Silicon carbide (SiC) is a versatile material with exceptional properties such as high hardness, thermal conductivity, wear resistance, and chemical stability, making it ideal for applications in corrosive environments, high-temperature settings, and semiconductor manufacturing. However, despite its advantages, silicon carbide has several limitations that can affect its performance and suitability for certain applications. These limitations include challenges in manufacturing, brittleness, high production costs, and limited electrical conductivity in some forms. Understanding these constraints is crucial for equipment and consumable purchasers to make informed decisions.
Key Points Explained:
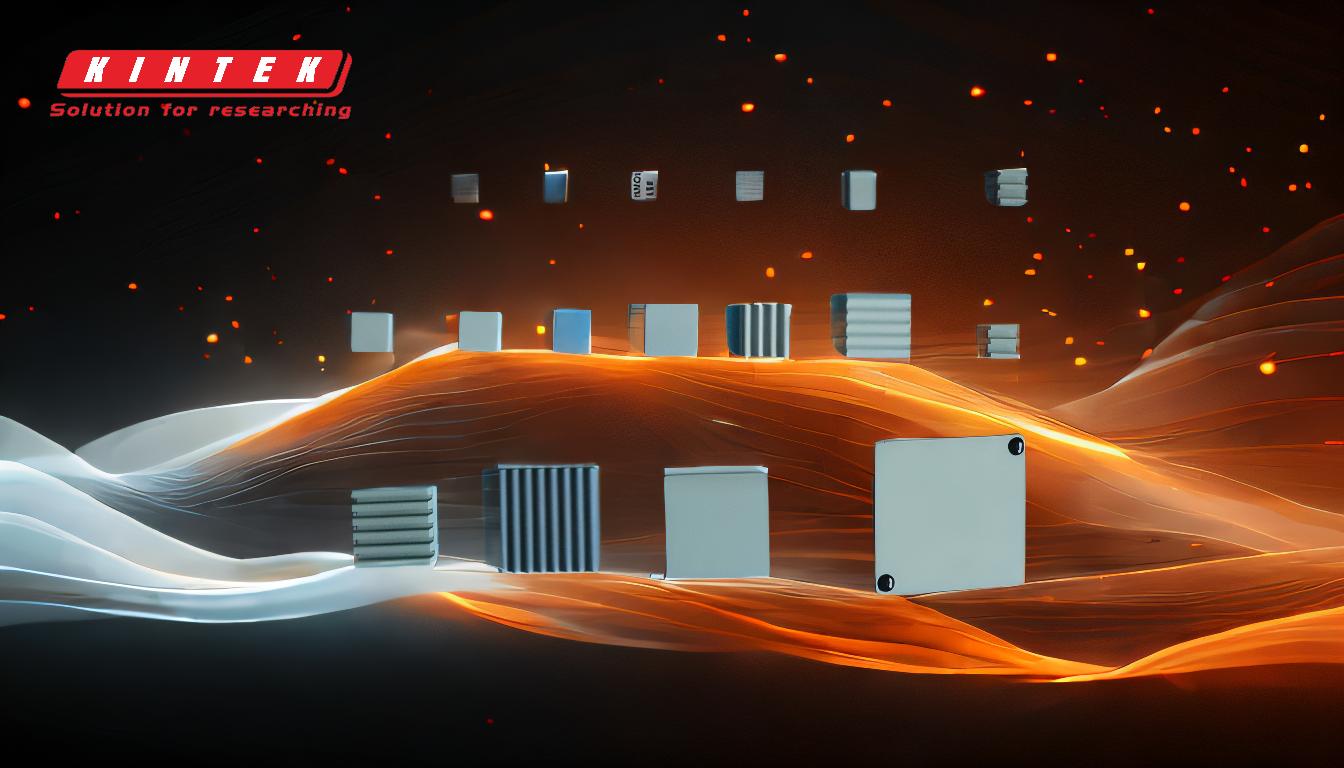
-
Brittleness and Mechanical Limitations:
- Silicon carbide is inherently brittle, which makes it prone to cracking or fracturing under mechanical stress or impact. This limits its use in applications requiring high toughness or flexibility.
