Thin film deposition is a critical process in materials science and engineering, enabling the creation of thin layers of materials on substrates for applications in electronics, optics, and coatings. Physical methods of thin film deposition, particularly Physical Vapour Deposition (PVD), are widely used due to their ability to produce high-purity and high-performance films. PVD techniques, such as sputtering and evaporation, involve the physical transfer of material from a source to a substrate, often in a vacuum environment. These methods are essential for applications requiring precise control over film thickness, composition, and structure.
Key Points Explained:
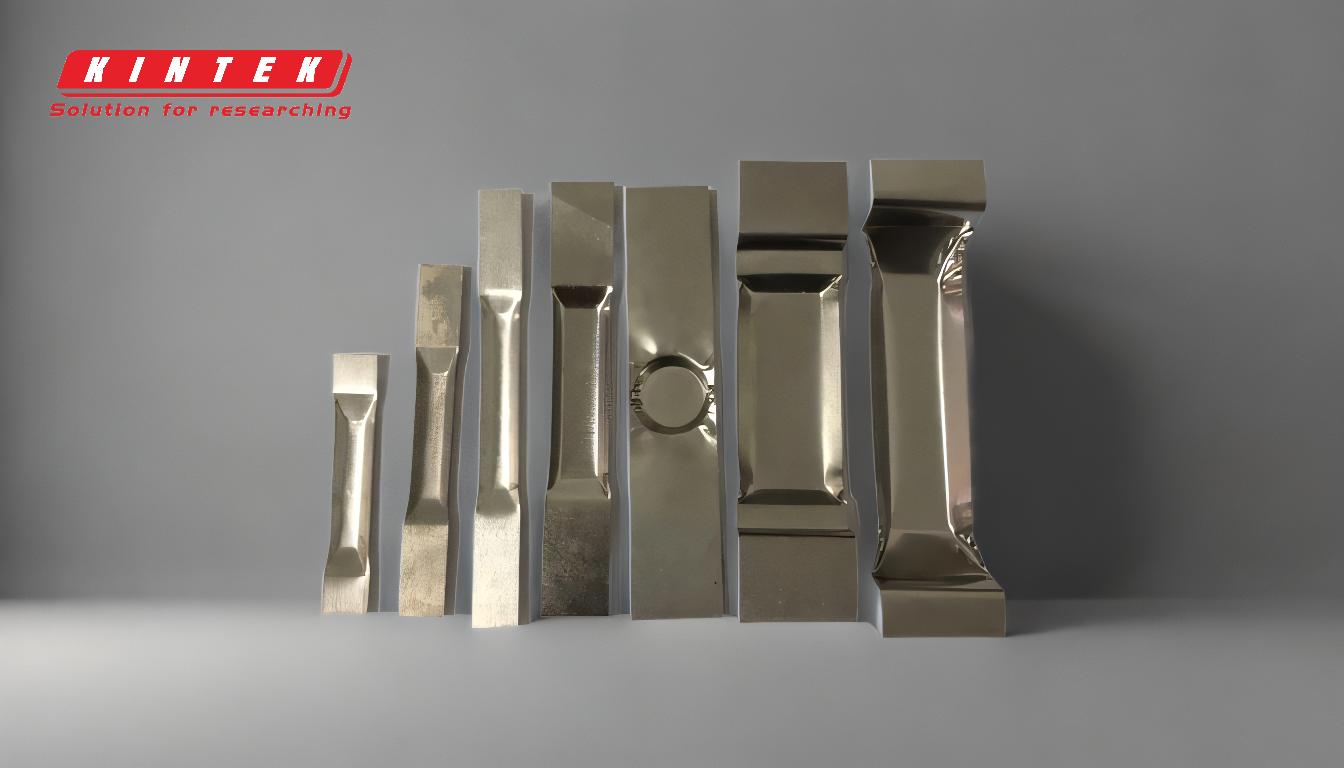
-
Physical Vapour Deposition (PVD):
- PVD is a family of thin film deposition techniques that rely on physical processes to transfer material from a source to a substrate. The most common PVD methods include:
- Sputtering: This involves bombarding a target material with high-energy ions, causing atoms to be ejected and deposited onto a substrate. Sputtering is widely used in the semiconductor industry due to its ability to produce uniform and high-quality films.
- Thermal Evaporation: In this method, the source material is heated until it evaporates, and the vapor condenses onto the substrate. This technique is often used for depositing metals and simple compounds.
- Electron Beam Evaporation: Similar to thermal evaporation, but the source material is heated using an electron beam, allowing for higher temperatures and the deposition of refractory materials.
- PVD is a family of thin film deposition techniques that rely on physical processes to transfer material from a source to a substrate. The most common PVD methods include:
-
Advantages of PVD:
- High Purity: PVD processes occur in a vacuum, minimizing contamination and resulting in high-purity films.
- Precision Control: PVD allows for precise control over film thickness, composition, and structure, making it suitable for applications requiring high performance.
- Versatility: PVD can deposit a wide range of materials, including metals, alloys, and compounds, onto various substrates.
-
Applications of PVD:
- Semiconductors: PVD is extensively used in the semiconductor industry to deposit thin films for integrated circuits, solar cells, and displays.
- Optical Coatings: PVD is used to create anti-reflective, reflective, and protective coatings for lenses, mirrors, and other optical components.
- Decorative Coatings: PVD is employed to deposit thin films with specific colors and finishes for decorative purposes, such as on watches and jewelry.
-
Comparison with Chemical Vapour Deposition (CVD):
- While PVD relies on physical processes, CVD involves chemical reactions to deposit thin films. CVD is often preferred for applications requiring conformal coatings and complex geometries, but PVD offers advantages in terms of material purity and process control.
-
Emerging Trends in PVD:
- Atomic Layer Deposition (ALD): Although ALD is primarily a chemical method, it shares similarities with PVD in terms of precision and control. ALD is gaining popularity for applications requiring ultra-thin and uniform films.
- Hybrid Techniques: Combining PVD with other deposition methods, such as CVD or ALD, is becoming more common to leverage the strengths of each technique and achieve superior film properties.
In summary, Physical Vapour Deposition (PVD) is a cornerstone of thin film technology, offering high purity, precision, and versatility. Its applications span across industries, from semiconductors to optics, and ongoing advancements continue to expand its capabilities.
Summary Table:
Method | Description | Key Applications |
---|---|---|
Sputtering | Bombards target material with high-energy ions to deposit atoms onto a substrate | Semiconductors, optical coatings |
Thermal Evaporation | Heats source material until it evaporates and condenses onto a substrate | Metals, simple compounds |
Electron Beam Evaporation | Uses an electron beam to heat and evaporate source material | Refractory materials, high-temperature films |
Learn how PVD techniques can enhance your thin film applications—contact our experts today!