Chemical vapor deposition (CVD) equipment is a sophisticated system designed to deposit thin films on substrates through chemical reactions in the vapor phase. The primary components of CVD equipment include a reaction chamber, gas delivery system, heating system, vacuum system, and exhaust system. These components work together to ensure precise control over the deposition process, enabling the creation of high-performance thin films used in various industries such as semiconductors, optics, and coatings. The equipment is categorized based on end-user applications, including memory, foundry, and logic segments, each requiring specific configurations to meet their unique needs.
Key Points Explained:
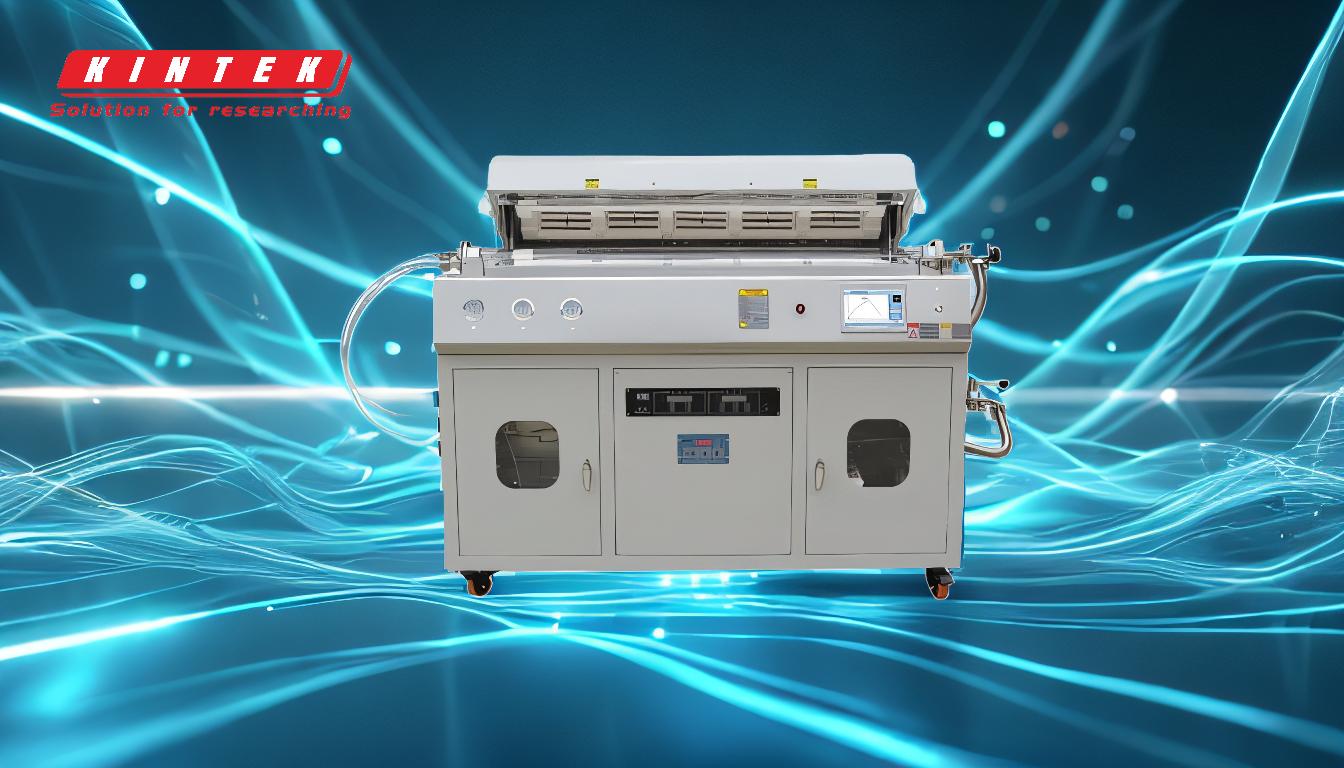
-
Reaction Chamber:
- The reaction chamber is the core component where the deposition process occurs. It is designed to withstand high temperatures and corrosive environments, ensuring the integrity of the deposition process.
- The chamber must maintain a controlled atmosphere to facilitate the chemical reactions necessary for thin-film formation. This includes precise control over pressure and temperature to achieve uniform deposition.
-
Gas Delivery System:
- The gas delivery system is responsible for supplying the precursor gases and other reactive gases to the reaction chamber. It includes gas cylinders, mass flow controllers, and valves to regulate the flow of gases.
- Precise control over the gas flow rates is crucial for achieving the desired film properties, such as thickness, composition, and uniformity.
-
Heating System:
- The heating system provides the thermal energy required to vaporize the precursor compounds and facilitate the chemical reactions. This system typically includes resistive heaters, induction coils, or lamps.
- The heating system must ensure uniform temperature distribution across the substrate to prevent defects in the deposited film.
-
Vacuum System:
- The vacuum system is essential for creating and maintaining the low-pressure environment required for CVD processes. It includes vacuum pumps, pressure gauges, and valves.
- A well-maintained vacuum system ensures the removal of any contaminants and provides a stable environment for the deposition process.
-
Exhaust System:
- The exhaust system is responsible for removing by-products and unreacted gases from the reaction chamber. It includes scrubbers, filters, and exhaust pumps.
- Proper exhaust management is crucial for maintaining the purity of the deposition environment and ensuring the safety of the operation.
-
Control and Monitoring System:
- Modern CVD equipment often includes advanced control and monitoring systems to automate and optimize the deposition process. These systems use sensors and software to monitor parameters such as temperature, pressure, and gas flow rates.
- Real-time monitoring and control enhance the reproducibility and quality of the deposited films.
-
Substrate Handling System:
- The substrate handling system is designed to load, position, and unload the substrates within the reaction chamber. It includes robotic arms, trays, and holders.
- Efficient substrate handling ensures minimal contamination and maximizes throughput in high-volume production environments.
-
End-User Specific Configurations:
- CVD equipment is tailored to meet the specific requirements of different end-user segments, such as memory, foundry, and logic. For example, memory applications may require equipment optimized for high-throughput deposition of dielectric layers, while logic applications may focus on precision deposition of conductive layers.
- The equipment's design and configuration are influenced by the specific materials and processes used in each segment.
In summary, the main components of CVD equipment are designed to work in harmony to achieve precise and controlled deposition of thin films. Each component plays a critical role in ensuring the quality, uniformity, and performance of the deposited films, making CVD equipment indispensable in various high-tech industries.
Summary Table:
Component | Function | Key Features |
---|---|---|
Reaction Chamber | Core component where deposition occurs | High-temperature resistance, controlled atmosphere for uniform deposition |
Gas Delivery System | Supplies precursor and reactive gases | Mass flow controllers, precise gas flow regulation |
Heating System | Provides thermal energy for vaporization and reactions | Uniform temperature distribution, resistive heaters or induction coils |
Vacuum System | Maintains low-pressure environment | Vacuum pumps, pressure gauges, contaminant removal |
Exhaust System | Removes by-products and unreacted gases | Scrubbers, filters, exhaust pumps for safety and purity |
Control & Monitoring | Automates and optimizes deposition process | Sensors, software for real-time parameter monitoring |
Substrate Handling | Loads, positions, and unloads substrates | Robotic arms, trays, and holders for minimal contamination |
End-User Configurations | Tailored for specific applications (e.g., memory, foundry, logic) | Optimized for high-throughput or precision deposition based on industry needs |
Need CVD equipment tailored to your industry? Contact our experts today for a customized solution!