Biochar is a carbon-rich material produced through the pyrolysis of organic matter, primarily used for soil amendment, carbon sequestration, and environmental remediation. The raw materials for biochar production are diverse and include a wide range of organic feedstocks. These feedstocks are categorized into woody biomass, agricultural residues, green waste, and other organic materials. The choice of feedstock depends on availability, cost, and desired properties of the biochar. Common examples include pine wood, wheat straw, green waste, and dried algae. Understanding the raw materials is crucial for optimizing biochar production and its applications.
Key Points Explained:
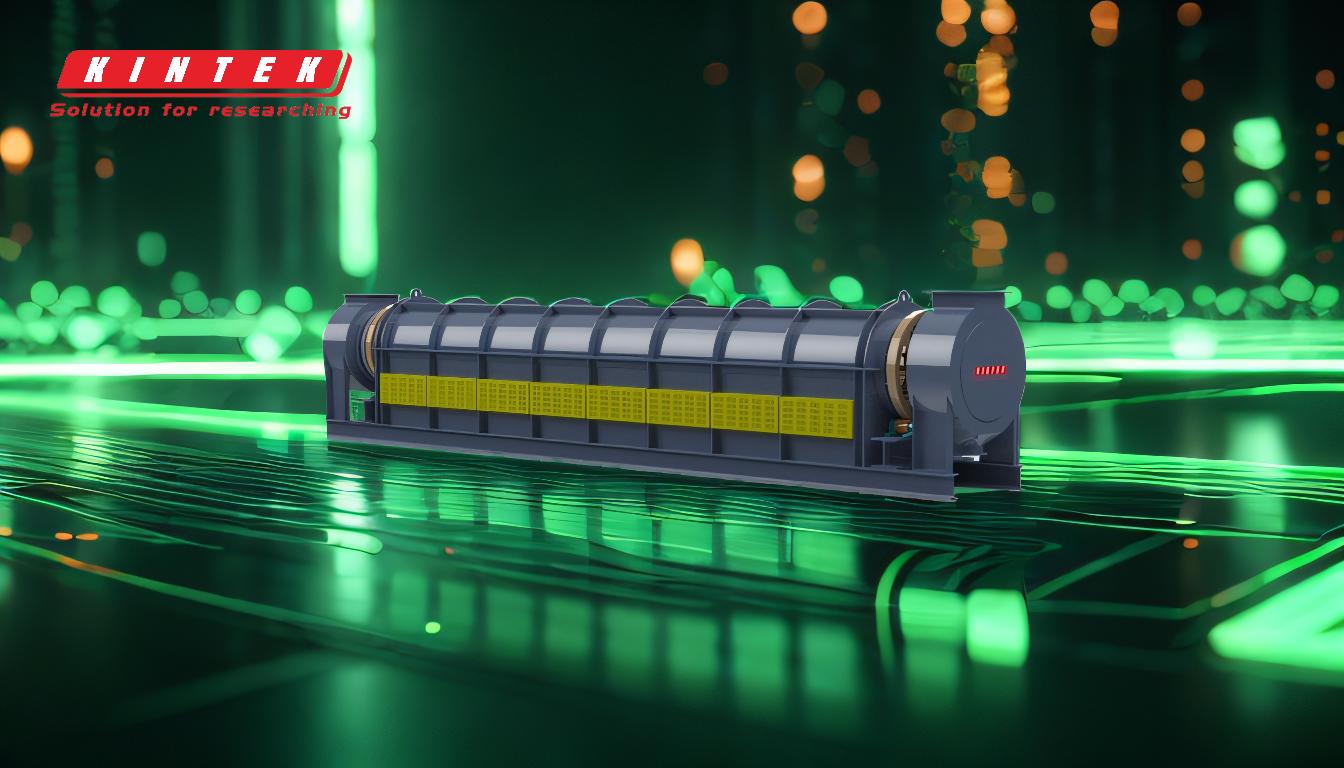
-
Definition of Biochar Feedstocks
- Biochar feedstocks are organic materials that undergo pyrolysis (thermal decomposition in the absence of oxygen) to produce biochar.
- These materials are renewable and can be sourced from various natural and waste streams.
-
Primary Categories of Raw Materials
-
Woody Biomass: Includes materials like pine wood, hardwood, and other types of wood.
- Pine wood is a common feedstock due to its high lignin content, which contributes to stable biochar.
-
Agricultural Residues: Comprises crop leftovers such as wheat straw, rice husks, and corn stover.
- Wheat straw is widely used because it is abundant and a byproduct of agriculture.
-
Green Waste: Includes garden and landscaping waste, such as grass clippings, leaves, and pruned branches.
- Green waste is a sustainable option as it repurposes organic waste that would otherwise decompose or be discarded.
-
Other Organic Materials: Includes unconventional feedstocks like dried algae, manure, and synthetic polymers.
- Dried algae, for example, is gaining attention due to its high carbon content and potential for carbon sequestration.
-
Woody Biomass: Includes materials like pine wood, hardwood, and other types of wood.
-
Factors Influencing Feedstock Selection
- Availability: The feedstock must be locally available to reduce transportation costs and environmental impact.
- Cost: Feedstocks should be cost-effective, often favoring waste materials or byproducts.
- Biochar Properties: The type of feedstock influences the biochar's physical and chemical properties, such as porosity, surface area, and nutrient content.
- Environmental Impact: Sustainable feedstocks, like agricultural residues or green waste, are preferred for their low environmental footprint.
-
Examples of Common Feedstocks
- Pine Wood: A woody biomass with high lignin content, producing stable and porous biochar.
- Wheat Straw: An agricultural residue that is widely available and produces biochar with good nutrient retention properties.
- Green Waste: Includes grass clippings and leaves, which are renewable and contribute to waste reduction.
- Dried Algae: An emerging feedstock with high carbon content and potential for carbon sequestration.
-
Unconventional Feedstocks
- Synthetic Polymers: While not traditional, synthetic polymers can be used for biochar production, though they raise concerns about environmental impact and toxicity.
- Biological Tissues: Includes materials like animal manure or food waste, which can be used but may require additional processing to remove contaminants.
-
Importance of Feedstock Diversity
- Using a variety of feedstocks ensures flexibility in biochar production and allows for tailored biochar properties to meet specific application needs.
- Diverse feedstocks also promote sustainability by utilizing waste materials and reducing reliance on single sources.
-
Environmental and Economic Benefits
- Utilizing waste materials like agricultural residues and green waste reduces landfill use and greenhouse gas emissions.
- Biochar production from renewable feedstocks supports circular economy principles by converting waste into valuable products.
In summary, the raw materials for biochar production are diverse and include woody biomass, agricultural residues, green waste, and other organic materials. The choice of feedstock depends on factors like availability, cost, and desired biochar properties. Common examples include pine wood, wheat straw, and dried algae. Understanding these materials is essential for optimizing biochar production and maximizing its environmental and economic benefits.
Summary Table:
Category | Examples | Key Characteristics |
---|---|---|
Woody Biomass | Pine wood, hardwood | High lignin content, stable biochar, porous structure |
Agricultural Residues | Wheat straw, rice husks | Abundant, cost-effective, good nutrient retention |
Green Waste | Grass clippings, leaves | Sustainable, reduces waste, renewable |
Other Organic Materials | Dried algae, manure | High carbon content, emerging potential for carbon sequestration |
Ready to optimize your biochar production? Contact our experts today for tailored solutions!