Press molds, also known as press dies, are essential tools in manufacturing processes, particularly in metal stamping and rubber molding. They are designed to shape materials into specific forms with precision and consistency. A press mold typically consists of several key components, including the punch, die, die set, and guide post, as well as additional plates like the punch plate, stripper plate, backing plate, and die plate. These components work together to ensure the mold operates efficiently and produces high-quality, stable products. While press molds are expensive to manufacture, their ability to mass-produce consistent parts makes them invaluable in industrial applications.
Key Points Explained:
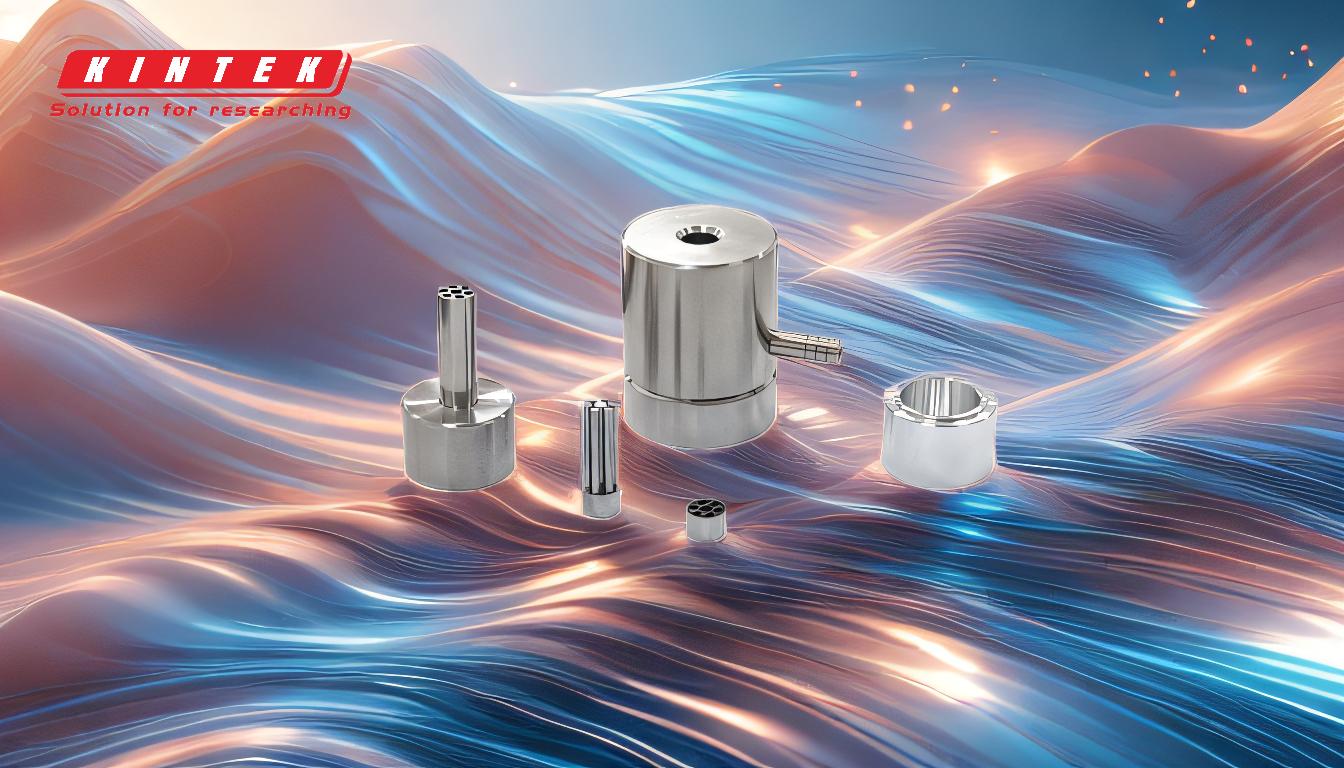
-
Main Components of a Press Mold
- Punch: The punch is the upper part of the mold that applies force to the material, shaping it into the desired form. It moves downward into the die to create the product.
- Die: The die is the lower part of the mold that contains the cavity or shape into which the material is pressed. It works in tandem with the punch to form the final product.
- Die Set: The die set is the assembly that holds the punch and die together, ensuring proper alignment during the pressing process.
- Guide Post: The guide post ensures precise alignment of the punch and die, preventing misalignment and ensuring consistent product quality.
-
Additional Plates and Their Functions
- Punch Plate: This plate holds the punch in place and ensures it remains stable during the pressing operation.
- Stripper Plate: The stripper plate helps remove the finished product from the punch after the pressing process is complete. It prevents the material from sticking to the punch.
- Backing Plate: The backing plate provides support to the die and other components, ensuring they remain rigid and stable during operation.
- Die Plate: The die plate holds the die and ensures it remains securely in place during the pressing process.
-
Functionality and Process
- Press molds work by applying force to a material (such as metal or rubber) between the punch and die, shaping it into the desired form. The cavities in the die conform to the outer shape of the finished part, ensuring precision and consistency.
- The process involves aligning the punch and die using the guide post, applying force to the material, and then removing the finished product using the stripper plate.
-
Advantages of Press Molds
- Mass Production: Press molds are designed for high-volume production, making them ideal for industries that require large quantities of identical parts.
- Consistency: The precision of press molds ensures minimal variation in product quality, resulting in stable and reliable output.
- Durability: While expensive to manufacture, press molds are built to withstand repeated use, making them a cost-effective solution in the long run.
-
Applications of Press Molds
- Press molds are widely used in industries such as automotive, aerospace, electronics, and consumer goods manufacturing. They are particularly valuable for producing complex shapes and high-precision components.
By understanding the components and functionality of press molds, manufacturers can make informed decisions about their use in production processes, ensuring efficiency, consistency, and cost-effectiveness.
Summary Table:
Component | Function |
---|---|
Punch | Applies force to shape materials into desired forms. |
Die | Contains the cavity for shaping materials. |
Die Set | Holds punch and die together for proper alignment. |
Guide Post | Ensures precise alignment of punch and die. |
Punch Plate | Holds the punch in place during operation. |
Stripper Plate | Removes finished products from the punch. |
Backing Plate | Provides support to the die and other components. |
Die Plate | Holds the die securely in place. |
Ready to optimize your manufacturing process with press molds? Contact us today for expert guidance!