Silicon deposition is a critical process in semiconductor manufacturing, thin-film production, and various other applications. The methods of silicon deposition are diverse, each tailored to specific requirements such as film quality, thickness, uniformity, and deposition rate. Common techniques include Low Pressure Chemical Vapor Deposition (LPCVD), Plasma Enhanced Chemical Vapor Deposition (PECVD), Sub-Atmospheric Pressure Chemical Vapor Deposition (SACVD), Atmospheric Pressure Chemical Vapor Deposition (APCVD), Atomic Layer Deposition (ALD), Physical Vapor Deposition (PVD), Ultra-High Vacuum Chemical Vapor Deposition (UHV-CVD), Diamond-Like Carbon (DLC), Commercial Film (C-F), and Epitaxial Deposition (Epi). Each method has unique advantages and is chosen based on the specific needs of the application.
Key Points Explained:
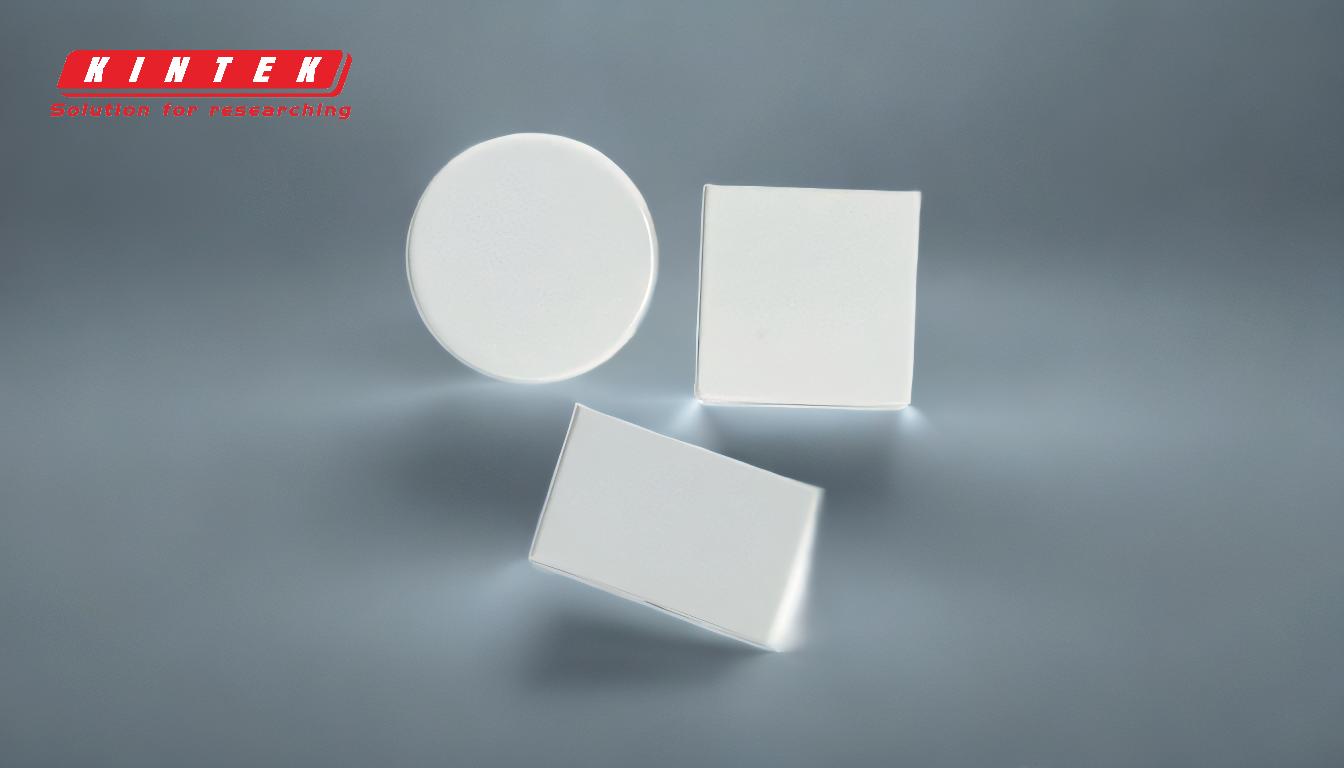
-
Low Pressure Chemical Vapor Deposition (LPCVD):
- Process: LPCVD involves the deposition of silicon at low pressures, typically in the range of 0.1 to 1 Torr. This method uses a chemical reaction between gaseous precursors to deposit a solid film on a substrate.
- Advantages: High film uniformity, excellent step coverage, and high deposition rates.
- Applications: Commonly used for depositing polysilicon, silicon nitride, and silicon dioxide in semiconductor devices.
