PVD (Physical Vapor Deposition) and CVD (Chemical Vapor Deposition) are two widely used techniques for depositing thin films onto substrates. PVD involves the physical vaporization of materials, typically through processes like sputtering or evaporation, followed by condensation onto a substrate in a vacuum environment. CVD, on the other hand, relies on chemical reactions, where gaseous precursors react on the substrate surface to form a solid coating. The choice between PVD and CVD depends on factors such as the desired film properties, substrate material, operating temperatures, and application requirements. While PVD is known for its ability to deposit a wide range of materials at lower temperatures, CVD excels in producing dense, uniform coatings, especially on complex geometries, albeit at higher temperatures.
Key Points Explained:
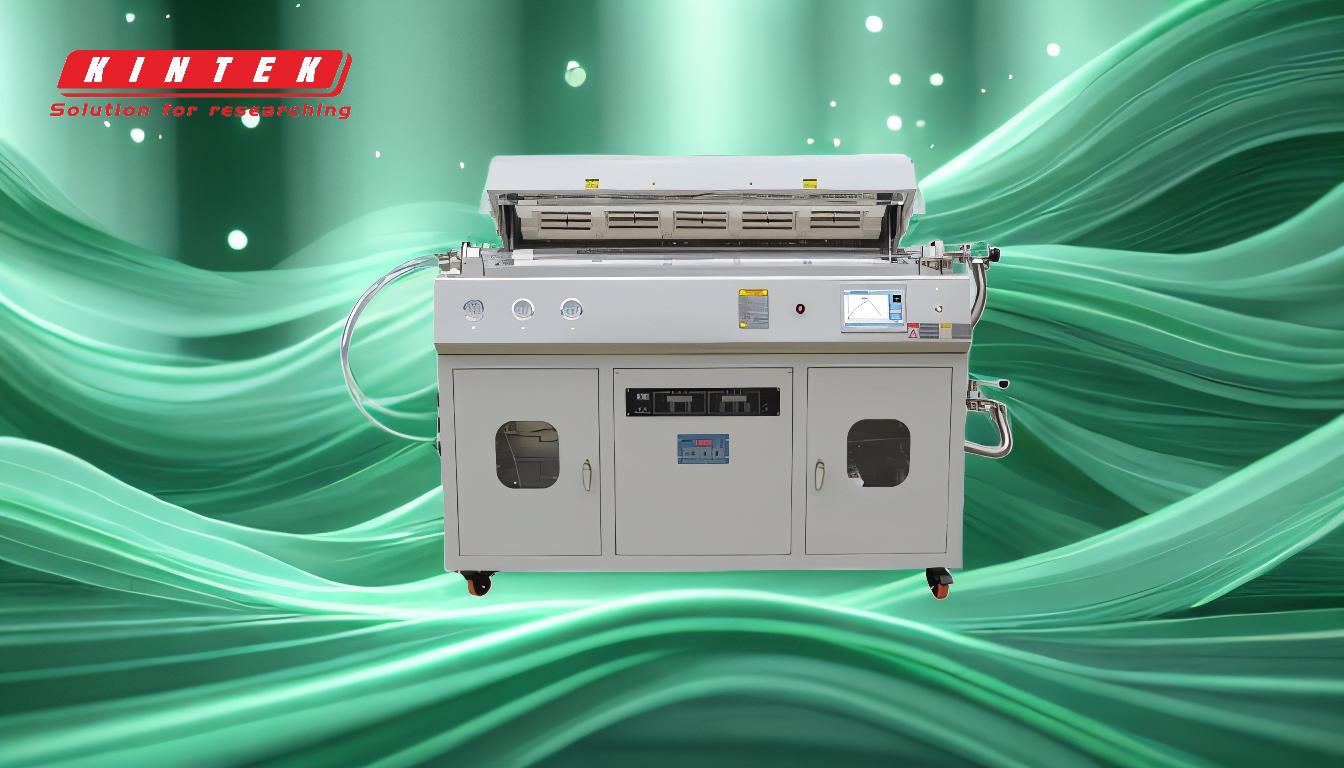
-
PVD Process Overview:
- PVD involves the physical vaporization of a solid material, such as metals, alloys, or ceramics, in a vacuum environment.