- While it has high hardness and wear resistance, its brittleness can be a drawback in dynamic or high-impact environments, such as certain industrial machinery or structural components.
-
Manufacturing Complexity:
- Producing high-quality silicon carbide ceramic requires advanced manufacturing techniques, such as sintering or chemical vapor deposition (CVD). These processes are energy-intensive and require precise control over temperature and pressure, leading to higher production costs.
- The complexity of manufacturing also limits the size and shape of components that can be produced, making it challenging to create large or intricately designed parts.
-
High Production Costs:
- The raw materials and processing methods for silicon carbide are expensive compared to other ceramics or metals. This cost factor can be a significant limitation for industries with tight budgets or high-volume production requirements.
- The need for specialized equipment and skilled labor further adds to the overall expense, making it less economical for some applications.
-
Limited Electrical Conductivity in Some Forms:
- While silicon carbide is used as a semiconductor material due to its wide band gap and high thermal conductivity, its electrical conductivity can vary depending on its purity and crystal structure. In some cases, it may not provide the desired electrical performance for certain electronic applications.
- This limitation can restrict its use in advanced semiconductor devices where precise control over electrical properties is critical.
-
Thermal Shock Sensitivity:
- Although silicon carbide has excellent thermal conductivity and can withstand high temperatures, it is susceptible to thermal shock. Rapid temperature changes can cause cracking or failure, particularly in large or thick components.
- This sensitivity limits its use in applications where rapid heating or cooling cycles are common, such as in certain industrial furnaces or aerospace components.
-
Corrosion Resistance Limitations:
- While silicon carbide is highly resistant to many corrosive environments, it can be attacked by certain chemicals, such as hydrofluoric acid and strong alkalis. This restricts its use in applications involving these substances.
- In highly oxidizing environments at elevated temperatures, silicon carbide can also undergo oxidation, forming a silica layer that may affect its performance over time.
-
Limited Availability of High-Quality Raw Materials:
- The production of high-performance silicon carbide requires high-purity raw materials, which are not always readily available. This can lead to supply chain challenges and increased costs.
- The availability of suitable raw materials can also impact the consistency and quality of the final product, affecting its suitability for critical applications.
-
Challenges in Joining and Machining:
- Silicon carbide is difficult to machine due to its extreme hardness, requiring specialized tools and techniques. This increases the cost and time required for post-processing.
- Joining silicon carbide components to other materials (e.g., metals or other ceramics) is also challenging, often requiring advanced bonding techniques that may not be cost-effective or reliable.
In conclusion, while silicon carbide ceramic offers numerous advantages, its limitations—such as brittleness, high production costs, and sensitivity to thermal shock—must be carefully considered when selecting materials for specific applications. Equipment and consumable purchasers should weigh these factors against the material's benefits to determine its suitability for their needs. For more information on silicon carbide ceramics, visit silicon carbide ceramic.
Summary Table:
Limitation | Description |
---|---|
Brittleness | Prone to cracking under mechanical stress, limiting use in high-impact environments. |
Manufacturing Complexity | Requires advanced, energy-intensive processes, increasing costs and limiting size/shape options. |
High Production Costs | Expensive raw materials and specialized equipment make it less economical for some applications. |
Limited Electrical Conductivity | Variability in conductivity can restrict use in advanced semiconductor devices. |
Thermal Shock Sensitivity | Susceptible to cracking under rapid temperature changes. |
Corrosion Resistance Limitations | Vulnerable to certain chemicals and oxidation in extreme conditions. |
Limited Raw Material Availability | High-purity raw materials are scarce, impacting supply and quality consistency. |
Joining and Machining Challenges | Difficult to machine and join, requiring specialized techniques and tools. |
Need help selecting the right material for your application? Contact us today for expert guidance!