Pyrolysis of biomass is a complex thermochemical process that decomposes organic materials at high temperatures (300–900°C) in the absence of oxygen. The process involves multiple reactions, including the breakdown of cellulose, hemicellulose, and lignin into smaller molecules, which form gases, bio-oil, and solid char. Key mechanisms include covalent bond cleavage, depolymerization, fragmentation, and secondary reactions like cracking and recombination of volatile compounds. The process is influenced by temperature, heating rate, and biomass composition, resulting in a range of products such as biochar, bio-oil, and syngas. Understanding these reactions is critical for optimizing pyrolysis for energy recovery and sustainable waste management.
Key Points Explained:
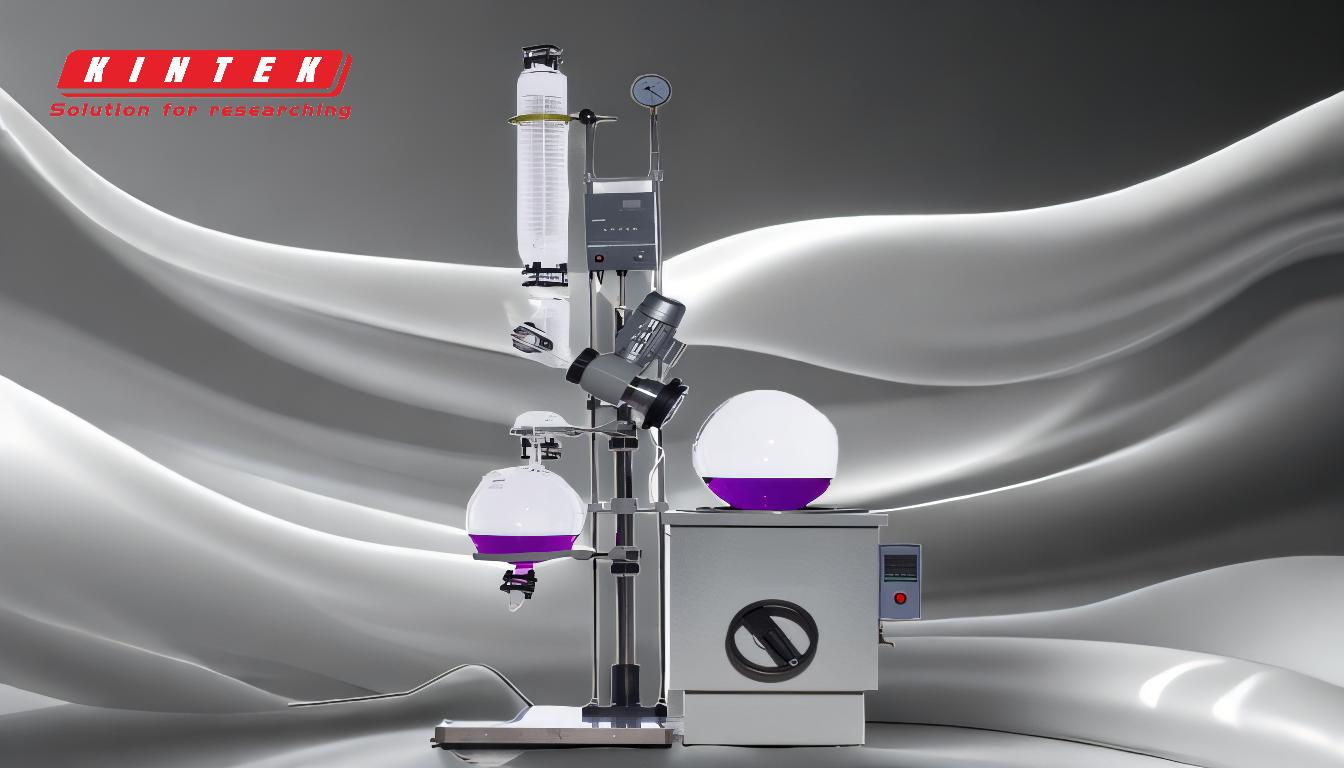
-
Temperature Range and Absence of Oxygen:
- Pyrolysis occurs at temperatures between 300–900°C in the absence of oxygen to prevent combustion.
- This thermal decomposition breaks down biomass into its constituent parts: cellulose, hemicellulose, and lignin.
-
Primary Reactions: Covalent Bond Cleavage and Depolymerization:
- The initial step involves the breaking of covalent bonds within the biomass polymers, releasing reactive free radicals.
- Depolymerization breaks down large polymer chains (e.g., cellulose and hemicellulose) into smaller, volatile molecules.
- Fragmentation further decomposes these molecules into lighter gases, tars, and other intermediates.
-
Secondary Reactions: Cracking, Recombination, and Char Formation:
- Volatile compounds released during primary reactions undergo secondary reactions, including:
- Cracking: Breaking of larger molecules into smaller ones (e.g., light gases like methane and ethane).
- Recombination: Formation of new compounds from reactive intermediates.
- Char Formation: Unstable volatiles may condense to form secondary char, a solid residue.
- Volatile compounds released during primary reactions undergo secondary reactions, including:
-
Product Formation:
- Bio-oil: Condensed volatile compounds form a liquid product rich in organic compounds.
- Syngas: Non-condensable gases, including hydrogen, carbon monoxide, and methane, are produced.
- Biochar: Solid residue composed mainly of lignin and other recalcitrant materials.
-
Influence of Biomass Composition:
- Cellulose and Hemicellulose: These components decompose at lower temperatures, producing more volatile compounds and bio-oil.
- Lignin: Decomposes at higher temperatures, contributing more to char formation due to its complex aromatic structure.
-
Process Steps:
- Pre-treatment: Drying and crushing biomass to optimize pyrolysis efficiency.
- Pyrolysis: Heating biomass to the desired temperature to initiate decomposition.
- Cooling and Condensation: Gases are cooled to separate bio-oil and syngas.
- De-dusting: Cleaning exhaust gases to reduce harmful emissions.
-
Side Reactions:
- In the presence of oxygen or water, side reactions like combustion or hydrolysis may occur, reducing product yield and quality.
- Pyrolysis in an inert atmosphere or vacuum minimizes these side reactions, improving byproduct recovery.
-
Applications and Optimization:
- Pyrolysis is used for converting biomass into renewable energy sources (bio-oil, syngas) and soil amendments (biochar).
- Optimization involves controlling temperature, heating rate, and biomass composition to maximize desired product yields.
By understanding these reactions and mechanisms, stakeholders can design and operate pyrolysis systems more effectively, ensuring efficient biomass conversion and sustainable resource utilization.
Summary Table:
Key Aspect | Details |
---|---|
Temperature Range | 300–900°C in the absence of oxygen to prevent combustion. |
Primary Reactions | Covalent bond cleavage, depolymerization, and fragmentation. |
Secondary Reactions | Cracking, recombination, and char formation. |
Products | Bio-oil, syngas, and biochar. |
Influencing Factors | Temperature, heating rate, and biomass composition. |
Applications | Renewable energy production (bio-oil, syngas) and soil amendments (biochar). |
Optimization | Control temperature, heating rate, and biomass composition to maximize product yields. |
Ready to optimize your biomass pyrolysis process? Contact our experts today for tailored solutions!