- The vaporized material then condenses onto the substrate, forming a thin film.
- Common PVD techniques include sputtering and evaporation, which use low-voltage, high-current arc discharges or thermal energy to vaporize the target material.
- PVD operates at relatively lower temperatures (250°C~500°C), making it suitable for temperature-sensitive substrates.
- The coatings produced by PVD are typically thinner (3~5μm) and exhibit compressive stress due to the lower processing temperatures.
-
CVD Process Overview:
- CVD relies on chemical reactions between gaseous precursors and the substrate surface to form a solid coating.
- The process involves heating the substrate to high temperatures (450°C~1050°C) to drive the chemical reactions.
- CVD can produce thicker coatings (10~20μm) with excellent uniformity and conformality, even on substrates with complex geometries.
- The higher processing temperatures in CVD can lead to tensile stress and fine cracks in the coating, but they also result in denser and more durable films.
-
Key Differences Between PVD and CVD:
- Deposition Mechanism: PVD is a physical process involving vaporization and condensation, while CVD is a chemical process involving gas-phase reactions.
- Temperature: PVD operates at lower temperatures (250°C~500°C), whereas CVD requires higher temperatures (450°C~1050°C).
- Coating Thickness: PVD coatings are thinner (3~5μm), while CVD coatings are thicker (10~20μm).
- Stress in Coatings: PVD coatings exhibit compressive stress, whereas CVD coatings may develop tensile stress due to high-temperature processing.
- Material Range: PVD can deposit a broader range of materials, including metals, alloys, and ceramics, while CVD is typically limited to ceramics and polymers.
- Line-of-Sight vs. Multidirectional Deposition: PVD is a line-of-sight process, meaning the coating is deposited directly onto the substrate, while CVD allows for multidirectional deposition, enabling uniform coverage on complex shapes.
-
Advantages of PVD:
- Lower processing temperatures make it suitable for temperature-sensitive materials.
- Ability to deposit a wide range of materials, including metals, alloys, and ceramics.
- Faster deposition rates compared to CVD.
- Produces coatings with high hardness and wear resistance.
-
Advantages of CVD:
- Produces dense, uniform, and conformal coatings, even on complex geometries.
- Suitable for depositing high-purity materials with excellent adhesion.
- Can achieve thicker coatings, which are beneficial for certain applications.
- Eliminates the need for high-vacuum systems, reducing equipment costs in some cases.
-
Applications of PVD and CVD:
- PVD Applications: Commonly used for decorative coatings, wear-resistant coatings, and semiconductor devices. Examples include tool coatings, optical films, and thin-film solar cells.
- CVD Applications: Widely used in the semiconductor industry for depositing dielectric layers, conductive layers, and protective coatings. Also used for producing diamond-like carbon (DLC) coatings and ceramic coatings in aerospace and automotive industries.
By understanding the processes, differences, and advantages of PVD and CVD, manufacturers can select the most appropriate technique based on their specific application requirements, such as coating properties, substrate compatibility, and operational constraints.
Summary Table:
Aspect | PVD | CVD |
---|---|---|
Deposition Mechanism | Physical process (vaporization and condensation) | Chemical process (gas-phase reactions) |
Temperature Range | 250°C~500°C | 450°C~1050°C |
Coating Thickness | 3~5μm | 10~20μm |
Stress in Coatings | Compressive stress | Tensile stress |
Material Range | Metals, alloys, ceramics | Ceramics, polymers |
Deposition Direction | Line-of-sight | Multidirectional |
Advantages | Lower temperatures, faster deposition, high hardness | Dense, uniform coatings, excellent adhesion, thicker coatings |
Applications | Decorative coatings, wear-resistant coatings, semiconductor devices | Semiconductor industry, DLC coatings, aerospace, automotive industries |
Need help choosing between PVD and CVD for your application? Contact our experts today for tailored solutions!