Chemical vapor deposition (CVD) is a versatile and widely used technique for depositing thin films and coatings on substrates. The process relies heavily on the use of precursors, which are volatile compounds that decompose or react to form the desired material on the substrate. Precursors in CVD can be categorized into several types, including hydrides, halides, metal carbonyls, metal alkyls, and metal alkoxides. These precursors must be volatile yet stable enough to be transported to the reactor, where they decompose or react under controlled conditions to deposit the desired material. The choice of precursor depends on the specific material being deposited, the properties required for the final product, and the conditions of the CVD process.
Key Points Explained:
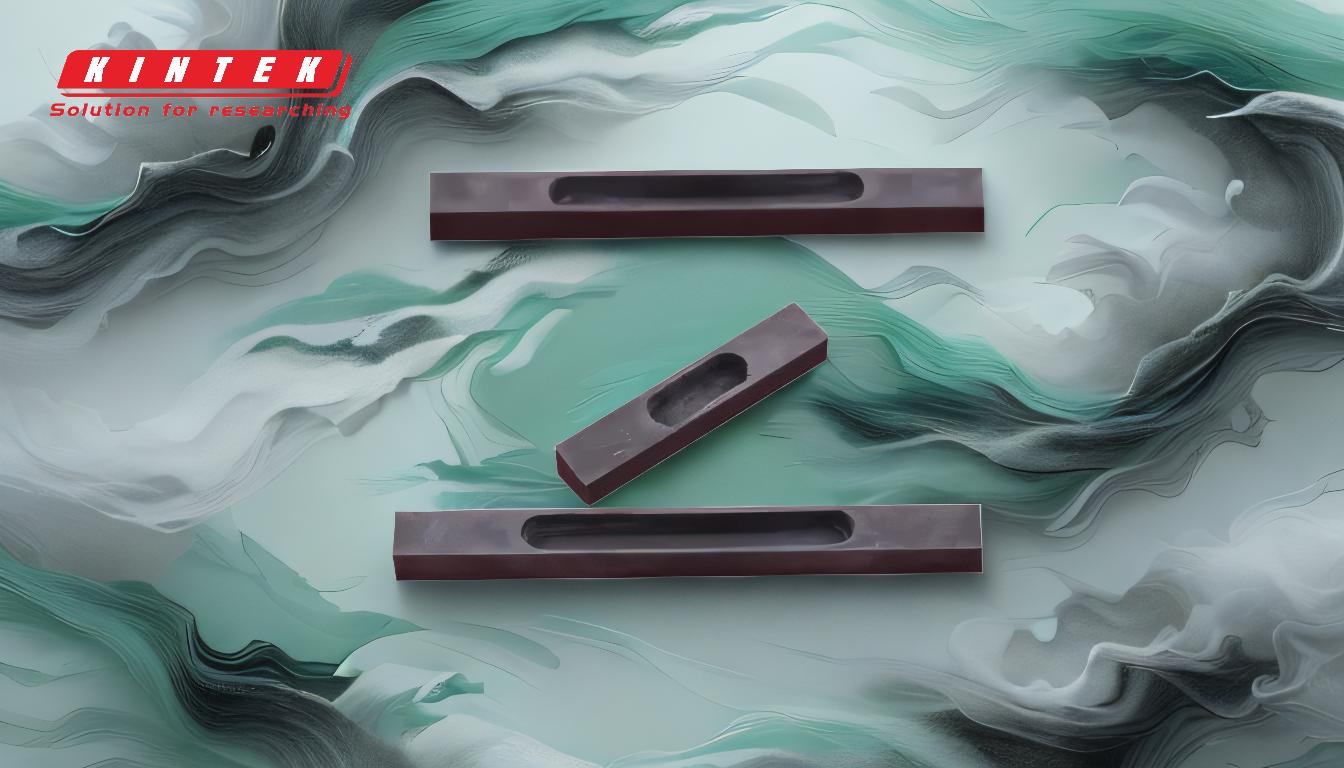
-
Types of Precursors in CVD:
- Hydrides: These are compounds containing hydrogen and another element. Common examples include silane (SiH4), germane (GeH4), and ammonia (NH3). Hydrides are often used in the deposition of semiconductors and nitrides.
