Graphite furnace atomic absorption spectroscopy (GFAAS) is a highly sensitive analytical technique used for trace metal analysis. However, it is susceptible to various interferences that can affect the accuracy and precision of results. These interferences can be broadly categorized into spectral, chemical, and physical interferences. Spectral interferences arise from overlapping absorption lines or background absorption, while chemical interferences involve interactions between the analyte and matrix components that alter the atomization process. Physical interferences are related to changes in the sample introduction or atomization conditions. Understanding and mitigating these interferences is crucial for obtaining reliable analytical results.
Key Points Explained:
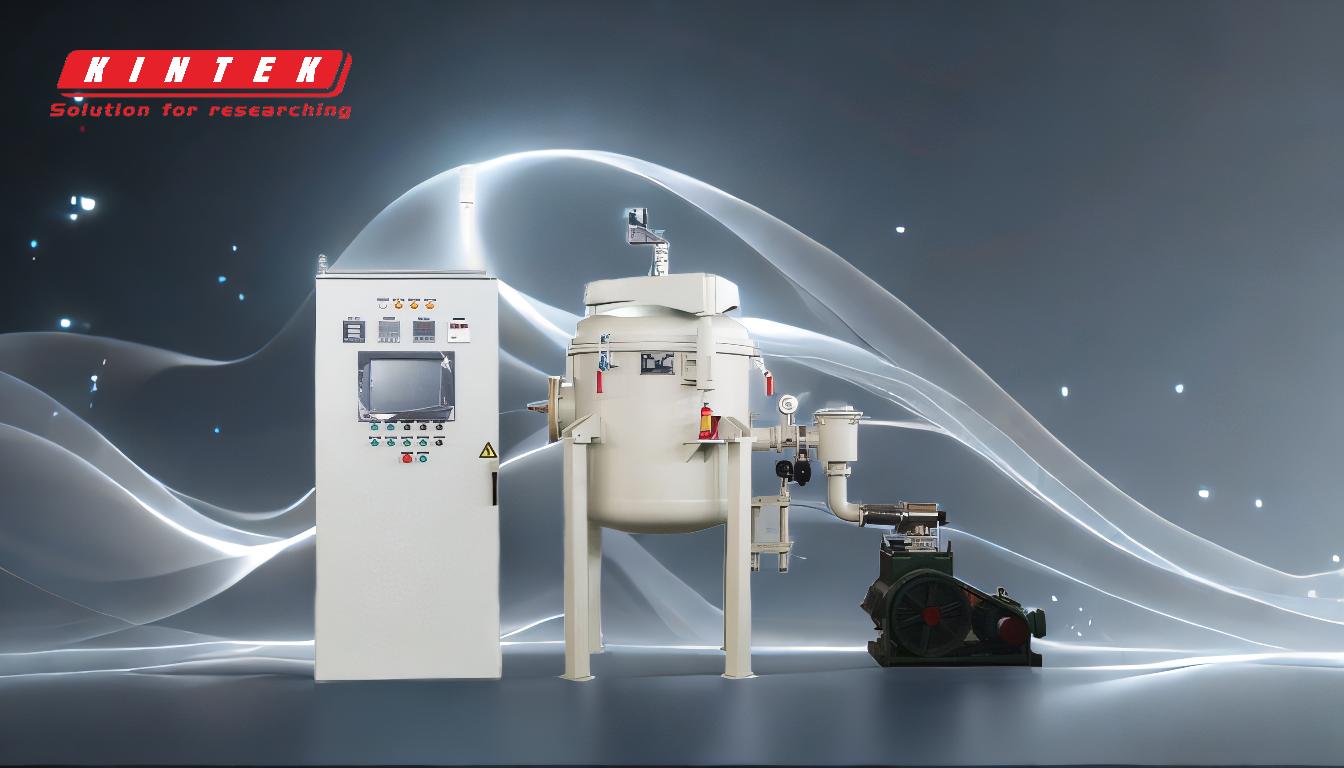
-
Spectral Interferences:
- Overlapping Absorption Lines: When the absorption lines of the analyte and another element overlap, it can lead to false readings. This is particularly problematic in complex matrices where multiple elements are present.
- Background Absorption: Non-specific absorption by matrix components or molecular species can obscure the analyte signal. This is often corrected using background correction techniques such as deuterium lamp or Zeeman-effect background correction.
-
Chemical Interferences:
- Matrix Effects: The presence of other elements or compounds in the sample can alter the atomization efficiency of the analyte. For example, high concentrations of salts or organic matter can suppress or enhance the analyte signal.
- Formation of Stable Compounds: Some analytes may form stable compounds with matrix components that do not easily decompose during atomization, leading to reduced sensitivity. This is often mitigated by using chemical modifiers that promote the release of the analyte.
- Volatilization Interferences: Differences in the volatility of the analyte and matrix components can lead to incomplete or inconsistent atomization. This can be addressed by optimizing the temperature program of the graphite furnace.
-
Physical Interferences:
- Sample Introduction Variability: Inconsistent sample introduction, such as variations in droplet size or deposition position, can lead to variability in the atomization process. Automated sample introduction systems can help reduce this variability.
- Graphite Tube Degradation: Over time, the graphite tube can degrade due to repeated heating cycles, leading to changes in the atomization characteristics. Regular maintenance and replacement of the graphite tube are necessary to maintain consistent performance.
- Temperature Gradients: Non-uniform heating of the graphite tube can result in uneven atomization, affecting the reproducibility of results. Ensuring proper alignment and calibration of the furnace can help mitigate this issue.
-
Mitigation Strategies:
- Use of Chemical Modifiers: Adding chemical modifiers to the sample can help stabilize the analyte and reduce matrix effects. Common modifiers include palladium, magnesium nitrate, and ammonium phosphate.
- Background Correction Techniques: Implementing background correction methods such as deuterium lamp or Zeeman-effect correction can help distinguish between analyte and background absorption.
- Optimization of Furnace Parameters: Carefully optimizing the temperature program, gas flow rates, and other furnace parameters can help minimize interferences and improve the accuracy of the analysis.
- Matrix Matching and Standard Additions: Using matrix-matched standards or the standard additions method can help account for matrix effects and improve the accuracy of the results.
In conclusion, while graphite furnace atomic absorption spectroscopy is a powerful tool for trace metal analysis, it is susceptible to various interferences that can affect the accuracy and precision of the results. Understanding these interferences and implementing appropriate mitigation strategies is essential for obtaining reliable analytical data.
Summary Table:
Interference Type | Key Causes | Mitigation Strategies |
---|---|---|
Spectral | Overlapping absorption lines, background absorption | Use background correction techniques (deuterium lamp, Zeeman-effect) |
Chemical | Matrix effects, formation of stable compounds, volatilization issues | Add chemical modifiers, optimize furnace temperature program |
Physical | Sample introduction variability, graphite tube degradation, temperature gradients | Use automated sample systems, maintain/replace graphite tubes, ensure proper furnace alignment |
Need help optimizing your GFAAS analysis? Contact our experts today for tailored solutions!