Nanomaterials are synthesized using a variety of techniques, broadly categorized into top-down and bottom-up approaches. Top-down methods involve breaking down larger materials into nanoscale structures, while bottom-up methods build nanomaterials atom by atom or molecule by molecule. Common methods include laser ablation, arc-discharge, and chemical vapor deposition (CVD) for carbon-based nanomaterials, as well as chemical synthesis techniques like hydrothermal and sol-gel methods for a wide range of nanomaterials. These methods are chosen based on the desired properties, scalability, and application of the nanomaterials. Below, the key methods are explained in detail to provide a comprehensive understanding of nanomaterial synthesis.
Key Points Explained:
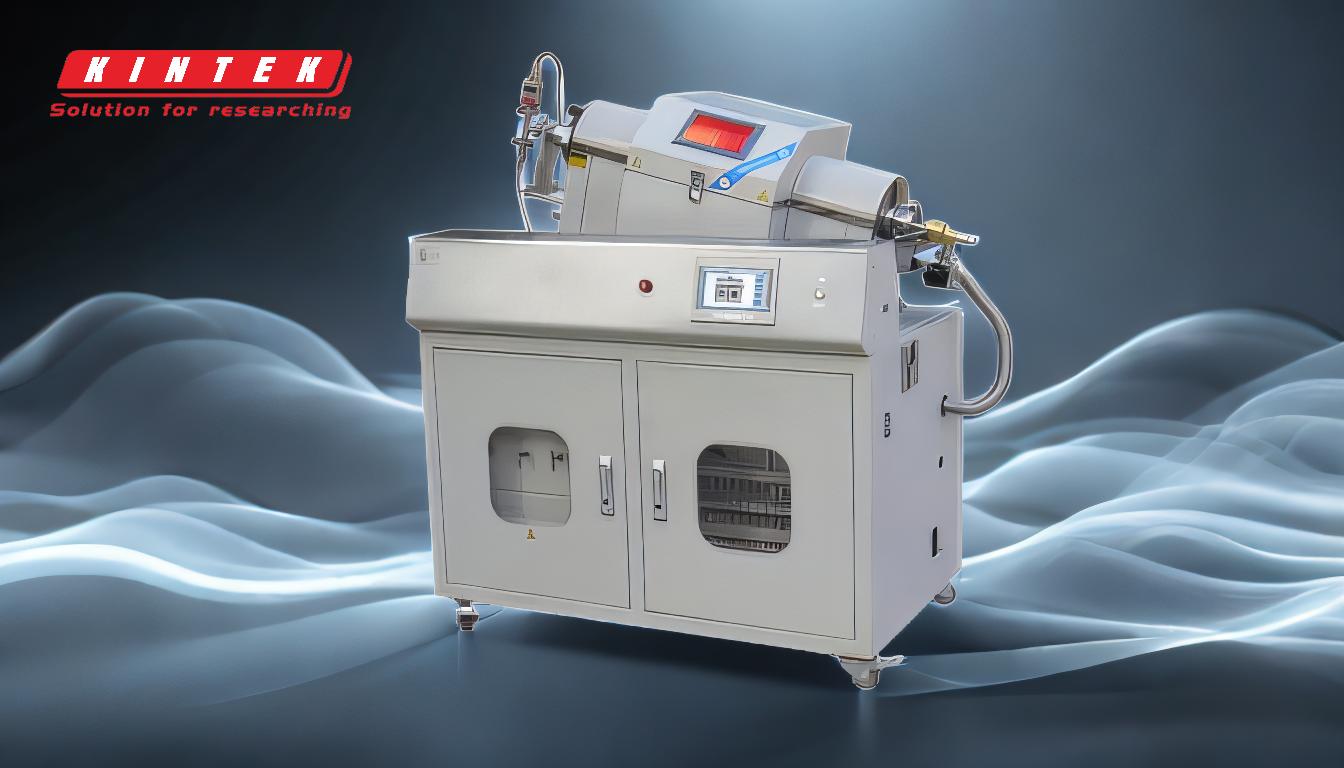
-
Top-Down vs. Bottom-Up Approaches:
- Top-Down: These methods involve reducing bulk materials into nanoscale particles. Examples include mechanical milling and lithography.
- Bottom-Up: These methods build nanomaterials from atomic or molecular components. Examples include chemical vapor deposition (CVD) and sol-gel methods.
-
Laser Ablation:
- A high-energy laser beam is used to vaporize a target material, which then condenses to form nanoparticles.
- Commonly used for synthesizing carbon-based nanomaterials like carbon nanotubes and graphene.
- Advantages: High purity and control over particle size.
- Disadvantages: High energy consumption and limited scalability.
-
Arc-Discharge:
- An electric arc is generated between two electrodes in a gas environment, vaporizing the material to form nanoparticles.
- Widely used for producing carbon nanotubes and fullerenes.
- Advantages: Simple setup and high yield.
- Disadvantages: Requires post-processing to separate and purify nanomaterials.
-
Chemical Vapor Deposition (CVD):
- A precursor gas is decomposed at high temperatures to deposit nanomaterial layers on a substrate.
- Used for synthesizing graphene, carbon nanotubes, and thin films.
- Advantages: High-quality nanomaterials with precise control over thickness and composition.
- Disadvantages: High equipment costs and complex process parameters.
-
Hydrothermal Method:
- A chemical reaction occurs in a sealed, high-temperature, high-pressure environment (autoclave) to form nanoparticles.
- Suitable for producing metal oxides, ceramics, and other inorganic nanomaterials.
- Advantages: Simple equipment and ability to control particle morphology.
- Disadvantages: Long reaction times and limited to specific materials.
-
Sol-Gel Method:
- A colloidal suspension (sol) is transformed into a gel, which is then dried and calcined to form nanomaterials.
- Used for synthesizing oxides, composites, and hybrid materials.
- Advantages: Low processing temperatures and versatility in material composition.
- Disadvantages: Long processing times and potential for contamination.
-
Other Methods:
- Mechanical Milling: Bulk materials are ground into nanoparticles using high-energy ball mills.
- Electrochemical Deposition: Nanomaterials are formed by electroplating metals onto a substrate.
- Biological Synthesis: Uses microorganisms or plant extracts to produce nanoparticles, often for biomedical applications.
Each method has its unique advantages and limitations, making it essential to choose the appropriate technique based on the desired nanomaterial properties and intended application.
Summary Table:
Method | Description | Advantages | Disadvantages |
---|---|---|---|
Top-Down | Breaks bulk materials into nanoscale particles (e.g., mechanical milling). | Scalable, simple setup. | Limited precision, potential contamination. |
Bottom-Up | Builds nanomaterials atom by atom (e.g., CVD, sol-gel). | High precision, versatile. | Complex process, high costs. |
Laser Ablation | Uses laser to vaporize materials, forming nanoparticles. | High purity, controlled particle size. | High energy use, limited scalability. |
Arc-Discharge | Generates electric arc to produce nanoparticles (e.g., carbon nanotubes). | Simple setup, high yield. | Requires post-processing. |
CVD | Decomposes precursor gas to deposit nanomaterials (e.g., graphene). | High-quality, precise control. | Expensive, complex parameters. |
Hydrothermal | Uses high-pressure, high-temperature reactions in autoclaves. | Simple equipment, morphology control. | Long reaction times, material limitations. |
Sol-Gel | Transforms sol into gel, then calcines to form nanomaterials. | Low temperature, versatile. | Long processing, contamination risk. |
Need help choosing the right nanomaterial synthesis method for your project? Contact our experts today!