- Halides: These are compounds containing halogens (e.g., fluorine, chlorine, bromine). Examples include titanium tetrachloride (TiCl4) and tungsten hexafluoride (WF6). Halides are commonly used in the deposition of metals and metal oxides.
- Metal Carbonyls: These are organometallic compounds containing carbon monoxide ligands. Examples include nickel carbonyl (Ni(CO)4) and iron pentacarbonyl (Fe(CO)5). Metal carbonyls are used in the deposition of pure metals.
- Metal Alkyls: These are compounds where a metal is bonded to one or more alkyl groups. Examples include trimethylaluminum (Al(CH3)3) and diethylzinc (Zn(C2H5)2). Metal alkyls are often used in the deposition of III-V semiconductors.
- Metal Alkoxides: These are compounds where a metal is bonded to one or more alkoxide groups. Examples include titanium isopropoxide (Ti(OCH(CH3)2)4) and aluminum isopropoxide (Al(OCH(CH3)2)3). Metal alkoxides are used in the deposition of metal oxides.
-
Properties of Precursors:
- Volatility: Precursors must be volatile enough to be transported in the gas phase to the reaction chamber.
- Stability: While precursors need to be volatile, they must also be stable enough to prevent premature decomposition or reaction before reaching the substrate.
- Purity: High purity precursors are essential to avoid contamination of the deposited film, which can affect its properties.
- Reactivity: Precursors must be reactive under the conditions of the CVD process, typically involving heat, to decompose or react and form the desired material.
-
Chemical Reactions in CVD:
- Decomposition: Many precursors decompose upon heating, releasing the desired element or compound. For example, silane (SiH4) decomposes to form silicon and hydrogen gas.
- Oxidation: Some precursors react with oxygen to form oxides. For example, titanium tetrachloride (TiCl4) can react with oxygen to form titanium dioxide (TiO2).
- Reduction: Certain precursors are reduced to form pure metals. For example, tungsten hexafluoride (WF6) can be reduced by hydrogen to form tungsten metal.
- Hydrolysis: Some precursors react with water vapor to form oxides or hydroxides. For example, aluminum alkoxides can hydrolyze to form aluminum oxide.
-
Applications of Precursors in CVD:
- Semiconductor Manufacturing: Hydrides and metal alkyls are commonly used in the deposition of semiconductors like silicon, germanium, and III-V compounds.
- Protective Coatings: Halides and metal carbonyls are used to deposit hard, wear-resistant coatings such as titanium nitride (TiN) and chromium nitride (CrN).
- Optical Coatings: Metal alkoxides are used to deposit transparent oxides like titanium dioxide (TiO2) and aluminum oxide (Al2O3) for optical applications.
- Nanotechnology: Precursors are used in the growth of nanostructures like carbon nanotubes and graphene, where precise control over the deposition process is crucial.
-
Challenges in Precursor Selection:
- Toxicity and Safety: Many precursors are toxic, flammable, or reactive, requiring careful handling and storage.
- Cost: High-purity precursors can be expensive, impacting the overall cost of the CVD process.
- Compatibility: Precursors must be compatible with the specific CVD equipment and process conditions, including temperature, pressure, and gas flow rates.
In summary, the selection of precursors in CVD is critical to the success of the deposition process. The choice of precursor depends on the material to be deposited, the desired properties of the final product, and the specific conditions of the CVD process. Understanding the properties and behavior of different precursors is essential for optimizing the CVD process and achieving high-quality thin films and coatings.
Summary Table:
Precursor Type | Examples | Applications |
---|---|---|
Hydrides | SiH4, GeH4, NH3 | Semiconductor and nitride deposition |
Halides | TiCl4, WF6 | Metal and metal oxide deposition |
Metal Carbonyls | Ni(CO)4, Fe(CO)5 | Pure metal deposition |
Metal Alkyls | Al(CH3)3, Zn(C2H5)2 | III-V semiconductor deposition |
Metal Alkoxides | Ti(OCH(CH3)2)4, Al(OCH(CH3)2)3 | Metal oxide deposition |
Need help selecting the right CVD precursors for your application? Contact our experts today!