Deposition in nanotechnology involves creating thin films or nanostructures on substrates, and it is a critical process in fabricating nanoscale devices. The methods can be broadly categorized into physical vapor deposition (PVD), chemical vapor deposition (CVD), and other advanced techniques like atomic layer deposition (ALD). Each method has unique advantages, such as high purity, precise control over thickness, and compatibility with various materials. The choice of deposition method depends on the desired film properties, substrate type, and application requirements.
Key Points Explained:
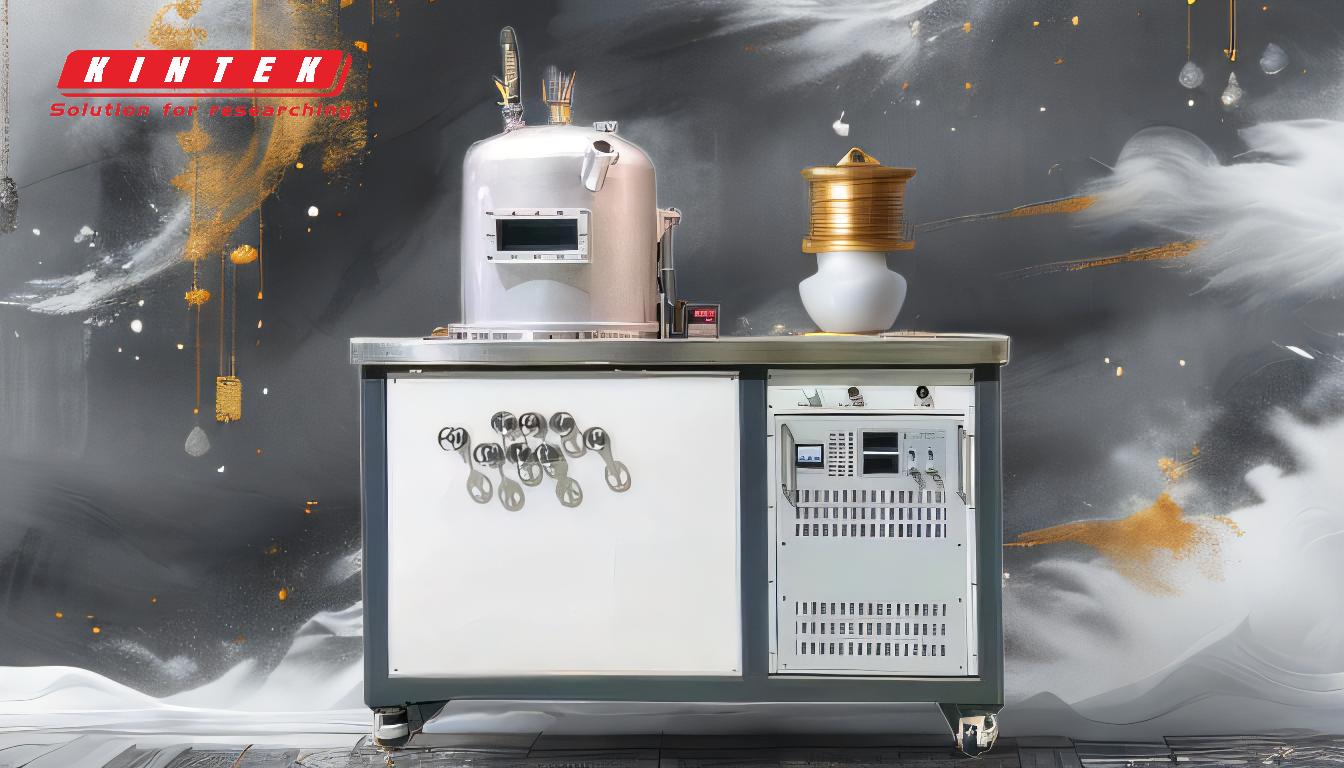
-
Physical Vapor Deposition (PVD):
- Definition: PVD involves the physical transfer of material from a source to a substrate in a vacuum environment.
-
Common Techniques:
- Magnetron Sputtering: Uses a plasma to eject atoms from a target material, which then deposit onto the substrate. Known for producing high-purity, defect-free coatings.
- Electron Beam Evaporation: A high-energy electron beam heats a target material, causing it to evaporate and condense on the substrate.
- Ion Beam Sputtering: Similar to magnetron sputtering but uses a focused ion beam to sputter material onto the substrate.
- Advantages: High-quality films, good adhesion, and compatibility with a wide range of materials.
-
Chemical Vapor Deposition (CVD):
- Definition: CVD involves chemical reactions in the gas phase to produce a solid material that deposits onto the substrate.
-
Common Techniques:
- Low Pressure CVD (LPCVD): Conducted at reduced pressures to improve film uniformity and reduce impurities.
- Plasma Enhanced CVD (PECVD): Uses plasma to enhance chemical reactions, allowing deposition at lower temperatures.
- Atomic Layer Deposition (ALD): A precise form of CVD where materials are deposited one atomic layer at a time, offering exceptional control over film thickness and composition.
- Advantages: High-quality, uniform films with excellent step coverage and the ability to deposit complex materials.
-
Other Deposition Methods:
- Epitaxial Deposition (Epi): Used to grow crystalline layers on a substrate, often for semiconductor applications.
- Diamond-Like Carbon (DLC): A specialized form of PVD or CVD used to deposit hard, wear-resistant carbon films.
- Dip or Spin Coating: Simpler methods where a liquid precursor is applied to the substrate and then solidified, but these are less precise than PVD or CVD.
-
Bottom-Up vs. Top-Down Approaches:
- Bottom-Up: Builds nanostructures atom by atom or molecule by molecule, often using techniques like ALD or CVD.
- Top-Down: Starts with a larger material and reduces it to nanoscale dimensions using methods like lithography or etching.
-
Application Considerations:
- Material Compatibility: The choice of deposition method depends on the material being deposited and the substrate.
- Film Properties: Factors like thickness, uniformity, and purity are critical and vary by method.
- Cost and Scalability: Some methods, like ALD, are highly precise but may be more expensive or slower than others like PVD.
In summary, nanotechnology deposition methods are diverse, each offering unique benefits for specific applications. PVD and CVD are the most widely used, with techniques like magnetron sputtering, ALD, and PECVD being particularly notable for their precision and quality. The choice of method depends on the desired film properties, material compatibility, and application requirements.
Summary Table:
Method | Key Techniques | Advantages |
---|---|---|
Physical Vapor Deposition (PVD) | Magnetron Sputtering, Electron Beam Evaporation, Ion Beam Sputtering | High-quality films, good adhesion, wide material compatibility |
Chemical Vapor Deposition (CVD) | LPCVD, PECVD, ALD | High-quality, uniform films, excellent step coverage, complex material support |
Other Methods | Epitaxial Deposition, DLC, Dip/Spin Coating | Specialized applications, simpler processes |
Need help selecting the right deposition method for your project? Contact our experts today!