Rotary kilns are essential in cement production but face several operational challenges, including dust generation, low thermal efficiency, and non-uniform product quality. These issues can be mitigated through targeted solutions such as upgrading burner systems, optimizing refractory lining, and improving the understanding of transport phenomena within the kiln. Addressing these problems not only enhances performance but also extends the equipment's lifespan and reduces operational costs. Below, the key problems and their remedies are explained in detail.
Key Points Explained:
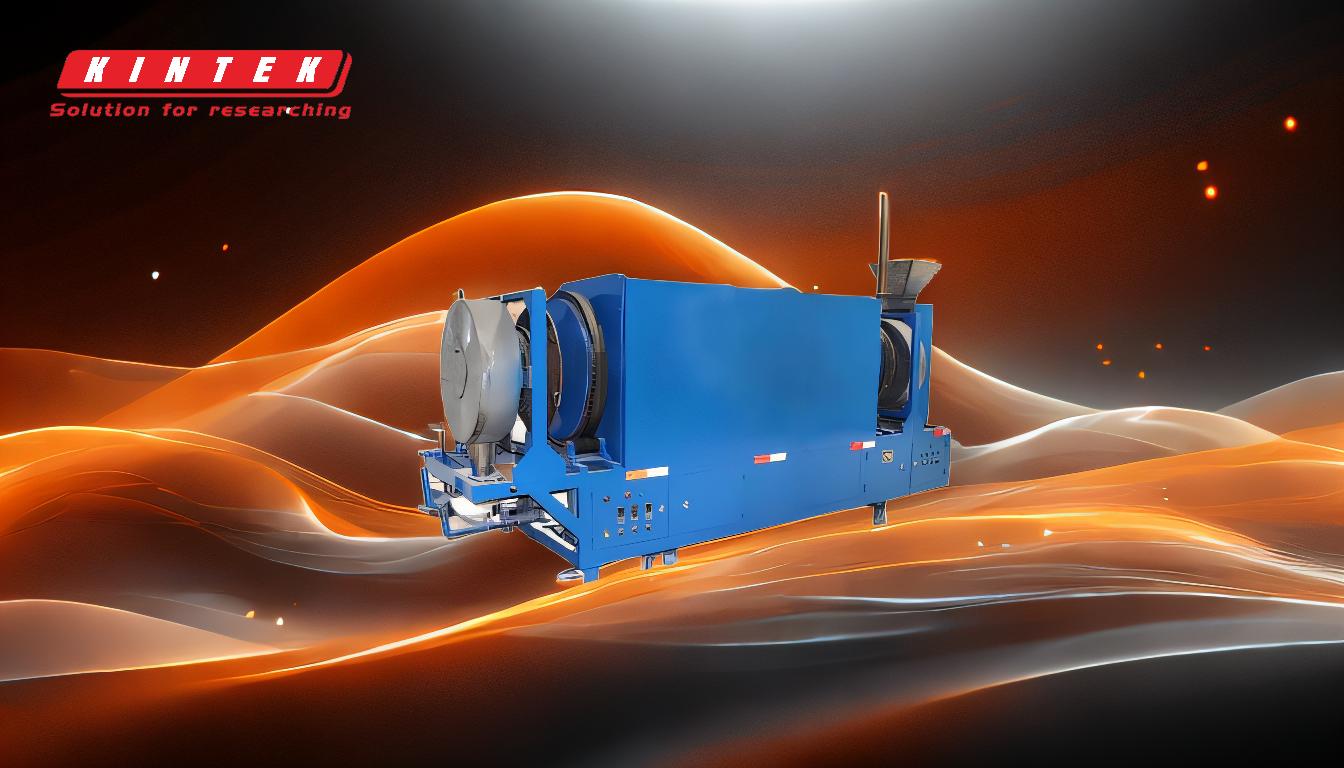
-
Dust Generation
- Problem: Dust generation is a common issue in rotary kilns, leading to environmental pollution, health hazards, and material loss.
