Sputtering is a vacuum-based thin film deposition process where ions bombard a target material, causing atoms to be ejected and deposited onto a substrate. The process is influenced by several key parameters, including incident ion energy, mass of ions and target atoms, angle of incidence, sputtering yield, chamber pressure, and the type of power source (DC or RF). These factors determine the efficiency, deposition rate, and quality of the thin film. Understanding these parameters is crucial for optimizing the sputtering process for specific applications, such as producing high-purity metallic or oxide films.
Key Points Explained:
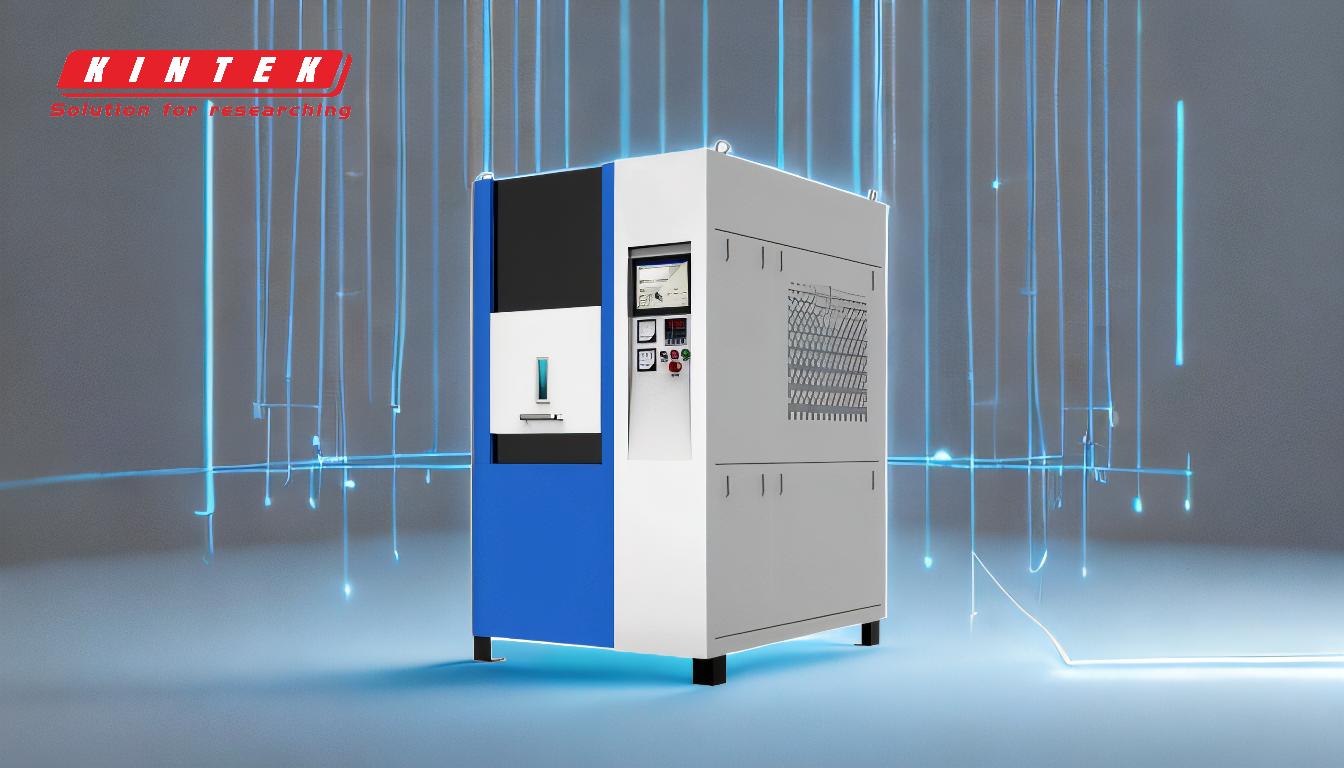
-
Incident Ion Energy:
- The energy of the ions bombarding the target material significantly affects the sputtering yield, which is the number of target atoms ejected per incident ion. Higher ion energy typically increases the sputtering yield, but excessive energy can lead to undesirable effects such as substrate damage or film stress.
-
Mass of Ions and Target Atoms:
- The mass of both the incident ions and the target atoms plays a critical role in the sputtering process. Heavier ions can transfer more momentum to the target atoms, resulting in a higher sputtering yield. Similarly, the mass of the target atoms determines how easily they can be ejected from the surface.
-
Angle of Incidence:
- The angle at which ions strike the target surface affects the sputtering yield. Generally, an oblique angle (not perpendicular) can enhance the sputtering yield due to more efficient energy transfer. However, extreme angles may reduce yield due to glancing collisions.
-
Sputtering Yield:
- Sputtering yield is a measure of the efficiency of the sputtering process, defined as the number of target atoms ejected per incident ion. It varies depending on the target material, ion energy, mass, and angle of incidence. Optimizing these factors is essential for achieving desired deposition rates and film quality.
-
Chamber Pressure:
- The pressure within the sputtering chamber influences the mean free path of the ejected particles and the overall coverage of the substrate. Lower pressures are typically used to minimize collisions and ensure a more directed deposition, while higher pressures can improve coverage but may reduce deposition rates.
-
Type of Power Source (DC or RF):
- The choice between direct current (DC) and radio frequency (RF) power sources affects the sputtering process in terms of deposition rate, material compatibility, and cost. DC sputtering is commonly used for conductive materials, while RF sputtering is suitable for insulating materials due to its ability to prevent charge buildup.
-
Kinetic Energy of Emitted Particles:
- The kinetic energy of the particles ejected from the target determines their direction and how they deposit on the substrate. Higher kinetic energy can lead to better adhesion and denser films, but it must be controlled to avoid damaging the substrate or creating stress within the film.
-
Excess Energy of Metal Ions:
- The excess energy of metal ions during the sputtering process can increase surface mobility, which affects the quality of the deposited film. Proper control of this energy can lead to smoother and more uniform films, enhancing the overall performance of the deposited layer.
Understanding and optimizing these parameters is essential for achieving high-quality thin films with desired properties in various applications, from electronics to optical coatings.
Summary Table:
Parameter | Impact on Sputtering Process |
---|---|
Incident Ion Energy | Higher energy increases sputtering yield but may cause substrate damage. |
Mass of Ions and Target Atoms | Heavier ions and target atoms enhance sputtering yield due to momentum transfer. |
Angle of Incidence | Oblique angles improve yield; extreme angles reduce it. |
Sputtering Yield | Measures efficiency; depends on material, ion energy, mass, and angle. |
Chamber Pressure | Lower pressure ensures directed deposition; higher pressure improves coverage. |
Power Source (DC or RF) | DC for conductive materials; RF for insulating materials to prevent charge buildup. |
Kinetic Energy of Particles | Higher energy improves adhesion but must be controlled to avoid substrate damage. |
Excess Energy of Metal Ions | Increases surface mobility, leading to smoother and more uniform films. |
Ready to optimize your sputtering process? Contact our experts today for tailored solutions!