective in joining dissimilar materials, such as steel and aluminum, which is increasingly important in modern vehicle design for optimizing performance and reducing weight.
-
Medical Industry:
- Biocompatible Materials: EBW is used to weld biocompatible materials like titanium and stainless steel, which are commonly used in medical implants and surgical instruments.
- Clean and Contamination-Free Welds: The vacuum environment of EBW prevents contamination, ensuring that medical devices meet strict hygiene and quality standards.
- Miniaturization: EBW's precision is particularly valuable in the production of small, intricate medical devices, such as pacemakers and stents.
-
Energy Industry:
- Nuclear Components: EBW is employed in the fabrication of nuclear reactor components, where the ability to produce high-integrity welds in radioactive environments is crucial.
- Renewable Energy: In the solar panel industry, EBW is used for joining thin films and other components, contributing to the production of efficient and durable solar cells.
- High-Temperature Applications: EBW is suitable for welding materials used in high-temperature environments, such as those found in power generation and oil and gas industries.
-
Semiconductor and Electronics Industry:
- Microelectronics: EBW is used in the fabrication of microelectronic components, where precision and minimal heat-affected zones are critical.
- Hermetic Sealing: The technique is employed for hermetic sealing of electronic packages, ensuring long-term reliability and protection from environmental factors.
- Advanced Materials: EBW is utilized in the production of advanced materials, such as liquid-crystal films and polymers, which are essential in modern electronics.
-
Tool and Die Industry:
- Durable Coatings: EBW is used to apply dense and strong coatings on cutting tools, enhancing their durability and performance.
- Wear-Resistant Components: The technique is employed to produce wear-resistant components, which are essential in high-stress industrial applications.
-
Research and Development:
- Material Development: EBW is used in R&D for developing new materials and testing their weldability under extreme conditions.
- Prototyping: The precision and flexibility of EBW make it an excellent tool for prototyping new components and assemblies in various industries.
In summary, electron-beam welding is a versatile and powerful technology that plays a critical role in numerous industrial applications. Its ability to produce high-quality, precise welds in a wide range of materials and environments makes it an invaluable tool in modern manufacturing and engineering.
Summary Table:
Industry | Key Applications |
---|---|
Aerospace | Deep, narrow welds; high-strength materials; precision and repeatability |
Automotive | Lightweight components; high-speed production; dissimilar material joining |
Medical | Biocompatible materials; contamination-free welds; miniaturization |
Energy | Nuclear components; renewable energy; high-temperature applications |
Semiconductor | Microelectronics; hermetic sealing; advanced materials |
Tool and Die | Durable coatings; wear-resistant components |
R&D | Material development; prototyping |
Explore how electron-beam welding can revolutionize your manufacturing process—contact us today!