-
Plasma Enhanced Chemical Vapor Deposition (PECVD):
- Process: PECVD utilizes plasma to enhance the chemical reaction rates of the precursors, allowing deposition at lower temperatures compared to LPCVD.
- Advantages: Lower deposition temperatures, good film quality, and the ability to deposit a variety of materials including silicon, silicon nitride, and silicon dioxide.
- Applications: Widely used in the fabrication of microelectronic devices, solar cells, and optical coatings.
-
Sub-Atmospheric Pressure Chemical Vapor Deposition (SACVD):
- Process: SACVD operates at pressures below atmospheric pressure but higher than LPCVD. It combines the benefits of both APCVD and LPCVD.
- Advantages: Improved film uniformity and step coverage compared to APCVD, with lower equipment complexity than LPCVD.
- Applications: Used in the deposition of silicon dioxide and other dielectric films in semiconductor manufacturing.
-
Atmospheric Pressure Chemical Vapor Deposition (APCVD):
- Process: APCVD occurs at atmospheric pressure, making it simpler and less expensive in terms of equipment compared to LPCVD and PECVD.
- Advantages: High deposition rates and lower equipment costs.
- Applications: Suitable for large-area coatings and less critical applications where high film quality is not essential.
-
Atomic Layer Deposition (ALD):
- Process: ALD is a sequential, self-limiting process where thin films are deposited one atomic layer at a time through alternating exposure to different precursors.
- Advantages: Exceptional control over film thickness and uniformity, conformal coatings even on complex geometries.
- Applications: Ideal for high-k dielectric layers, gate oxides, and other applications requiring precise thickness control.
-
Physical Vapor Deposition (PVD):
- Process: PVD involves the physical transfer of material from a source to a substrate through processes like sputtering or evaporation.
- Advantages: High purity films, good adhesion, and the ability to deposit a wide range of materials.
- Applications: Used in the deposition of metals, alloys, and compounds in microelectronics, optics, and decorative coatings.
-
Ultra-High Vacuum Chemical Vapor Deposition (UHV-CVD):
- Process: UHV-CVD operates at extremely low pressures, often below 10^-6 Torr, to minimize contamination and achieve high-quality films.
- Advantages: Ultra-clean environment, leading to high-purity films with excellent electronic properties.
- Applications: Primarily used in the research and development of advanced semiconductor materials and devices.
-
Diamond-Like Carbon (DLC):
- Process: DLC is a form of amorphous carbon with properties similar to diamond, deposited using PECVD or other techniques.
- Advantages: High hardness, low friction, and chemical inertness.
- Applications: Used in protective coatings, biomedical implants, and wear-resistant surfaces.
-
Commercial Film (C-F):
- Process: This refers to specialized films developed for specific commercial applications, often using a combination of deposition techniques.
- Advantages: Tailored properties for specific applications, such as optical, electrical, or mechanical performance.
- Applications: Used in a wide range of industries including electronics, optics, and packaging.
-
Epitaxial Deposition (Epi):
- Process: Epitaxial deposition involves the growth of a crystalline layer on a crystalline substrate, maintaining the same crystal structure.
- Advantages: High-quality single-crystal films, essential for high-performance electronic devices.
- Applications: Critical in the fabrication of semiconductor devices, particularly in the production of silicon wafers for integrated circuits.
Each of these methods offers unique benefits and is selected based on the specific requirements of the application, such as film quality, deposition rate, and the complexity of the substrate. Understanding these methods allows for the optimal selection of deposition techniques to achieve desired film properties and performance.
Summary Table:
Method | Advantages | Applications |
---|---|---|
LPCVD | High film uniformity, excellent step coverage, high deposition rates | Polysilicon, silicon nitride, silicon dioxide in semiconductor devices |
PECVD | Lower deposition temperatures, good film quality, versatile material options | Microelectronic devices, solar cells, optical coatings |
SACVD | Improved film uniformity, lower equipment complexity | Silicon dioxide and dielectric films in semiconductor manufacturing |
APCVD | High deposition rates, lower equipment costs | Large-area coatings, less critical applications |
ALD | Exceptional thickness control, conformal coatings on complex geometries | High-k dielectric layers, gate oxides |
PVD | High purity films, good adhesion, versatile material options | Metals, alloys, compounds in microelectronics, optics, decorative coatings |
UHV-CVD | Ultra-clean environment, high-purity films | Advanced semiconductor materials and devices |
DLC | High hardness, low friction, chemical inertness | Protective coatings, biomedical implants, wear-resistant surfaces |
C-F | Tailored properties for specific applications | Electronics, optics, packaging |
Epitaxial Deposition (Epi) | High-quality single-crystal films | Silicon wafers for integrated circuits |
Need help selecting the right silicon deposition method for your application? Contact our experts today!