Physical Vapour Deposition (PVD) is a thin-film coating process that involves the physical transfer of material from a source to a substrate under vacuum conditions. The process is widely used in industries such as semiconductors, optics, and tool coatings due to its ability to produce high-quality, durable, and precise coatings. The principles of PVD revolve around the vaporization of a solid or liquid material, its transportation through a vacuum or low-pressure environment, and its subsequent condensation onto a substrate to form a thin film. The two primary methods of PVD are Thermal Evaporation and Sputtering, each with distinct mechanisms and applications.
Key Points Explained:
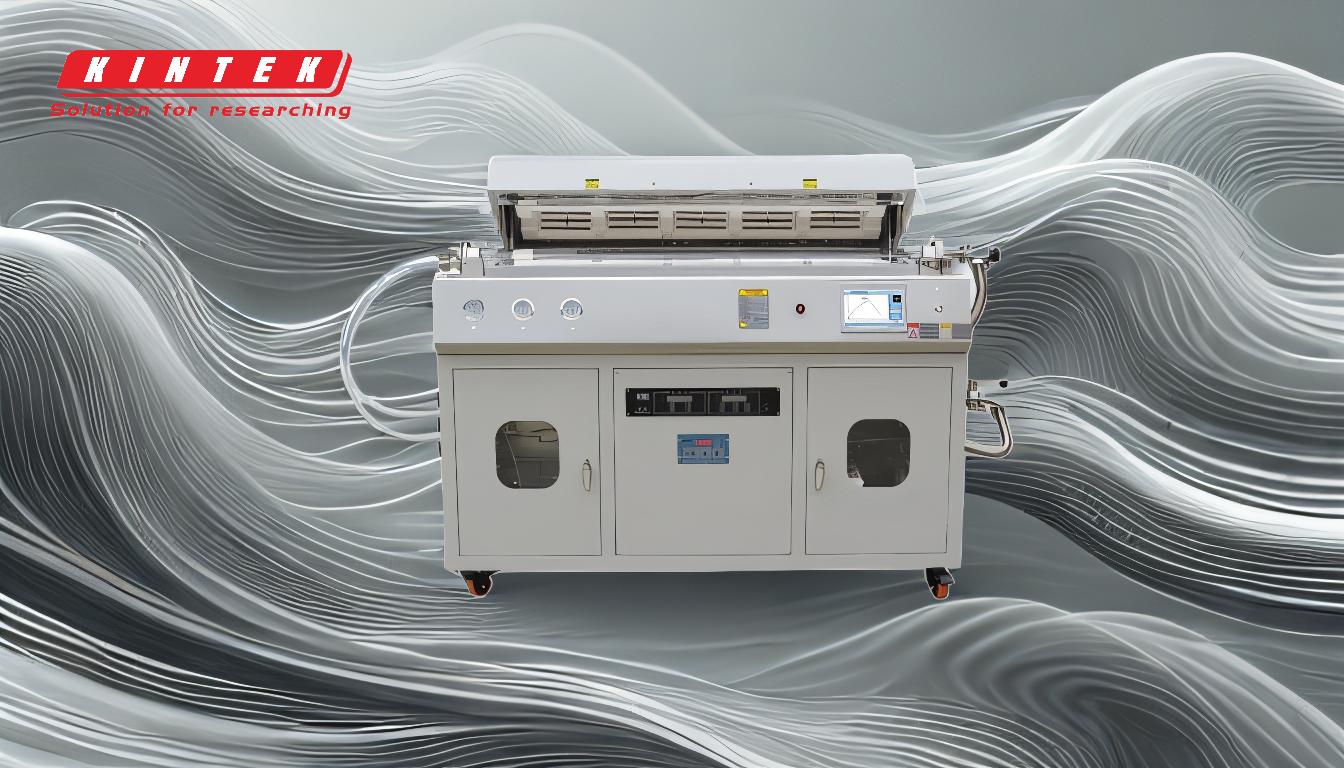
-
Basic Principles of Physical Vapour Deposition (PVD):
- PVD involves the physical transformation of a material from a solid or liquid state into a vapor phase, followed by its deposition onto a substrate.
- The process occurs in a vacuum or low-pressure environment to minimize contamination and ensure precise control over the deposition process.
- The vaporized material travels through the vacuum chamber and condenses on the substrate, forming a thin, uniform film.
-
Thermal Evaporation Deposition:
- In thermal evaporation, the target material is heated to high temperatures until it vaporizes. This is typically achieved using resistive heating, electron beams, or lasers.
- The vaporized material then travels through the vacuum chamber and deposits onto the substrate, forming a thin film.
- This method is suitable for materials with relatively low melting points and is commonly used for depositing metals and simple compounds.
-
Sputtering Deposition:
- Sputtering involves bombarding a target material with high-energy ions (usually argon ions) in a high-vacuum chamber.
- The impact of the ions dislodges atoms from the target material, which are then ejected and deposited onto the substrate.
- Sputtering is versatile and can be used for a wide range of materials, including metals, alloys, and ceramics. It is particularly useful for depositing materials with high melting points.
-
Advantages of PVD:
- High Purity and Density: PVD coatings are highly pure and dense, making them suitable for applications requiring excellent mechanical and chemical properties.
- Precision and Control: The process allows for precise control over film thickness, composition, and structure by adjusting deposition parameters such as temperature, pressure, and power.
- Versatility: PVD can deposit a wide variety of materials, including metals, alloys, ceramics, and compounds, making it applicable in numerous industries.
-
Applications of PVD:
- Semiconductors: PVD is used to deposit thin films of metals and dielectrics in the fabrication of integrated circuits and microelectronic devices.
- Optics: It is employed to create anti-reflective, reflective, and protective coatings on optical components.
- Tool Coatings: PVD coatings enhance the hardness, wear resistance, and durability of cutting tools, molds, and other industrial components.
-
Comparison with Chemical Vapour Deposition (CVD):
- Unlike PVD, which relies on physical processes, CVD involves chemical reactions to deposit materials onto a substrate.
- CVD typically requires higher temperatures and can produce coatings with excellent conformality, making it suitable for complex geometries.
- However, PVD offers advantages in terms of lower processing temperatures, better control over film properties, and reduced chemical contamination.
In summary, Physical Vapour Deposition is a versatile and precise thin-film coating technique that relies on the physical vaporization and deposition of materials. Its two main methods, Thermal Evaporation and Sputtering, cater to different material requirements and applications. PVD offers numerous advantages, including high purity, density, and control over film properties, making it a preferred choice in industries ranging from electronics to tool manufacturing.
Summary Table:
Aspect | Details |
---|---|
Basic Principles | Physical transformation of material into vapor, transported in vacuum, and condensed on substrate. |
Methods | Thermal Evaporation (heating to vaporize) and Sputtering (ion bombardment to dislodge atoms). |
Advantages | High purity, precise control, versatility in materials (metals, alloys, ceramics). |
Applications | Semiconductors, optics (anti-reflective coatings), tool coatings (wear resistance). |
Comparison with CVD | Lower temperatures, better control, reduced contamination compared to Chemical Vapour Deposition. |
Unlock the potential of PVD for your industry—contact our experts today to learn more!