Physical vapor deposition (PVD) is a widely used technique for depositing thin films, particularly in advanced manufacturing and electronics. The process involves the transfer of material from a source (target) to a substrate in a vacuum environment, where the material is vaporized and then condensed onto the substrate to form a thin film. PVD is highly valued for its ability to produce precise, uniform, and high-quality films with controlled properties. The principles of PVD revolve around three main components: the source, the transport process, and the substrate. Each of these components plays a critical role in determining the quality, structure, and functionality of the deposited film. Additionally, the interactions between the material and the substrate, as well as the deposition parameters, influence the growth mode and final properties of the thin film.
Key Points Explained:
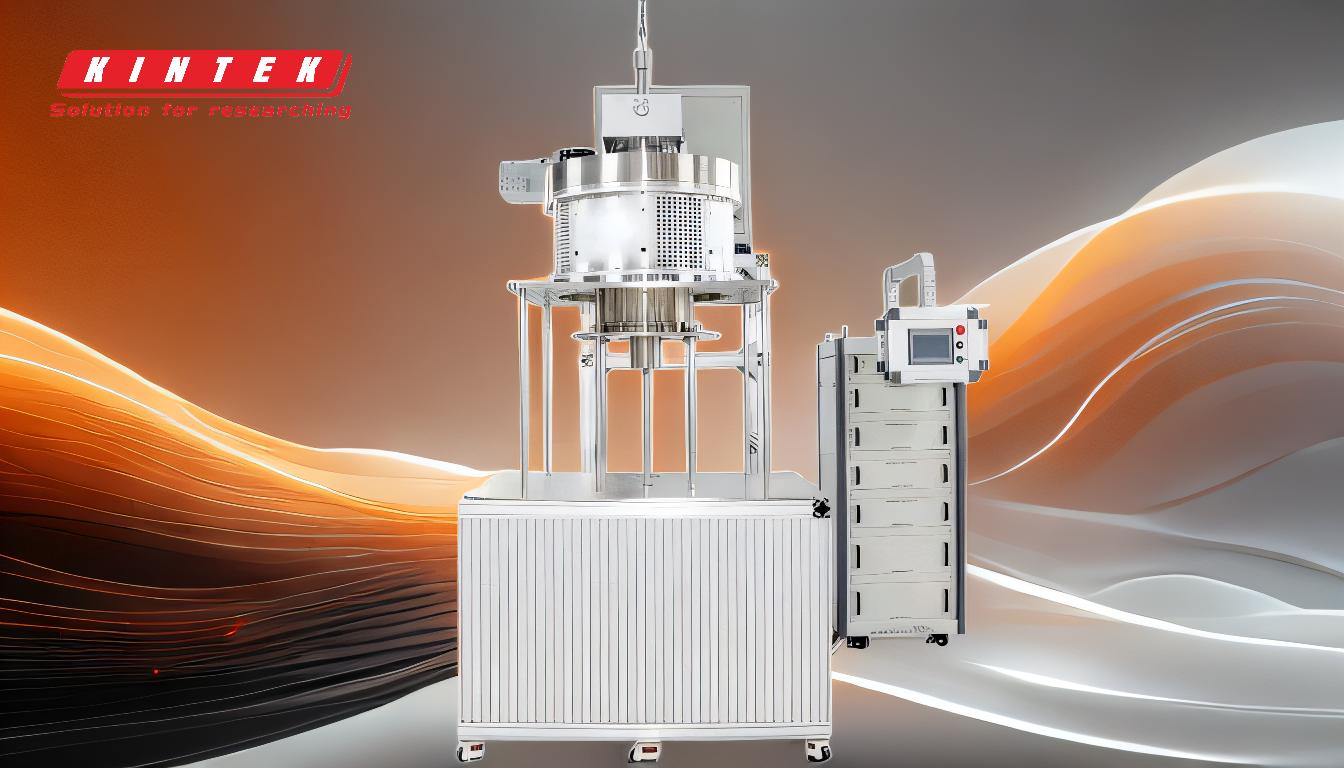
-
Components of PVD:
- Source (Target): The material to be deposited is typically in solid form, such as a metal or ceramic target. The source is vaporized using techniques like sputtering, evaporation, or arc discharge.
- Transport Process: The vaporized material is transported through a vacuum or low-pressure environment to the substrate. This step ensures minimal contamination and precise control over the deposition process.
- Substrate: The surface onto which the thin film is deposited. The substrate's properties, such as temperature, surface roughness, and chemical composition, influence the film's adhesion, structure, and performance.
-
Vaporization Techniques:
- Sputtering: A common PVD method where high-energy ions bombard the target, ejecting atoms or molecules that then deposit onto the substrate. This technique is known for producing highly uniform and dense films.
- Evaporation: The target material is heated to its vaporization point, often using an electron beam or resistive heating. The vaporized material then condenses on the substrate. This method is suitable for materials with low melting points.
- Arc-PVD: An electric arc is used to vaporize the target material. This method is particularly effective for depositing hard coatings and is widely used in industrial applications.
-
Thin Film Growth Modes:
- Adsorption: The initial stage where vaporized material adheres to the substrate surface.
- Surface Diffusion: The adsorbed atoms or molecules migrate across the substrate surface to find stable positions.
- Nucleation: Small clusters of atoms or molecules form, which then grow into larger islands and eventually coalesce into a continuous film.
-
Influence of Deposition Parameters:
- Substrate Temperature: Higher temperatures can enhance surface diffusion and improve film quality, but excessive heat may lead to unwanted reactions or defects.
- Deposition Rate: Controlled deposition rates ensure uniform film thickness and minimize defects such as pinholes or voids.
- Pressure and Environment: The vacuum or low-pressure environment reduces contamination and allows for precise control over the deposition process.
-
Post-Deposition Treatments:
- Annealing: Heat treatment can improve the film's crystallinity, adhesion, and mechanical properties.
- Analysis and Optimization: The deposited film is analyzed for properties such as thickness, uniformity, and composition. This feedback is used to refine the deposition process for future runs.
-
Applications of PVD:
- PVD is used in a wide range of industries, including electronics (e.g., semiconductor devices, optical coatings), aerospace (e.g., protective coatings), and medical devices (e.g., biocompatible coatings).
- The ability to deposit precise and uniform films makes PVD ideal for advanced thin-film devices, such as solar cells, sensors, and microelectromechanical systems (MEMS).
By understanding these principles, equipment and consumable purchasers can make informed decisions about the materials, processes, and parameters required for specific applications. This knowledge ensures the selection of the right PVD equipment and consumables to achieve the desired film properties and performance.
Summary Table:
Aspect | Details |
---|---|
Components of PVD | Source (Target), Transport Process, Substrate |
Vaporization Techniques | Sputtering, Evaporation, Arc-PVD |
Thin Film Growth Modes | Adsorption, Surface Diffusion, Nucleation |
Deposition Parameters | Substrate Temperature, Deposition Rate, Pressure and Environment |
Post-Deposition Treatments | Annealing, Analysis and Optimization |
Applications | Electronics, Aerospace, Medical Devices, Solar Cells, MEMS |
Discover how PVD can elevate your thin film applications—contact our experts today for tailored solutions!