-
Remedies:
- Install efficient dust collection systems, such as electrostatic precipitators or bag filters, to capture and reduce dust emissions.
- Optimize kiln feed composition to minimize fine particles that contribute to dust.
- Regularly inspect and maintain seals and joints to prevent dust leakage.
-
Low Thermal Efficiency
- Problem: Rotary kilns often suffer from low thermal efficiency due to heat loss through radiation, convection, and exhaust gases.
-
Remedies:
- Upgrade burner systems to improve combustion efficiency and reduce fuel consumption. Modern burners with advanced nozzles and sensors can enhance energy utilization.
- Install heat recovery systems, such as preheaters or waste heat boilers, to capture and reuse excess heat.
- Optimize kiln insulation to minimize heat loss and maintain consistent internal temperatures.
-
Non-Uniform Product Quality
- Problem: Inconsistent heating and material flow within the kiln can lead to non-uniform product quality, affecting the final cement properties.
-
Remedies:
- Improve the understanding of transport phenomena, such as momentum and energy transport, to optimize particle motion and heating rates.
- Use advanced control systems to monitor and adjust kiln parameters, such as temperature, rotation speed, and feed rate, in real-time.
- Ensure uniform feed distribution and proper alignment of the kiln to avoid material segregation and uneven heating.
-
Burner-Related Issues
- Problem: Burner problems, such as nozzle blockages, cone wear, and sensor malfunctions, can disrupt combustion and reduce efficiency.
-
Remedies:
- Regularly inspect and maintain burner components, replacing worn or damaged parts as needed.
- Upgrade to modern burners with improved designs and materials to enhance performance and durability.
- Implement predictive maintenance strategies using sensor data to detect and address issues before they escalate.
-
Refractory Failure
- Problem: Refractory lining failure can result from thermal cycling, chemical attack, or mechanical stress, leading to costly repairs and downtime.
-
Remedies:
- Minimize thermal cycling by avoiding rapid heating or cooling and reducing unnecessary shutdowns.
- Select refractory materials that are resistant to specific chemical exposures, such as chlorides, and ensure proper installation.
- Conduct regular inspections to identify early signs of wear or damage and address them promptly.
-
Transport Phenomena Optimization
- Problem: Inefficient transport of momentum and energy within the kiln bed can lead to suboptimal particle motion and heating rates.
-
Remedies:
- Conduct detailed studies to quantify momentum and energy transport mechanisms, enabling better control of particle behavior.
- Use computational modeling and simulations to optimize kiln design and operating conditions.
- Implement advanced instrumentation to monitor bed dynamics and adjust parameters for improved performance.
By addressing these challenges with targeted solutions, rotary kiln operators can achieve higher efficiency, better product quality, and reduced environmental impact, ultimately enhancing the overall sustainability of cement production.
Summary Table:
Challenge | Problem | Remedies |
---|---|---|
Dust Generation | Environmental pollution, health hazards, material loss | Install dust collection systems, optimize feed composition, maintain seals and joints |
Low Thermal Efficiency | Heat loss through radiation, convection, and exhaust gases | Upgrade burner systems, install heat recovery systems, optimize kiln insulation |
Non-Uniform Product Quality | Inconsistent heating and material flow | Improve transport phenomena understanding, use advanced control systems, ensure uniform feed |
Burner-Related Issues | Nozzle blockages, cone wear, sensor malfunctions | Regular maintenance, upgrade to modern burners, implement predictive maintenance |
Refractory Failure | Thermal cycling, chemical attack, mechanical stress | Minimize thermal cycling, select resistant materials, conduct regular inspections |
Transport Phenomena | Inefficient momentum and energy transport | Study transport mechanisms, use computational modeling, implement advanced instrumentation |
Optimize your rotary kiln operations today—contact our experts for tailored solutions!